by Ravindra Warang
7 minutes
Everything You Need to Know About Alu-Alu Blister Packaging in Pharma
Discover why Alu-Alu blister packaging is the gold standard for moisture-sensitive and high-value pharmaceutical products.
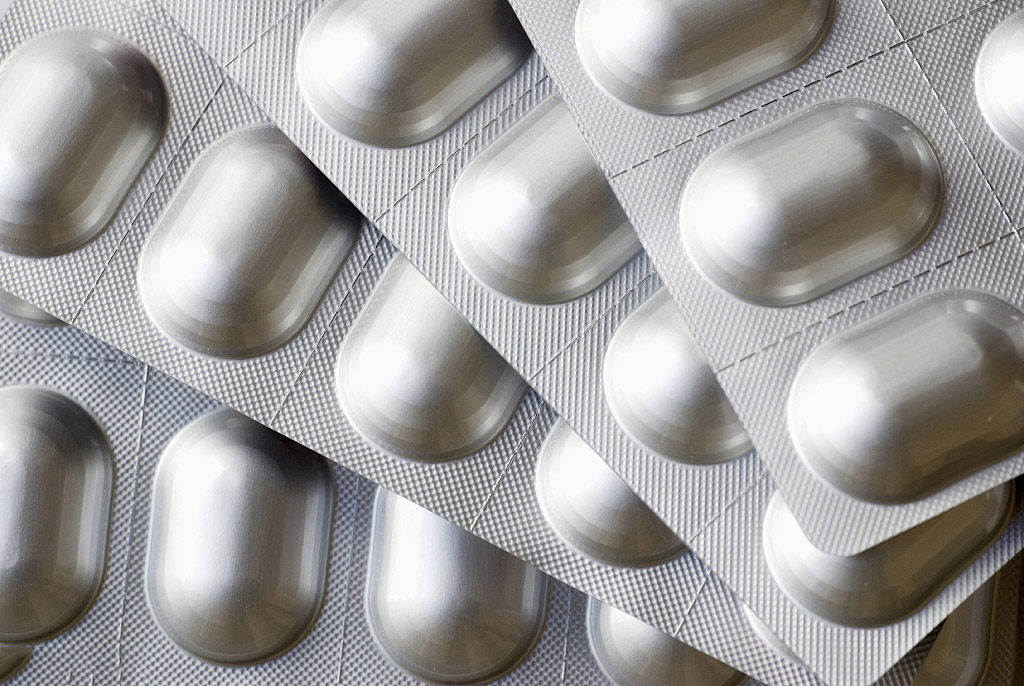
Image Source: Aipak Pharma
In a Normandy warehouse, a batch of potent antiviral tablets failed stability testing due to high humidity fluctuations. The tablets, packed in standard PVC blisters, lost significant potency—a risk to both patient safety and regulatory compliance in pharma packaging. In response, the sponsor urgently switched to Alu‑Alu (cold‑form) blister packaging. This decision, though costly, proved essential, reinforcing one truth: for moisture-sensitive pharmaceuticals and high-value drugs, Alu‑Alu blister packaging remains irreplaceable.
Alu‑Alu offers a premium level of barrier protection in drug packaging that is unmatched by other blister types. This guide explores its structure, manufacturing processes, compliance rules, pros and cons, cost considerations in blister packaging, and emerging trends in pharmaceutical packaging across a detailed 2,000-word overview. Discover the advantages of Alu-Alu packaging and why it is crucial for maintaining the integrity of moisture-sensitive pharmaceuticals.
What Is Alu-Alu Blister Packaging?
Alu‑Alu blister packaging, often called cold‑form blister, utilizes a specific alu-alu blister pack composition that includes aluminum foil for both the base and lid. The base typically consists of a three-layer laminate: oriented polyamide (OPA) for strength and resilience during forming; an aluminum core for excellent barrier protection; and a seal layer—usually PVC or a PVC‑free alternative—that bonds with the lidding foil. This careful arrangement ensures the durability of alu-alu blisters.
The manufacturing process of alu-alu blister packs begins with the cold forming process, where the base laminate is stamped into precise cavities at room temperature. Tablets are then inserted, followed by heat sealing in blister packs with a compatible aluminum lidding foil under heat and pressure. Finally, the packs are cut, printed, and readied for distribution. Unlike thermoformed packs that use clear plastics, Alu‑Alu blisters are opaque but exceedingly durable, making them an ideal choice for sensitive medications and products that require enhanced protection. This contrast highlights the advantages of alu-alu packaging in terms of durability compared with thermoformed packs.
Why Alu-Alu Is Essential in Pharma
Alu-Alu packaging plays a crucial role in the pharmaceutical industry due to its unique properties that ensure the safety and efficacy of medications. One of the key reasons for its importance is its excellent moisture and oxygen barrier properties, which protect sensitive drugs from degradation.
Additionally, Alu-Alu packaging provides light protection in drug packaging, safeguarding products from photodegradation caused by exposure to sunlight. This is particularly vital for applications of alu-alu in steroids and oncology medications, where maintaining the integrity of the active ingredients is essential.
Furthermore, the chemical and microbial resistance offered by Alu-Alu materials helps prevent contamination and ensures that the drugs remain stable throughout their shelf-life. By extending shelf-life with alu-alu packaging, manufacturers can guarantee that medications retain their potency until they reach the end user.
Tamper-evident security in pharma packs is another important feature of Alu-Alu packaging, providing an additional layer of safety for patients. This is especially critical in an industry where mechanical hazards and product integrity are paramount.
In summary, the importance of alu-alu in pharmaceuticals cannot be overstated, as it effectively addresses various challenges such as moisture control, light exposure, chemical stability, and security—making it an indispensable choice for modern drug packaging solutions.
Moisture & Oxygen Barrier
The aluminum core in Alu‑Alu blister packaging creates an impermeable shield against water vapor and oxygen—two major causes of drug degradation. This moisture barrier in drug packaging is essential for highly moisture-sensitive drug formulations, as it ensures optimal drug stability by providing protection against moisture, oxygen, and light. The aluminum core benefits include its ability to prevent drug degradation and maintain the integrity of pharmaceuticals by offering effective oxygen protection in pharmaceuticals.
Light Protection in Pharmaceutical Packaging
Unlike clear thermoformed blister packs, Alu‑Alu is completely opaque, providing superior light protection in pharmaceutical packaging. This opacity effectively shields medications from harmful UV light exposure that could degrade sensitive compounds and lead to the formation of degradation products.
By preventing exposure to visible light and UV rays, Alu-Alu blisters ensure that the integrity of the active ingredients is maintained, making them an ideal choice for products that require strict control of relative humidity (RH) and light conditions.
Additionally, when used in conjunction with desiccants like silica gel canisters or silica gel packets, these opaque blister packs offer enhanced protection against moisture and further safeguard the quality of sensitive pharmaceuticals.
Chemical & Microbial Resistance
The foil's chemical resistance in drug packaging is crucial for preventing chemical contamination and ensuring the stability of active pharmaceutical ingredients (API) within. Its robust structural integrity—characteristic of alu-alu blisters—combined with tight seals in pharmaceutical packs, effectively safeguards against microbial contamination, thus playing a vital role in microbial contamination prevention. These features are essential for protecting patient safety and maintaining the potency of sensitive formulations that may contain excipients like microcrystalline cellulose, lactose, and croscarmellose sodium. Additionally, the tamper resistance offered by these seals ensures that the integrity of the product remains uncompromised throughout its lifecycle.
Shelf-Life Extension
Alu‑Alu blister packaging extends a product’s shelf life significantly through its exceptional barrier properties for supply chain stability. These properties are crucial in maintaining efficacy during long supply chains or unstable climatic conditions, ensuring climatic condition resilience in drug storage. By effectively protecting against moisture and oxygen, Alu-Alu packaging plays a vital role in pharmaceutical shelf-life management.
Additionally, when considering shelf-life extension with blister packaging, it's important to explore how desiccants improve shelf-life in pharmaceutical packaging. For instance, the presence of magnesium stearate in formulations can influence the overall stability of the product while complementing the protective qualities of Alu-Alu packaging.
Tamper-Evident Security
Aluminum-aluminum blister packaging, commonly known as Alu‑Alu, requires deliberate access, offering robust security against unauthorized access to medications. The tamper-evident features of Alu‑Alu blisters ensure that any rupture in the aluminum seal is instantly noticeable, making tampering rare. This integrity of the aluminum seal is crucial in maintaining the safety and efficacy of sensitive products.
This combination of protection against environmental hazards and structural strength explains why Alu‑Alu remains the standard for steroids, oncology medications, hormones, and high-value OTCs like enzymes or antioxidants. Additionally, when considering the stability of pharmaceuticals packaged in Alu‑Alu, it's essential to explore accelerated stability assessment methods like ASAP. These methods can provide valuable insights into how factors such as moisture sorption and relative humidity effects inside packages influence the overall quality of the medications.
For products that require alternative packaging solutions, high-density polyethylene (HDPE) bottles are often considered due to their durability and resistance to various environmental factors. However, the unique properties of aluminum blister packs make them indispensable in preserving the integrity of sensitive pharmaceutical formulations.
Comparative Analysis: Alu-Alu vs. Other Blister Types
In this comparative analysis of blister pack types, Alu‑Alu blisters outperform competitors while acknowledging trade‑offs when compared to options like Alu-PVC blisters and PVC/PVDC packs:
- Barrier Performance: In the barrier performance comparison, Alu‑Alu provides the strongest protection against moisture, oxygen, and light. In contrast, Alu‑PVC offers a partial barrier, while polyvinylidene chloride (PVDC) is adequate only for low-sensitivity drugs.
- Opacity: Opacity differences in blister packs are significant; Alu‑Alu offers complete opacity compared to the clarity of other packs.
- Cost & Speed: When considering cost and speed considerations in production, Alu‑Alu is costlier and slower to produce but justified for critical products.
- Recyclability: The recyclability of aluminum vs. mixed-material packs is notable, as the aluminum-only structure makes Alu‑Alu more environmentally friendly than those that combine different materials.
This analysis highlights the unique advantages of Alu-Alu blister packaging in various essential aspects.
Material Science & Laminate Structures in Blister Packaging
Material science in alu-alu foils utilizes varied laminate structures to optimize performance:
- Standard three-layer structures (OPA/Al/PVC) balance durability and sealing, making them essential in alu-PVC blister pack benefits and drawbacks.
- Enhanced versions add additional PVC layers, improving film rigidity and handling while ensuring effective cold forming.
- Emerging PVC-free laminates like OPA/Al/PE are gaining traction due to improved recyclability—though sealing characteristics may differ.
Key technical parameters include consistent wall thickness to ensure uniform sealing, quality lacquer systems to prevent delamination, and foil thickness optimization for cold-form processing. These factors are crucial in maintaining barrier protection while allowing efficient production processes.
Manufacturing Equipment & Quality Controls
Producing Alu‑Alu blisters requires specialized manufacturing equipment for Alu-Alu blisters and rigorous quality controls in blister pack production. Cold‑form blister machines mold cavities using image and depth sensors and operate slower than thermoforming lines. These machines are essential in the packaging manufacturing process to ensure precise shaping of the blisters.
Heat sealing systems are carefully calibrated for precise temperature, pressure, and dwell time, ensuring that the integrity of the blisters is maintained. Clean, dust-free environments are essential, as even micrometer defects in foil can compromise integrity.
During the manufacturing process of alu-PVC blister packs, inline visual inspections, automated seal-testing, and dimensional checks maintain quality throughout production. Each shift performs statistical checks—including seal peel strength and moisture barrier testing—to ensure consistent performance and adherence to quality standards.
Regulatory Compliance
Ensuring regulatory compliance for alu-alu packaging is essential in the pharmaceutical industry. Adhering to global standards for pharmaceutical packaging not only guarantees the safety and efficacy of the products but also aligns with key guidelines such as the WHO Annex 9 guidelines.
When developing high barrier blister packaging, it is crucial to consider ISO 11607 principles, which outline the requirements for sterile barrier systems. Additionally, incorporating ICH Q10 validation processes ensures that quality management systems are effectively implemented throughout the production lifecycle.
Utilizing appropriate alu alu materials that meet these regulatory standards will help maintain product integrity and ensure compliance with international regulations.
Global Standards for Alu-Alu Blister Packaging
- WHO Annex 9 emphasizes barrier integrity in packaging for drug protection, highlighting the importance of compliant pharmaceutical packaging practices.
- ICH Q10 integrates Alu‑Alu validation into the pharmaceutical quality system, ensuring adherence to national regulations for alu-alu blisters.
- ISO 11607 guidelines—while designed for sterile packaging—also align with Alu‑Alu cold‑form principles and EU EMA Annex 13 requirements.
Additionally, consider FDA Container-Closure Guidance and USP <661> compatibility when selecting materials for secondary packaging and tertiary packaging in the pharmaceutical industry. Ensure that all processes comply with India CDSCO Schedule M compliance standards to maintain product integrity and safety.
National Regulations
- FDA: Describes Alu‑Alu as a high‑barrier system under Container‑Closure Guidance. It’s compatible with USP <661> and ties into serialization rules under DSCSA. Additionally, FDA regulations highlight the importance of testing requirements for Alu-Alu packaging, including seal strength testing (ASTM F1886/F2096) to ensure integrity.
- EU (EMA): Recognizes Alu‑Alu for investigational medicines per Annex 13 and supports minimal packaging for primary blisters. The regulation also considers factors like water vapor transmission rate (MVTR) to address moisture sensitivity in packaged products.
- India (CDSCO): Cites Alu‑Alu for moisture‑sensitive products; Schedule M mandates cold‑form validation and integrity testing. This includes conducting foil delamination tests and extractable and leachable profiling to ensure product safety and efficacy.
By understanding these national regulations, manufacturers can effectively navigate the complexities of discovering manufacturing steps for Alu-Alu and Alu-PVC blister packs.
Testing Requirements
Critical tests for alu-alu blister packaging include ASTM F1886/F2096 seal strength and assessments of the moisture vapor transmission rate (MVTR), with an ideal target of ≤ 0.1 g/m²/day. These tests are essential for ensuring effective moisture, light, and oxygen protection, which are crucial for shelf life extension benefits in pharmaceutical products. Additionally, foil delamination tests and extractable and leachable profiling are necessary to evaluate the tamper resistance features and the recyclability of aluminum composition.
When conducting these tests, it's also important to consider dynamic vapor sorption (DVS) methods to gain a comprehensive understanding of water activity and its impact on product stability. Furthermore, gaining knowledge on regulatory requirements for pharmaceutical packaging will ensure compliance and enhance the overall effectiveness of the packaging solution.
Advantages & Limitations of Alu-Alu Blister Packaging
Alu-Alu blister packaging offers several advantages in the pharmaceutical industry, including enhanced protection against moisture and oxygen. However, it is essential to consider the limitations of Alu-Alu blisters, such as higher cost considerations in pharmaceutical packaging compared to traditional methods.
One significant advantage is the ability to use silica gel desiccants effectively within these packs, ensuring that sensitive products remain stable over time. Nevertheless, visual inspection challenges may arise due to the opaque nature of the materials used.
Additionally, manufacturers must be aware of production rate differences when opting for Alu-Alu blister solutions, as the complexity of the process can impact overall efficiency. Finally, logistics for thicker packs should be carefully planned to accommodate their increased weight and volume during distribution.
Advantages
- Offers the best protection from moisture, light, and oxygen, making it ideal for moisture or oxidation sensitive products.
- Extends shelf life significantly, especially when dealing with expensive active pharmaceutical ingredients (APIs) that require long shelf-life expectations.
- Highly tamper-resistant, ensuring the integrity of the packaging in high-humidity climate distribution.
- Fully recyclable due to all-aluminum composition.
- Considerations like the moisture vapor transmission rate comparison are crucial when to use alu-alu blister packaging for effective moisture protection in pharmaceutical packaging.
Limitations of Alu-Alu Packaging
- Higher costs associated with cost considerations for alu-alu packaging.
- Visual inspection of tablets isn't possible due to the opaque nature of strip packs.
- Slower production rates compared to traditional blister packs.
- Thicker packs may require adjusted logistics, impacting overall efficiency.
For high-value or critical drugs, the trade-offs are outweighed by the benefits in product stability and regulatory acceptance. This includes factors such as regulatory delay avoidance and downstream cost reduction from stability failures. Additionally, when considering value-based pricing models for blister packs, the impact of relative humidity on drug stability is crucial. Exploring benefits and limitations of aluminium foil in drug packaging also highlights the importance of programs like the Accelerated Stability Assessment Program (ASAP) and tools such as ASAPprime software for stability modeling.
When to Use Alu-Alu Blister Packaging
Alu‑Alu blister packaging should be prioritized when products are moisture or oxidation sensitive, include expensive APIs, or require tamper evidence. This is particularly important for items distributed in high-humidity climates or those with long shelf-life expectations. Examples include antibiotics, oncology agents, hormones, high-cost generics, and dry biologic formulations.
Consider the advantages of Alu-Alu blister packaging, such as its superior barrier properties and ability to protect sensitive ingredients from environmental factors. Additionally, when assessing the sustainability of Alu-Alu packaging, it's essential to explore options like recycling aluminum blisters and using PVC-free laminates to minimize environmental impact.
As the pharmaceutical industry increasingly aligns with pharma ESG commitments, understanding the lifecycle carbon footprint comparison of different packaging types becomes crucial. Moreover, if child-resistant packaging is necessary due to safety concerns, Alu-Alu blisters can be designed to meet these requirements while still offering protection and integrity for the contained products.
However, it's also important to weigh the disadvantages of Alu-Alu blister packaging, such as potential higher costs compared to traditional options or limitations in recycling depending on local facilities.
Cost Considerations
Although Alu‑Alu packaging is more expensive than its Alu-PVC counterparts, it can reduce downstream costs from stability failures or regulatory delays. When evaluating cost considerations in Alu-Alu vs Alu-PVC packs, it's essential to recognize that its recyclable nature supports green initiatives and aligns with future innovations in Alu-Alu packaging.
Additionally, premium blister packs made with next-gen laminates (PE, PLA) with Alu cores become a strategic investment in value-based pricing models. These advanced materials not only enhance product protection but also facilitate smart integration with NFC chips and QR codes for improved consumer engagement.
Moreover, the adoption of nano-laminates for cold-form capability and automated quality control with AI vision systems can further streamline production processes while ensuring safety aspects are met. As you assess different blister pack options, consider the trade-offs between PVC vs PVDC in blister packs to make informed decisions that balance cost and quality effectively.
Sustainability & Recycling
Alu‑Alu is fully recyclable within existing infrastructure, making it an excellent choice for sustainability in the pharmaceutical industry. The shift to PVC-free laminates enhances environmental credentials and aligns with the growing demand for recycling partnerships for closed-loop programs. When aluminum is recycled, its lifecycle carbon footprint is significantly lower than that of mixed-material packaging, such as alu alu vs pvc blister options.
As pharma companies commit to ESG initiatives, Alu‑Alu offers both protective and ecological advantages. Its superior barrier properties make it ideal for moisture-sensitive products, allowing teams to effectively understand advantages of alu-alu blister packaging for moisture-sensitive products. Additionally, incorporating Alu-Alu in your packaging strategy can support stability studies with ICH zones by ensuring that active ingredients remain protected throughout their lifecycle.
For packaging teams looking to optimize their processes, considering the cold-form and seal process validation with Alu-Alu laminates can enhance product integrity while supporting sustainable practices. Furthermore, as you explore formulation development, don't forget the importance of barrier testing in formulation development to assess how different materials interact with moisture and other environmental factors.
By choosing Alu-Alu, you not only prioritize product protection but also contribute to a more sustainable future in pharma packaging.
Future Innovations in Alu-Alu Blister Packaging
Technologies poised to enhance Alu-Alu blister packaging include:
- Smart integration: Embedding NFC chips or QR codes for traceability and patient engagement, aligning with regulatory acceptance of Alu-Alu packs.
- Next-gen laminates: Blends of PE or PLA with aluminum cores target improved recyclability without compromising barrier qualities, supporting sustainability in pharma packaging solutions.
- Nano-laminates: Ultra-thin multi-layer aluminum foils may combine cold-form capability with lower mass, advancing innovation in pharmaceutical packaging materials.
- Automated quality control: AI-powered vision systems can catch seal defects and film consistency anomalies in real time, ensuring the integrity of pharmaceutical packaging barriers.
These developments will maintain Alu-Alu’s premium status and support the evolving demands in pharma, highlighting the alu-alu blister packaging benefits such as superior moisture control compared to plastic bottles vs aluminum blisters for moisture control.
Practical Tips for Pharma Packaging Teams
To ensure successful Alu‑Alu implementation in your pharmaceutical packaging process:
- Conduct barrier testing early in formulation development to assess packaging moisture permeability impact.
- Validate cold-form and seal processes before full-scale run, especially when using cold-form foil-foil blister packaging.
- Include sufficient space for printed information, since foil surfaces are opaque, and consider the functions of different pharmaceutical packaging types.
- Design stability studies aligned with ICH zones using Alu‑Alu packs; ensure these studies account for pharmaceutical stability testing methods.
- Build recycling partnerships to support closed-loop programs while exploring options like desiccant use in packaging to enhance drug stability.
- Train operators in cleanroom protocols and material handling, emphasizing the importance of proper handling techniques in pharmaceutical packaging materials comparison.
Additionally, when considering drug stability, compare alu-alu blister packaging with plastic bottles and desiccants for optimal results.
Conclusion
When product integrity, safety, and compliance cannot be compromised, Alu-Alu blister packaging stands unrivaled among various pharmaceutical blister pack types. While more complex and costly, its extraordinary barrier properties—particularly the barrier properties of Alu-Alu packaging—and regulatory standing justify the investment, especially for critical, moisture-sensitive medications.
As the demand for effective packaging for oral solid medications grows, continued innovation and eco-friendly materials will strengthen Alu‑Alu’s relevance. In an era that demands safety, traceability, and sustainability, understanding Alu-Alu blister packaging composition and structure is essential. This type of packaging not only ensures the protection levels necessary but also incorporates child-resistant pharmaceutical packaging features to enhance safety.
Ultimately, as we explore the landscape of packaging materials in the pharmaceutical industry, comparing Alu-Alu and alu-PVC blister pack protection levels will highlight the unique advantages that aluminium as pharmaceutical packaging material offers. Alu‑Alu remains the cornerstone of premium pharmaceutical packaging.
FAQs
1. What is Alu-Alu blister packaging and what materials are used in its construction?
Alu-Alu blister packaging consists of an aluminum foil base and lid made from a three-layer laminate typically comprising OPA (Oriented Polyamide), Aluminum, and PVC (Polyvinyl Chloride). This cold-formed, opaque, and durable packaging ensures exceptional product protection.
2. What are the key advantages of Alu-Alu blister packaging over thermoformed blisters?
Alu-Alu blister packaging offers superior barrier performance against moisture, oxygen, and light, complete opacity for chemical and microbial resistance, extended shelf-life, tamper-evident security, recyclability, and enhanced product integrity compared to thermoformed blisters which have lower barrier properties.
3. How does Alu-Alu packaging comply with pharmaceutical regulatory standards?
Alu-Alu blister packaging meets stringent regulatory requirements including WHO Annex 9, ICH Q10 guidelines, ISO 11607 standards, FDA's high-barrier system under Container-Closure Guidance, EU Annex 13 for investigational medicines, and India's Schedule M for moisture-sensitive products ensuring safety and compliance in pharmaceutical applications.
4. How does Alu-Alu blister packaging contribute to sustainability and future innovations in pharma packaging?
Alu-Alu packaging is fully recyclable within existing infrastructure with a lower lifecycle carbon footprint than mixed-material alternatives. Innovations include smart integration with NFC chips or QR codes for traceability and patient engagement, development of next-generation PE/PLA laminates with aluminum cores, nano-laminates featuring ultra-thin multi-layer foils, and AI-powered automated quality control systems enhancing both ecological credentials and functional performance.