by Ravindra Warang
7 minutes
Designing Child-Resistant Blister Packs: Safety Standards & Innovations
Explore why child-resistant blister packaging is vital for pharmaceutical safety, regulatory compliance, and patient protection.
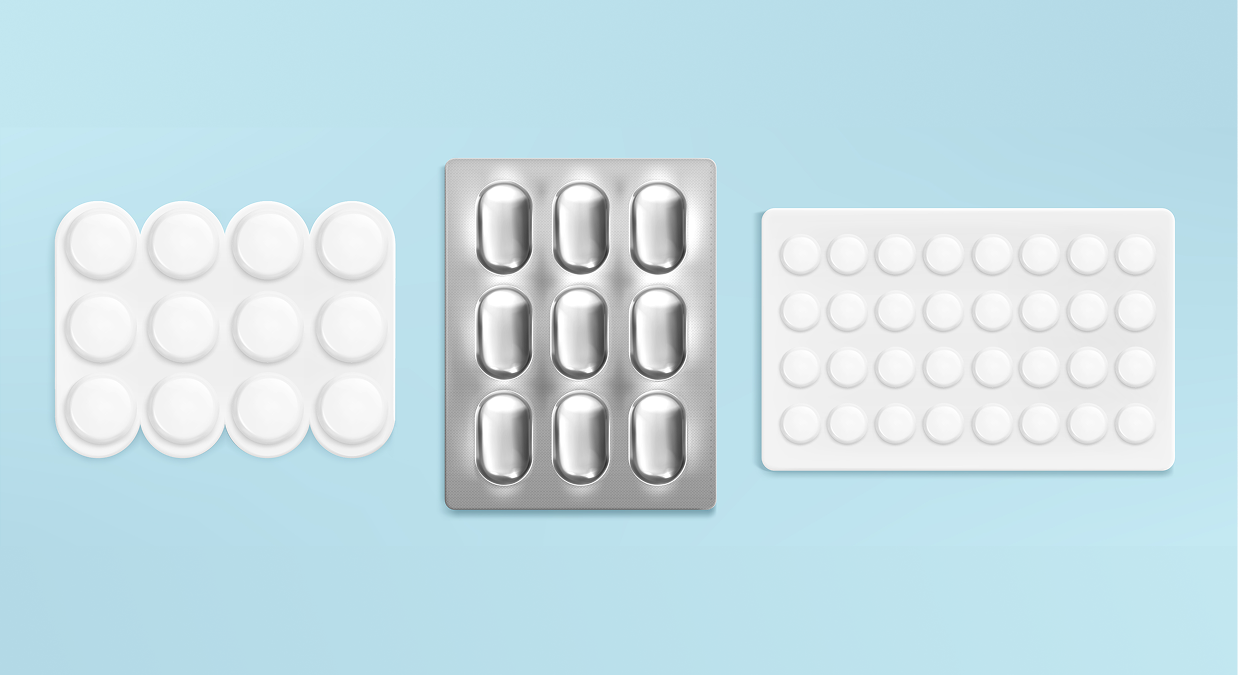
It was a typical afternoon when a hospital in New Delhi reported an alarming case: a 4-year-old had accidentally ingested six tablets of a diabetes medication from a household medicine cabinet. The drugs were stored in a standard blister pack—easy to open, clearly labeled, and completely non-resistant to tiny, curious fingers. This incident highlights the critical importance of pharmaceutical packaging safety and the need for effective child-proofing medications.
This incident, like many others globally, reflects a growing challenge in pharmaceutical packaging: how to ensure ease of access for adults while creating a formidable barrier for children. This is where child-resistant blister packaging enters the picture—not just as packaging, but as life-saving innovations in child-resistant packaging.
As we explore the complexities of pharmaceutical blister packaging standards, it’s crucial to understand how to properly label prescription drugs with child-resistant packaging info and to know testing methods and standards for child-resistant packages. These considerations are vital in preventing accidental ingestions and protecting vulnerable populations.
Why Child-Resistance in Blister Packaging Matters
Accidental pediatric poisoning remains a global concern, making pediatric poisoning prevention a top priority. According to the WHO, more than 50% of accidental poisonings involve children under five years of age, with medicines being a common culprit¹. While blister packs are often assumed to be inherently safe due to dose separation, standard push-through formats can be easily breached by children with developed motor skills, increasing the risk of accidental drug ingestion in children.
Child-resistant packaging importance cannot be overstated. CR designs in pharmaceuticals offer a critical safeguard in homes, hospitals, and pharmacies—particularly for medications like analgesics, antihypertensives, antidiabetics, and psychiatric drugs. These child-resistant safety features are essential for ensuring medication safety for children and complying with packaging standards for nonprescription drugs.
Organizations like the Center for Biologics Evaluation and Research (CBER) provide guidance on including CRP statements in patient information leaflets to enhance awareness about the risks of improper access. As outlined in the Code of Federal Regulations Title 16, effective child-resistant packaging must meet specific criteria to ensure that it effectively prevents young children from accessing potentially harmful substances while remaining accessible to adults.
When considering blister pack safety features, it’s important to compare child-resistant options that also align with environmental sustainability, such as compostable child-resistant zippers. By prioritizing compliance for blister packs that integrate these elements, manufacturers can better protect vulnerable populations while addressing ecological concerns.
Global Regulatory Standards: The Backbone of CR Design
Child-resistant packaging (CRP) is not optional in many geographies—it is mandated by law under global regulatory standards for CR packaging.
United States
Under the Poison Prevention Packaging Act (PPPA) and CPSC requirements 16 CFR §1700, the Consumer Product Safety Commission (CPSC) requires that certain prescription and OTC medications be packaged in child-resistant formats². Additionally, ASTM D3475 design criteria outlines design criteria for unit-dose formats3.
European Union
The European Medicines Agency (EMA) mandates safety under Directive 2001/83/EC. EU CR packaging regulations stipulate that ISO 8317 performance testing is essential for reclosable CR packaging4, while EN 14375 covers non-reclosable formats like blister packs5.
India
Though not yet mandatory for all products, CDSCO guidelines in India encourage CR packaging for pediatric formulations and high-risk medications6.
To pass the regulatory muster, CR packaging compliance testing must ensure that such packaging prevents access for at least 85% of children during testing, while ensuring at least 90% of adults can use the packaging successfully. This includes adhering to requirements for carton and container labels with CRP info, as well as understanding how to include CRP statements on labels effectively.
When considering materials, options like Fresh-Lock child-resistant zippers can enhance safety in various applications, including aerosol cans. It's crucial to recognize the benefits of child-proof features that align with GMP for blister packaging standards.
Key Design Principles for Child-Resistant Blister Packs
Designing child-resistant blister packaging is a delicate balance between protection and accessibility. Some key design principles for child-resistant blister packs include:
Two-Step Access Mechanisms:
Requires two distinct, sequential actions—such as press + slide or peel + push—too complex for small children but manageable for adults. This two-step access is crucial for compliance with the Poison Prevention Packaging Act related to drug containers.
Peel-Push Blisters:
Uses a laminated foil or fold system, forcing the user to uncover the medication before pushing it out. These peel-push blisters are essential in Biologics License Applications (BLA) and the Over-the-Counter (OTC) Drug Review process.
Hidden Cavity Designs:
Pills may be concealed behind additional layers or flaps, requiring alignment, lifting, or peeling to access. This principle helps maintain safety by implementing disrupted recognition patterns in CR packaging.
Increased Opening Force Requirements:
Push-through resistance is elevated beyond what an average child can exert (50–60 Newtons), ensuring that only adults can easily access the contents while adhering to child-resistant blister pack regulations.
Disrupted Recognition Patterns:
Non-uniform layouts and varying push points reduce the ability for children to repeat successful attempts, making it harder for them to navigate the packaging effectively. This is vital when considering child-deterrent claims in labeling.
When developing child-resistant blister packs, it's important to include clear instructions on how to open child resistant closures within the prescribing information section, HOW SUPPLIED/STORAGE AND HANDLING.
Notable Examples of CR Blister Innovations
Ecobliss Locked4Kids system
A patented CR blister system combining cartons and blisters with hidden access mechanisms, popular for controlled substances and antipsychotics⁷. This innovative design prioritizes child safety in packaging design while ensuring compliance with drug product labeling guidance.
Bilcare CR Blisters technology
Incorporate dual-layer foil and delayed push-release technology to increase access complexity⁸. These features are essential for distinguishing between prescription and OTC drug packaging regulations for CRP, ensuring that nonprescription drug products remain secure yet accessible.
Klockner Pentaplast CRxPack features
Uses multi-layer PET film with a rigid cavity and peelable lidding for dual protection⁹. This design not only protects the integrity of the medication but also meets tamper-evident packaging compliance standards.
Aptar CSP Technologies designs
Their CR innovations integrate active barrier polymers with two-step access and built-in moisture protection¹⁰. These designs are crucial for effective patient labeling for child-resistant packaging, especially in markets with strict regulations on prescription drug products.
Each design undergoes child panel testing ISO 8317 / ASTM D3475 resistance validation to assess its resistance level while ensuring adult usability. Additionally, manufacturers are encouraged to find sustainable options for child-resistant packaging materials that do not compromise safety or efficacy.
Material & Machinery Considerations in CR Blister Production
Producing CR blister packs requires careful changes in both material selection and machinery considerations in CR packaging:
Materials for CR blister production
Films: PET/PE/foil laminates offering higher stiffness and puncture resistance. These materials are essential for ensuring the integrity of flexible packaging child resistant designs.
Foils: Specialized CR-grade aluminum foils with strong seal coatings to maintain product safety and compliance with labeling requirements for CRP.
Machinery Tooling: Custom molds for CR designs to create locking folds, dual blisters, or hidden cavities that meet the specific needs of Container Closure Systems.
Lines: Standard production lines may need servo upgrades in production lines or inline visual inspection for CR cavities to ensure proper cavity alignment and adherence to CPSC special packaging standards for children safety.
While retrofitting is often possible, line speeds may drop by 15–25% depending on design complexity. This is an important consideration when developing packaging for prescription medications like Kirkland Signature products.
For further insights, see case studies on successful child-resistant flexible packaging implementations.
Documentation, Labeling & Regulatory Testing for CR Packaging
To obtain market approval, child-resistant (CR) packaging must pass:
Child Panel Tests
Conducted with children aged 42–51 months using standard testing panels of 50–200 participants. This child panel tests methodology ensures that the packaging is truly resistant to accidental opening by young children.
Senior Usability Tests
Typically done with 50–70-year-olds to assess real-world accessibility and ensure that senior individuals can use the packaging safely. These senior usability tests are crucial for understanding the diverse needs of all users.
Labeling
Must be clear, multilingual, and supplemented with diagrams to reduce misuse risk. Adhering to multilingual labeling requirements is essential for effective communication across different language speakers.
Submission Requirements
Include test data, packaging drawings, Standard Operating Procedures (SOPs), and validation protocols. These packaging submission protocols ensure that all necessary information is provided for regulatory testing for CR packaging.
This ensures compliance not only with regulators but also with public health expectations. By following Special Packaging Standards set by the Food and Drug Administration (FDA) and incorporating elements like Drug Facts Labeling (DFL) and specific subheadings such as 'Other Information,' manufacturers can guarantee over-the-counter drug packaging safety and effective child-resistant blister packaging.
For those looking to get guidance on designing and manufacturing effective child-resistant closures, understanding these regulatory requirements is paramount.
Trends Shaping the Future of CR Blister Packaging
Smart CR Packs: These innovative trends in CR blister packaging feature smart CR packs with NFC tags that use smartphone apps to guide correct opening sequences.
Dual-Access Formats: Dual-access formats in packaging are becoming popular, offering an outer child-resistant (CR) layer and inner standard blisters to balance safety and usability. This approach ensures compliance with child resistant packaging standards while meeting consumer needs.
Senior-Friendly Designs: As the population ages, senior-friendly CR designs are essential. These packages integrate tactile markers, audible clicks, and large-font instructions to aid the elderly, ensuring accessibility and safety in accordance with U.S. Consumer Product Safety Commission (CPSC) guidelines.
Sustainable CR Packs: The demand for sustainable child-resistant packs is rising. Look for bio-based films in CR packaging and PET-based laminates that pass CRP testing procedures while being recyclable and compostable CR solutions. These materials align with FDA blister packaging guidelines and support environmentally friendly practices.
Quick Comparison Table of Standard vs Child-Resistant Blister Packs
Conclusion: Designing with Care
The New Delhi incident isn't an anomaly—it reflects a systemic gap in how pharmaceutical products are protected in the real world. The importance of child-resistant blister packs goes beyond mere compliance; they are a moral obligation for drug safety and a clinical necessity. Child-resistant packaging (CRP) is essential in ensuring that the most vulnerable populations are protected while still meeting pharmaceutical packaging compliance standards.
With rising awareness, updated regulations like the evolution of child-resistant packaging standards, and better design thinking focused on designing for child safety in pharmaceuticals, the pharma industry has the opportunity—and obligation—to create packaging that safeguards children without inconveniencing intended users. This shift is crucial as companies navigate New Drug Applications (NDA) and Abbreviated New Drug Applications (ANDA) processes while adhering to guidelines that prevent misbranding under FD&C Act section 502(p).
It’s time we move from “child-proof” to “child-considered,” recognizing the critical role that sustainability in child resistant packaging plays in protecting both people and the environment. As we discover innovations in flexible child-resistant packaging, let’s ensure that learning regulatory requirements for child-resistant drug packaging statements becomes integral to the design process. By aligning with CDSCO packaging rules and prioritizing the safety of all users, we can create a healthier future for everyone.