by Abhay Kumar Srivastava
6 minutes
Building Thinking Plants: Operational Excellence as a Culture Shift in Pharma
How Operational Excellence and Lean Six Sigma can simultaneously improve quality, reduce costs, and transform pharma culture.
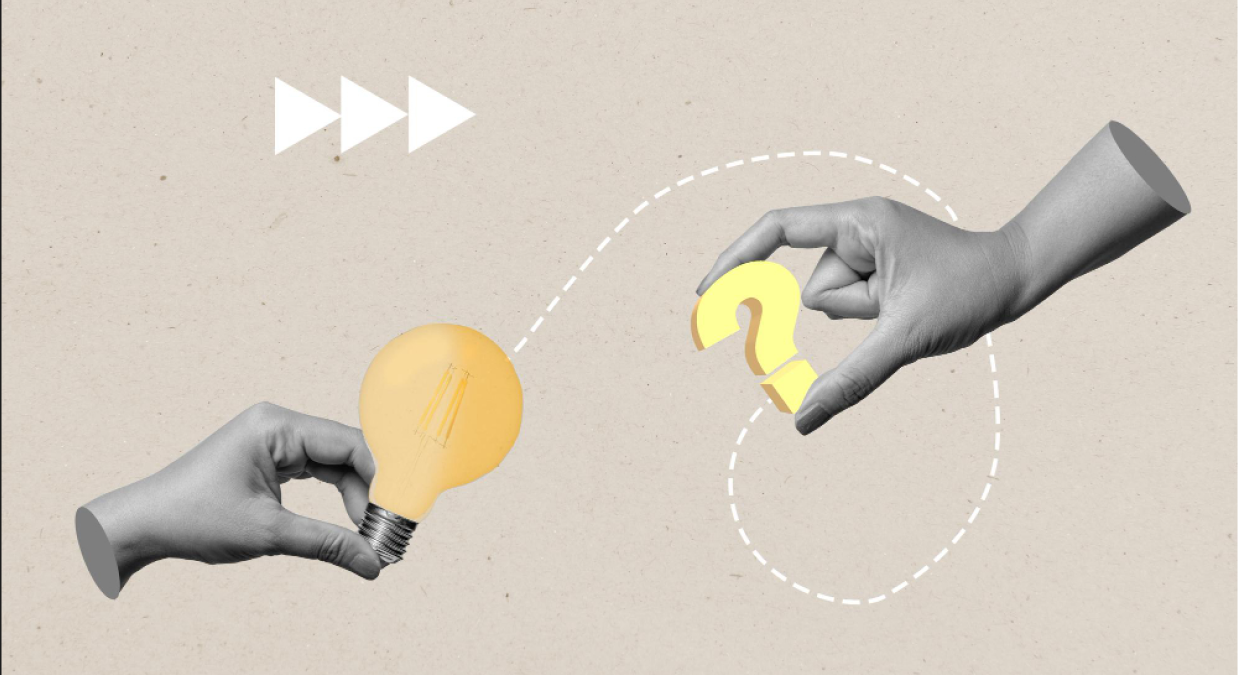
When I joined my previous organization, I began reporting to a senior leader with an engineering background from the IITs and a management degree from IIM or MIT. This shift marked a turning point in my professional journey within the pharmaceutical industry. It made me realize a profound truth: fundamentally, the pharmaceutical industry is like any other—it exists to serve customers (patients).
My new leadership encouraged me to explore best practices from across industries and adapt them to our context. During my research, I discovered the concept of Operational Excellence—a methodology widely used in engineering industries to improve quality while reducing costs. I proposed its adoption, and to my surprise, my superiors were even more enthusiastic than I was—it felt as if they had been waiting for this very idea.
That was when I realized that, despite being process-driven, the pharmaceutical sector had not yet fully embraced structured problem-solving tools like those used in the automotive, aerospace, or electronics industries. Bridging this gap became a personal mission. Today, I am so passionate about this cause that I’ve dedicated my career to promoting Operational Excellence across the pharmaceutical landscape.
Initially, I was confused: how could improving quality reduce costs? My previous understanding was that quality improvements typically increased the cost of goods sold (COGS). To resolve this, I began my own learning journey. I earned Lean Six Sigma Green Belt certification, followed by Black Belt training.
It was during the Black Belt training that I discovered a crucial insight: as you deepen your application of Lean and Six Sigma, quality improves and costs decline. In fact, cost and quality are often inversely related—or not directly correlated at all.
Lean Six Sigma opened my eyes to the reality that most inefficiencies and costs in pharma are due to non-conformances—rework, deviations, recalls, investigations, unplanned downtimes, batch failures, and a “super overkill” compliance mindset. When these are reduced or rationalized, costs naturally fall, quality improves, and operational complexity is reduced.
This realization led me to reflect on why “innovation” and “continuous improvement” are central to every quality policy. Sadly, we often fail to recognize that this is the true spirit behind quality initiatives.
Why Lean Six Sigma Enhances Quality and Reduces Cost
Operational Excellence comprises two pillars: Lean and Six Sigma.
- Lean focuses on eliminating waste or non–value-adding activities. Removing waste refines the process, and refining a process inherently improves its quality. Consider excessive material movement or redundant quality checks—these add no value, prolong timelines, and increase exposure risks. Eliminating them leads to greater speed, standardization, and reduced risk.
- Six Sigma aims to enhance process centricity and reduce variation. Whether it’s assay, weight, or thickness, Six Sigma ensures greater consistency and precision. Lower variation means better quality.
For instance, if an Out-of-Trend (OOT) result consistently points to a specific root cause or special variation, and that issue is addressed, the process becomes more centered and stable. This not only improves quality but also enhances yield and reduces losses from compensatory overages.
If you disagree with this logic, I welcome your counterpoints. But if you’re still with me—let’s go deeper.
The Culture Shift
Despite its clear benefits, I’ve often wondered why many quality leaders in pharma remain indifferent to such initiatives. In contrast, engineering-driven industries embrace Operational Excellence as a core pillar of quality and productivity.
Perhaps it’s because pharma evolved under the umbrella of compliance rather than competition. Quality was viewed more as a regulatory obligation than as a competitive advantage. But Operational Excellence is beginning to change that mindset. While some professionals resist this shift, many companies are now bringing in engineering talent specifically to drive this transformation.
When I joined my current organization, I proposed establishing an Operational Excellence department. Thankfully, I had the support of an open-minded Head of Quality. We began our journey—deliberately and patiently—because, like safety and quality, Operational Excellence is a "software." It requires cultural adoption, not just procedural enforcement.
We curated 26 Lean and Six Sigma principles, tailoring them for the pharmaceutical environment. Last year, we also integrated Total Productive Maintenance (TPM). We began training employees and identifying passionate change agents to be certified as Yellow, Green, and Black Belts—and eventually Master Black Belts (MBBs).
But we didn’t stop at training. We created platforms to track projects, measure impact, and celebrate wins. Tools like visual management boards, dashboards, and monthly Kaizen meets helped sustain momentum.
Within 2–3 years, we reached a critical mass of trained and motivated individuals, triggering a chain reaction of transformation throughout the organization.
As I write this, we have over 150 Green and Black Belts and 18 Master Black Belts. I don’t count Yellow Belts for benchmarking. Over the last three years, these professionals have tackled more than 8,000 problems—turning transactional employees into critical thinkers. Today, I proudly say: we have a thinking plant, not a walking one.
Sustaining the Change
Each problem solved became a case study, helping us institutionalize learning. We built a knowledge repository accessible to all new employees, ensuring our problem-solving DNA outlasts attrition. These are published annually and shared across plants. The best cases are showcased and rewarded at various forums. Recognition and rewards are key drivers of this cultural transformation.
With a workforce of over 2,850 people, imagine the collective impact if each person solved just one problem per year. This would create smoother products, processes, and people—the very essence of a quality culture.
We developed internal Operational Excellence indices to measure maturity—metrics like improvement ideas per person, project completion rate, and new employee engagement. These are now part of our performance reviews.
Ironically, many of these principles are already embedded in regulatory frameworks. Analytical Method Validation (AMV), Quality by Design (QbD), sampling plans, and confidence intervals for process variability all trace their roots to Operational Excellence.
The FDA’s 2011 Process Validation guidance encourages statistical process control and lifecycle approaches—both native to Lean Six Sigma. Other global regulatory bodies like EMA, PIC/S, and CDSCO echo similar sentiments. So I hereby request every one to adopt this.
Results and Vision
This approach has transformed our business—simultaneously improving both quality and cost. Internal surveys show that 67% of our employees solved at least one problem last year, demonstrating the maturity of our operational excellence culture.
Over the past three years, we’ve documented cost savings of ₹160 crore—achieved through waste reduction, yield improvements, cycle time optimization, and better capacity utilization.
My audacious goal? 100% of employees should contribute to problem-solving across products, processes, people, and business operations. I’m optimistic—we’ll get there.
To support this, we’re embedding problem-solving into performance discussions and career progression. For instance, one cannot become a plant manager without being at least a Green or Black Belt.
We are now integrating Digital Transformation with Operational Excellence. Tools like process mining, IoT dashboards, MES systems, and AI-based quality monitoring are making our approach more proactive than reactive.
Looking Ahead
I envision a future where the pharmaceutical industry shifts from a “compliance mindset” to an “excellence mindset.” We must realize that compliance is just a subset of excellence. True excellence lies in solving problems, simplifying operations, and scaling processes—every single day.