by Ravindra Warang
7 minutes
Checkweighers vs Metal Detectors vs X‑Ray: What Does Your Line Really Need?
Compare checkweighers, metal detectors, and X-ray systems to find the right inspection technology for your pharmaceutical production line.
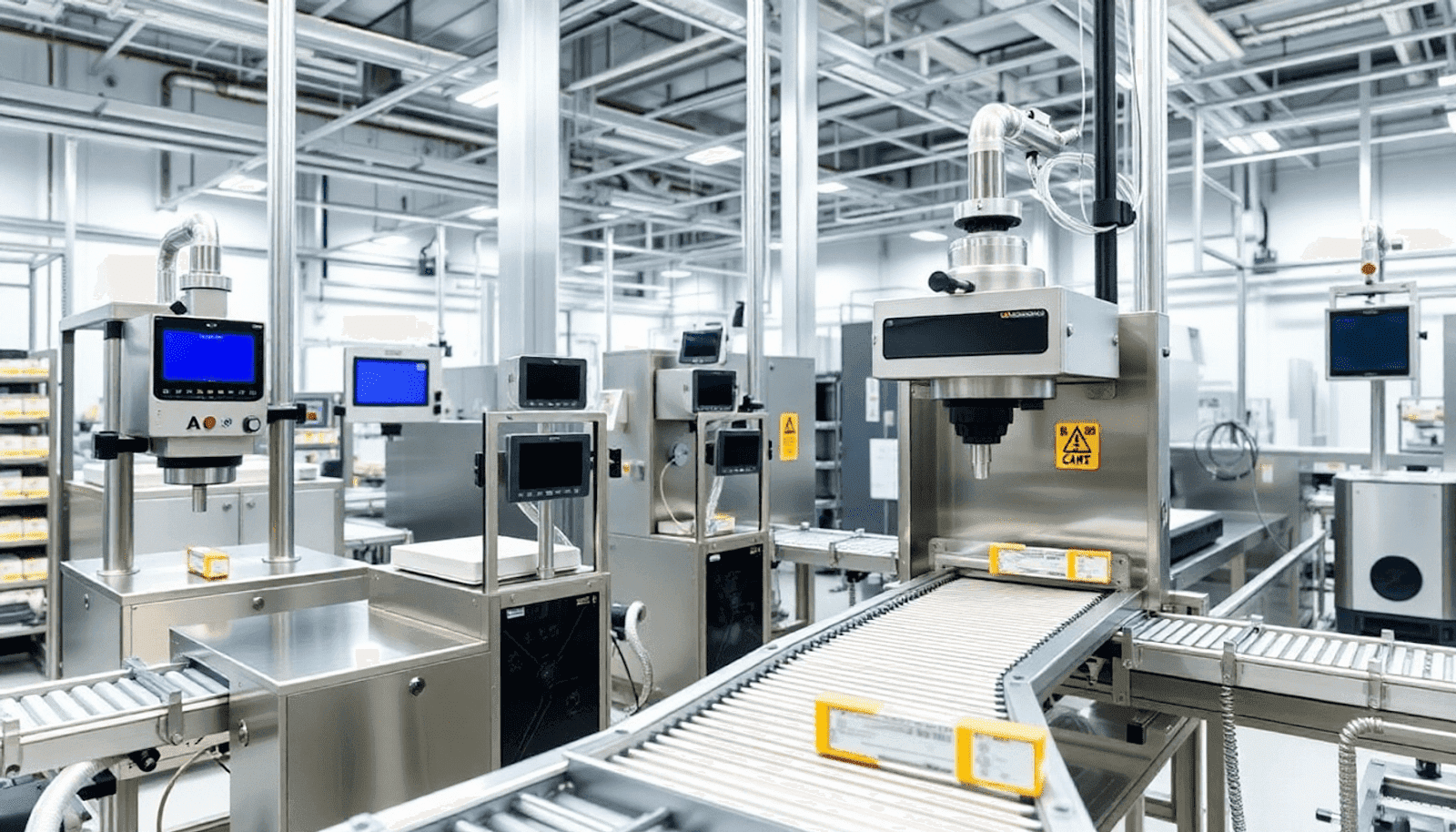
Anika, a Quality Assurance Head at a mid-sized pharma company in Pune, was preparing for a major facility upgrade. With new product lines being added—tablets, capsules, and liquid ampoules—she faced a critical question: Which inspection technologies for pharma should we invest in? A simple online search led to a confusing array of technical terms and conflicting advice. Should they go with pharma checkweighers? Are metal detectors enough, or is an X-ray system essential?
Anika’s dilemma reflects a broader challenge faced by pharma manufacturers when trying to balance regulatory compliance in pharmaceuticals, product safety in pharma, and cost-effectiveness.
In this article, we simplify the three main inspection tools—Checkweighers, Metal Detectors, and X-ray Systems—and assist you in determining which one is best suited for your production line. We'll compare pharma checkweigher vs metal detector vs X-ray systems for pharmaceutical quality control.
Understanding the Basics
Each of these technologies has a specific role in ensuring quality in the pharmaceutical industry. Here's a basic overview:
- Checkweighers: These are important for making sure that each package meets weight requirements. Checkweighers are crucial for maintaining accuracy within +/- 10 mg for aerosol can weighing. They also help optimize the production line by preventing products from being underfilled or overfilled.
- Metal Detectors: These devices are essential for detecting foreign objects in packaging. There are often debates about whether to use metal detectors or X-ray machines since both can identify contaminants. However, it's important to note that metal detectors are specifically designed to find metallic objects.
- X-ray Systems: An X-ray inspection system provides comprehensive analysis capabilities, making it ideal for tasks such as inspecting package inserts. These systems can assess the integrity of packaging while simultaneously checking for foreign objects and ensuring compliance with product safety standards in the pharmaceutical industry.
As Anika considers these options, she must also take into account factors such as IP69K protection class ratings for equipment durability and how tools like Comscale4 software can improve data accuracy across inspections.
Checkweighers: Precision Weight Assurance in the Pharmaceutical Industry
Dynamic checkweighers automatically verify the weight of every product on the production line. In pharmaceuticals, even slight weight deviations can imply underfilled capsules or missing components, which can have compliance and safety implications. By utilizing advanced EMFR weighing technology, these automatic checkweighers ensure dosage uniformity and enhance missing tablet detection effectively.
Key strengths:
- Detects missing tablets or liquids with high accuracy.
- Ensures dosage uniformity, adhering to GMP requirements.
- Integrates with rejection systems for non-compliant units, enhancing QC & productivity solutions.
- Supports checkweigher calibration standards to maintain precision.
- Explores hygienic and legal compliance aspects of weighing systems in regulated industries like pharmaceuticals and food processing.
Incorporating features such as integrated metal detectors in checkweighers and X-ray technology allows for comprehensive formulation package unit inspection and non-destructive inside inspection with X-ray systems. Consider models like the SSV-h Series Checkweigher or Multi-Lane Weighing System to find suitable high-speed options that improve throughput rates of checkweighers while ensuring strict adherence to safety standards.
Metal Detectors: The First Line of Defense in Quality Control
Metal detector technology is essential for identifying ferrous and non-ferrous contamination during mixing or packaging processes. These devices effectively detect ferrous, non-ferrous, and stainless steel contaminants that may compromise product integrity, ensuring compliance with legal requirements for weighing systems in pharma and food sectors.
Key strengths:
- Affordable metal detection solutions that offer high sensitivity to metallic contaminants.
- Widely used in tablet and capsule line inspection, particularly in pharmaceutical manufacturing.
- Critical for maintaining quality and productivity in production lines while preventing underfilling and overfilling.
Learn about metal detectors used in pharmaceutical production and discover modular options to customize weighing systems with additional inspection capabilities such as x-ray technologies for quality control in production lines.
X-ray Inspection Systems: Comprehensive Contaminant Detection
X-ray inspection systems go beyond metal detection. They are essential for comprehensive contaminant detection, capable of identifying glass, stone, high-density plastic, and even fill level deviations.
Key strengths:
- Detects non-metallic and metallic contaminants.
- Useful for ampoules, blister packs, and vials.
- Can perform component verification and count detection.
Application by Product Type
Each technology is better suited to certain product formats. Here's a breakdown of application by product type:
Tablets/Capsules:
- Use pharma checkweighers for weight consistency
- Metal Detectors for ferrous/non-ferrous contaminants
- Optional X-ray inspection systems for foreign object detection in blister packs
Ampoules/Liquids:
- X-ray inspection systems are ideal for fill level and glass detection
- Checkweighers ensure uniform fill volume
- Metal detectors are limited due to the glass/metal container
Powders:
- Metal Detectors work best in bulk stages
- Checkweighers ensure sachet/pouch weight accuracy
Compliance & Regulatory Considerations
In regulated markets, equipment must not only perform well but also support compliance. Here’s how they stack up in terms of compliance and regulatory considerations:
- Checkweighers often help meet FDA and EU GMP guidelines by ensuring content uniformity.
- Metal Detectors are commonly referenced in guidelines for general product safety.
- X-ray Systems must be validated and justified under risk-based approaches, especially in Europe.
Digital audit trails in inspection technology and 21 CFR Part 11 compliance features are increasingly integrated across all three technologies.
Operational Limitations and Costs
Understanding operational limitations of inspection systems helps avoid costly surprises:
- Checkweighers:
- Cannot detect foreign objects
- May struggle with unstable containers
- Metal Detectors:
- Can't detect glass, stones, or plastics
- Limited by moisture and product effect
- X-ray Systems:
- High initial investment and maintenance cost
- Radiation safety in X-ray systems compliance needed
Comparison Table: Checkweigher vs Metal Detector vs X-ray System
Feature
Pharma Checkweigher
Metal Detector
X-ray System
Detects Weight Variations
✅ Yes
❌ No
✅ Yes (to an extent)
Detects Metal Contaminants
❌ No
✅ Yes
✅ Yes
Detects Non-Metal Contaminants
❌ No
❌ No
**✅
FAQs (Frequently Asked Questions)
Q1. What roles do checkweighers play in pharmaceutical quality assurance?
Checkweighers verify product weight, detect missing tablets or liquids, ensure dosage uniformity, and integrate with rejection systems to maintain consistent product quality. They are essential for meeting FDA and EU GMP guidelines related to content uniformity compliance.
Q2. How do metal detectors contribute to contaminant detection in pharma manufacturing?
Metal detectors identify ferrous, non-ferrous, and stainless steel contaminants with high sensitivity. They are affordable, widely used in tablet and capsule production lines, and referenced in regulatory guidelines for general product safety compliance. However, their effectiveness can be limited by factors like moisture and the presence of metal containers.
Q3. What advantages do X-ray inspection systems offer in pharmaceutical production?
X-ray systems detect glass, stone, high-density plastic contaminants, as well as fill level deviations. They can identify both metallic and non-metallic foreign objects, making them ideal for inspecting ampoules, blister packs, and vials. Despite higher initial investment and maintenance costs, they provide critical detection capabilities not achievable by other technologies.
Q4. Why is a combination of inspection technologies recommended for pharma facility upgrades?
Each technology addresses specific inspection needs: checkweighers ensure weight consistency in tablets/capsules; metal detectors are effective at detecting metal contaminants during bulk powder stages; X-ray systems excel at detecting foreign objects and fill level deviations in ampoules and blister packs. Combining these ensures comprehensive quality control across different production stages.
Q5. What limitations should be considered when selecting inspection technologies for pharmaceutical lines?
Checkweighers cannot detect foreign objects or handle unstable containers; metal detectors may have reduced sensitivity due to moisture or product effects; X-ray systems require significant initial investment, ongoing maintenance costs, and adherence to radiation safety protocols. Understanding these limitations helps optimize technology selection for specific production needs.