by Ravindra Warang
7 minutes
Understanding IQ/OQ/PQ for Pharma Checkweighers: Qualification Without the Stress
Your stress-free guide to IQ/OQ/PQ qualification for pharma checkweighers—compliance made practical.
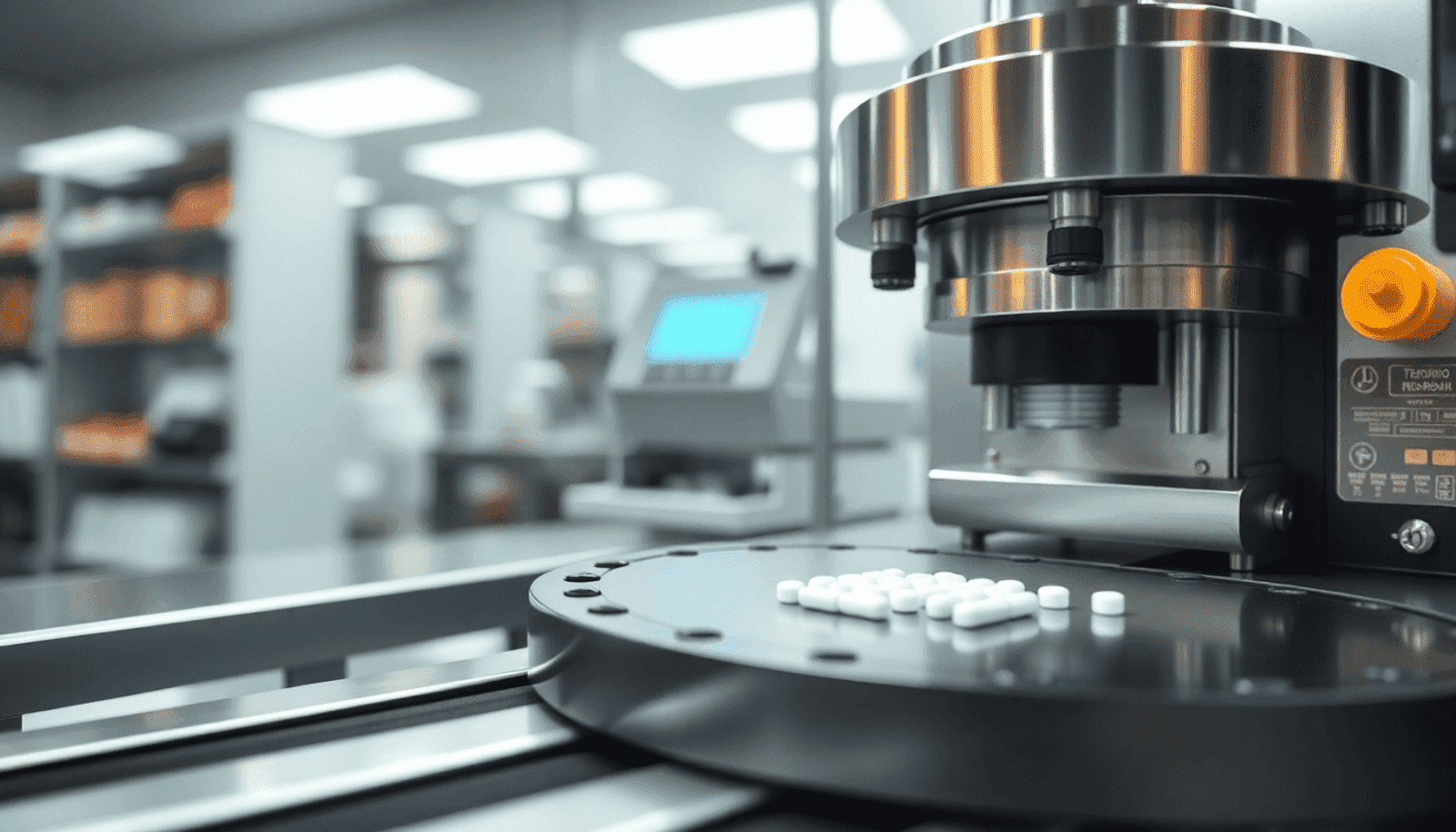
A QA manager at a mid-sized pharmaceutical plant noticed issues with the weight readings from a newly installed checkweigher on a busy Monday. This caused production to stop and panic to set in, especially with a regulatory audit coming up in just a week. The problem? Even though the machine was top-of-the-line, the protocol for qualifying the checkweigher had been ignored.
In the world of pharmaceuticals, where equipment must be both precise and properly documented, this situation highlights the critical importance of equipment qualification. In this article, we'll take an in-depth look at IQ OQ PQ for pharma checkweighers—explaining what it means and how to master it without stress.
We'll cover:
- The key stages of performance qualification (PQ) in validating pharmaceutical manufacturing equipment
- Best practices for ensuring compliance in pharmaceutical manufacturing
- The significance of quality assurance in pharmaceutical plants
- Tips for preparing for regulatory audits
Whether you're familiar with specific equipment like Taylor-Wharton Cryogenic Freezers or basic operations involving pharma x-ray systems, grasping these essential processes is crucial for maintaining integrity and efficiency in your operations.
Join us as we explore the complexities of IQ/OQ/PQ for checkweighers and empower yourself with the knowledge needed to effectively operate and maintain pharmaceutical x-ray inspection systems while keeping accurate audit records.
What Is Equipment Qualification and Why Does It Matter?
The equipment qualification process is essential in ensuring that any pharmaceutical manufacturing equipment operates correctly and consistently as intended. This is particularly crucial for tools like checkweighers, which verify the weight of tablets, capsules, or vials—where every gram counts.
Regulatory bodies in pharma, such as the US FDA, EMA, and WHO, mandate this qualification as a key component of Good Manufacturing Practices (GMP). Proper equipment qualification not only ensures compliance but also safeguards data integrity in pharmaceutical production. Poorly qualified machines can lead to significant risks, including:
- Data integrity violations
- Product recalls
- Regulatory penalties
- Batch rejection risks
To effectively navigate the equipment qualification process, it's important to identify roles and responsibilities involved in pharma equipment qualification processes. This includes understanding the critical stages such as DQ (Design Qualification) and ensuring that robust systems are in place for user authentication in pharma systems.
By prioritizing pharmaceutical checkweigher qualification and adhering to established GMP guidelines, companies can enhance product recall prevention efforts and regulatory penalties avoidance.
Understanding IQ, OQ, and PQ
The breakdown of IQ, OQ, and PQ is crucial for ensuring the quality assurance of pharmaceutical products. These qualification stages—Installation Qualification (IQ), Operational Qualification (OQ), and Performance Qualification (PQ)—are essential in the validation processes of equipment.
1. Installation Qualification (IQ)
This stage verifies that the equipment is installed correctly according to the specified guidelines, such as the Freezer Specification Sheet and the General Arrangement Drawing. For instance, when setting up a Pharmaceutical X-ray Inspection System, it's vital to ensure that all components are positioned as per the manufacturer's instructions.
2. Operational Qualification (OQ)
During OQ, you assess whether the equipment operates according to its intended use under normal conditions. This includes checking various parameters and ensuring that audit trails in pharmaceutical inspections are maintained effectively. For example, when using a Mowden Controller, it's important to validate that it responds accurately to set inputs.
3. Performance Qualification (PQ)
The final stage, PQ, determines if the equipment performs consistently and reliably while producing quality products. In this phase, real-world testing is conducted to ensure that the machinery meets predefined performance criteria.
By systematically addressing these IQ OQ PQ breakdown stages, System Owners can ensure that their processes remain compliant and efficient throughout the production cycle. Additionally, understanding pharma checkweigher qualification stages is vital for maintaining accuracy in weight measurements and overall product integrity.
Installation Qualification (IQ)
Installation Qualification (IQ) ensures that your checkweigher is installed correctly and complies with manufacturer and regulatory specifications. This process is crucial for maintaining GMP compliance, especially in industries like pharmaceuticals where IQ OQ PQ for pharma checkweighers is standard practice.
Key IQ Activities:
- Verifying location suitability for checkweighers (humidity, power supply, vibration control)
- Completing the checkweigher installation checklist as per manufacturer guidelines
- Reviewing calibration certificates to ensure part verification
- Documentation of software and firmware documentation, including current versions
- Ensuring data security in pharma inspections through proper record-keeping
Engaging with a Manufacturer’s Representative can further streamline these Installation Qualification (IQ) activities, ensuring that all aspects are thoroughly addressed.
Operational Qualification (OQ)
Operational Qualification (OQ) validates that the checkweigher operates as expected within specified parameters. This process is essential for ensuring compliance with FDA 21 CFR Part 11 and maintaining FDA audit readiness.
Key OQ Checks:
- Testing checkweigher alarm systems testing and rejection systems
- Running the equipment under simulated load conditions for OQ
- Verifying weight accuracy using certified test weights verification
- Checking HMI functionality checks to ensure proper operation
These Operational Qualification testing procedures are critical for effective product defect detection and should be documented in the Manufacturing Quality Traveler. Additionally, ensure that all cleaning and maintenance of x-ray systems is conducted regularly to uphold quality standards.
Performance Qualification (PQ)
Performance Qualification (PQ) tests the checkweigher under actual production conditions over an extended period, ensuring checkweigher reliability verification and adherence to Cryogenic freezer system acceptance criteria.
Key PQ Tasks:
- live production batch sampling using representative weights
- Verifying reproducibility and reliability
- Stress-testing for product types or formats, including missing tablet detection scenarios
- Documenting any deviations and resolutions through thorough deviation documentation in PQ processes
These Performance Qualification (PQ) tasks are essential for maintaining quality standards and ensuring that all equipment functions correctly within its intended parameters. Additionally, vendor support in IQ OQ PQ activities can greatly enhance the effectiveness of these qualifications.
For more information on best practices, consider resources from institutions like Nagoya City University.
The Qualification Protocol Blueprint
To streamline the IQ OQ PQ protocol development process, a clear qualification protocol blueprint must be developed. This protocol acts as your roadmap for ensuring compliance and quality in pharmaceutical testing.
Must-Have Components in a Qualification Protocol:
- Qualification objectives and scope
- Equipment details and drawings, including specifications for IQ OQ PQ for pharma checkweighers
- Test plans and acceptance criteria that address chipped tablet detection and other critical factors
- Deviation handling procedure to manage any inconsistencies
- Final approval checklist to ensure all criteria are met before sign-off
A collaborative effort between QA, validation engineers, and equipment vendors is essential, especially when considering guidelines set by the World Health Organization (WHO) and conducting pharmaceutical testing after x-ray exposure.
Common Qualification Mistakes in Pharma (and How to Avoid Them)
- Skipping Vendor Involvement in OQ: Always involve the equipment supplier during the Operational Qualification (OQ) process to ensure that all specifications are met and that you adhere to best practices.
- Poor Documentation: Incomplete or inconsistent documentation can nullify even the most thorough tests. Follow documentation best practices to maintain clarity and compliance in your qualification documentation and appendices.
- Neglecting Re-Qualification: If equipment has been moved or modified, be sure to address re-qualification requirements immediately. This is crucial for maintaining integrity in processes like acetaminophen package checks.
- Ignoring Software Validation for Checkweighers: Modern checkweighers that utilize AI/IoT technology require thorough software validation. Ensure that your validation process includes assessment of safety mechanisms for x-ray machines if they are part of the workflow.
By being aware of these common qualification mistakes in pharma, you can streamline your processes and ensure compliance with industry standards.
Role of Vendors in IQ/OQ/PQ
Vendors play a crucial role in the IQ OQ PQ process, especially when working with leading checkweigher brands such as Mettler Toledo, Wipotec, and Anritsu. These companies often provide comprehensive support packages that include:
- On-site execution of Installation Qualification (IQ) and Operational Qualification (OQ) to ensure proper installation
- Pre-validated templates and documents for efficient compliance
- Calibration kits for checkweighers to maintain accuracy
- Training for plant teams to familiarize them with processes and standards
By involving the vendor early on, it reduces stress and ensures compliance with current regulations such as 21 CFR Part 11. This is particularly important when considering factors like x-ray radiation safety standards and the implementation of high sensitivity and stability x-ray inspection techniques.
Integrating Digital Tools for Paperless Qualification
The future is digital. Innovative digital tools for paperless qualification are transforming the way the pharma industry operates. Platforms now offer cloud-based validation systems that:
- Track version control in qualifications
- Auto-log calibration data
- Provide requalification deadline alerts
- Create audit trails with electronic signatures
Some pharma plants have already cut qualification timelines by 30% using these advanced tools. By streamlining the IQ OQ PQ for pharma checkweighers and adhering to calibration and certification requirements in pharma equipment qualification, these systems ensure compliance and efficiency.
Additionally, integrating these technologies can enhance processes such as mefenamic acid production and improve x-ray image quality while maintaining operator safety protocols.
Qualification and Regulatory Audits
Auditors often closely examine qualification records during regulatory audits to assess the following:
- Whether protocols align with equipment specifications and ensure traceability between protocols and equipment specs
- How deviations were handled and whether effective deviation handling was implemented in audits
- The traceability of test results to batch records, ensuring batch records can be traced back
- The training records of personnel involved, with a specific focus on personnel training records in audits
Well-maintained Installation Qualification (IQ), Operational Qualification (OQ), and Performance Qualification (PQ) documentation—especially for pharma checkweighers or similar equipment—often sets the stage for a smooth inspection.
For those looking to improve their processes, find detailed protocols and checklists for qualifying pharmaceutical equipment according to industry standards. Additionally, consider obtaining sample qualification documentation templates for Design Qualification (DQ) and OQ that incorporate best practices for product integrity verification and x-ray leakage prevention curtains.
Understanding the features and benefits of pharmaceutical x-ray inspection systems is also crucial during regulatory assessments.
IQ/OQ/PQ Activities vs Expected Documentation
This table outlines the essential IQ OQ PQ activities documentation required during the qualification process. Ensure compliance with FDA regulations for pharma inspection equipment while conducting installation checks and functional testing.
Qualification Stage Activities Key Documentation IQ (Installation Qualification)
Installation checks (documentation for freezers), power validation
OQ (Operational Qualification)
Functional testing (of freezer controllers), safety features
PQ (Performance Qualification)
Real production runs, reproducibility (batch run data analysis)
Additional Documentation
In addition to the above, the following documents are also critical:
- Calibration reports and utility drawings for IQ
- Test reports and deviation logs for OQ
- Batch run data and analysis summary for PQ
Conclusion: From Compliance Burden to Strategic Advantage
Let’s go back to that QA manager. After the audit, the plant received zero observations—thanks to a crash course in IQ OQ PQ value-adding processes and strong vendor support.
What was once seen as a compliance burden is now recognized as a strategic advantage. Proper qualification through IQ OQ PQ for pharma checkweighers builds equipment trust, avoids downtime in pharma, and provides risk shielding for pharma firms. With the right tools and mindset, these processes can become less about paperwork and more about performance-focused qualification.
Additionally, when considering DQ IQ OQ PQ protocols for cryogenic freezers, it's essential to understand the role of PQ in pharmaceutical cryogenic freezers. Ensuring that X-ray ON/OFF keys are functioning correctly can significantly contribute to false reject reduction. Moreover, learning about safety measures for X-ray inspection in the pharma industry is crucial for maintaining quality and compliance standards.
FAQs: SEO-Optimized for Real Search Behavior
Q1. What is IQ/OQ/PQ in pharmaceutical checkweighers?
IQ/OQ/PQ for pharma checkweighers refers to the three-step qualification process—Installation (IQ), Operational Qualification (OQ), and Performance Qualification (PQ)—that ensures a checkweigher works as intended within the Manufacturing Process with Quality Check Points.
Q2. What are common IQ/OQ/PQ mistakes to avoid? Skipping software validation, poor documentation, not involving the vendor, and ignoring requalification are frequent issues—these are some of the common IQ OQ PQ mistakes to avoid.
Q3. Why is equipment qualification critical for checkweighers in pharmaceutical manufacturing?
Equipment qualification ensures that checkweighers perform correctly and consistently, verifying the weight of tablets, capsules, or vials as mandated by FDA, EMA, and WHO guidelines. Proper qualification prevents data integrity violations, product recalls, regulatory penalties, and batch rejection.
Q4. What are the main stages of checkweigher qualification and their purposes?
The three main stages are IQ (Installation Qualification), which verifies installation compliance with manufacturer and regulatory specifications; OQ (Operational Qualification), which validates operation within specified parameters such as alarm systems and weight accuracy; and PQ (Performance Qualification), which tests the checkweigher under actual production conditions to ensure reproducibility and reliability.
Q5. How do top checkweigher brands support pharmaceutical plants in the qualification process?
Leading brands offer on-site IQ/OQ execution services, provide pre-validated templates and documentation, supply calibration kits, and deliver training for plant teams to ensure smooth and compliant qualification processes.
Q6. What role do digital tools play in the checkweigher qualification process?
Digital tools facilitate cloud-based validation systems enabling paperless qualification with features like version control tracking and automatic logging of calibration data, enhancing accuracy, traceability, and ease of documentation management during audits.