by Ravindra Warang
10 minutes
Trends Transforming Injectable Drug Manufacturing in 2025
Explore how AI, robotics, and modular tech are revolutionizing injectable drug manufacturing in 2025 and beyond.
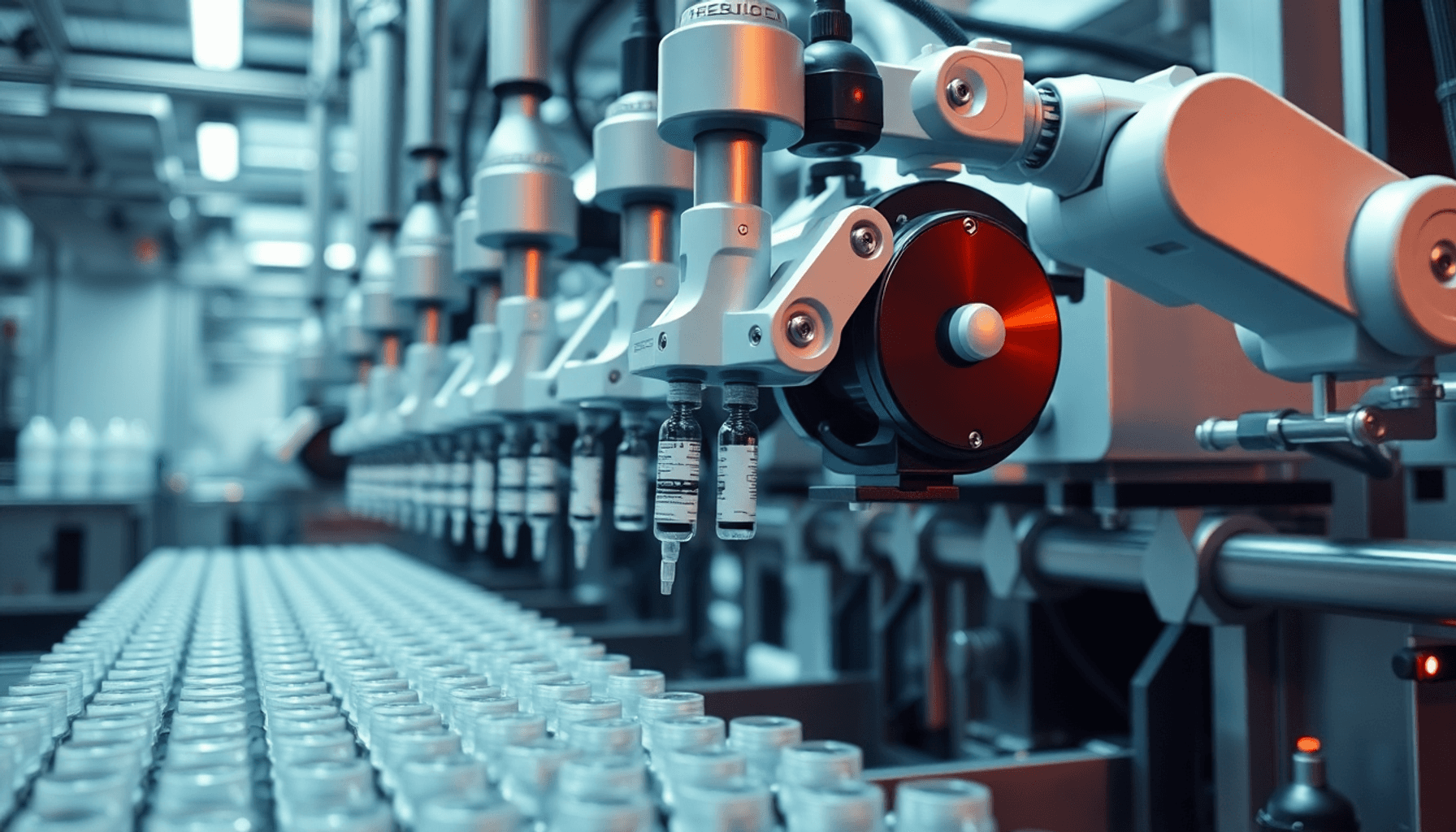
In 2010, a top-five pharmaceutical company needed nearly two years to scale up manufacturing for a blockbuster injectable biologic. By 2025, the same feat can be achieved in under six months—thanks to modular cleanrooms, digital twins, and AI-enhanced fill-finish lines.
Injectable drug manufacturing is undergoing a revolution. Once considered rigid, slow, and capital-intensive, it is now at the forefront of pharmaceutical innovation. The need for personalized therapies, advanced biologics, and robust pandemic response infrastructure has pushed manufacturers to rethink every step—from upstream processing to patient-ready syringes.
This article explores the most transformative injectable pharma trends reshaping manufacturing. From AI-powered quality control to single-use systems, we’ll examine the tools, technologies, and strategies driving a more flexible, safe, and efficient future. Key considerations include regulatory strategy and risk mitigation in pharma partnerships as the industry adapts to market uncertainties impacting pharmaceutical funding and operations.
1. Rise of Single-Use Technology (SUT) in Fill-Finish Operations
Traditionally, sterile fill-finish operations relied on fixed stainless-steel infrastructure. However, by 2025, the industry is expected to reach a tipping point where single-use technology (SUT) becomes standard across mid- and small-batch injectable lines, particularly in the production of biologics and orphan drugs.
Why It Matters:
- Reduces cleaning validation and changeover times
- Minimizes cross-contamination risk
- Ideal for clinical trial production and innovative therapies
According to a BioPlan survey, over 65% of biomanufacturers now use single-use technology in some aspect of injectable production. Vendors offer gamma-sterilized products that include fully disposable product contact surfaces—syringe tubing, connectors, bags—delivered gamma-sterilized and ready for aseptic setup.
As the demand for prefilled syringes increases, especially for applications like insulin injections, companies are also considering sustainability initiatives in pharmaceutical packaging and manufacturing. Moreover, with the evolving landscape of serialization laws in pharmaceutical packaging, effective third-party resources management in pharma has become crucial.
For those looking to understand broader trends, the Asia Pacific 2025 forecast indicates significant growth in the adoption of AI fill‑finish technologies within the sector.
2. Modular & Flexible Facilities for Agile Manufacturing
In an age of rapid tech transfers and decentralized trials, pharma companies are increasingly adopting modular cleanroom facilities that can be scaled or reconfigured on demand. These facilities are essential for agile manufacturing processes, allowing for quick adjustments in response to changing market demands.
Key Features:
- Plug-and-play isolators and filling lines designed for efficiency
- Rapid HVAC commissioning via prefabricated zones to ensure optimal air quality
- Mobile units for pandemic response or regional production, addressing shifting needs in the industry
Notably, CDMOs like Lonza and Catalent are investing in multi-client modular platforms, which streamline operations and reduce time-to-launch for niche biologics and advanced therapies. This approach not only helps in meeting the complexities of drug-device combination products but also addresses key CDMO product development challenges.
As the industry evolves, considerations such as carbon footprint reduction in pharma production and the requirements of biologic medication cold chain requirements are becoming increasingly important. Additionally, understanding new technologies like connected health and the expansion of the pharmaceutical packaging secondary market are vital for staying competitive.
Companies like Tjoapack LLC are at the forefront of these changes, offering innovative solutions that integrate single‑use pharma practices while ensuring compliance with US FDA regulations.
3. AI-Driven Quality Assurance and Visual Inspection in Injectable Pharma Trends 2025
Visual inspection has long been one of the bottlenecks in injectable manufacturing. In 2025, AI-based vision systems are replacing human inspectors, significantly improving accuracy and throughput. This shift is a key aspect of emerging injectable pharma trends, as the industry adapts to new technologies and regulatory requirements.
Benefits:
- Detects particles as small as 50 microns, enhancing particle detection rates
- Learns and self-corrects across production cycles
- Integrates with MES and QMS platforms for real-time deviation alerts
Fact: According to ISPE, AI-enhanced visual inspection has improved particle detection rates by up to 90% compared to manual inspection.
The FDA has signaled support for these innovations through its commitment to FDA support for AI innovations, as long as models are validated per GAMP5 AI guidelines. As the pharma industry responds to patent expirations and shifts towards advanced solutions like autoinjectors and dual chamber syringes, considerations for regulatory and quality management system considerations become paramount.
4. Smart Autoinjectors and Drug-Device Combinations
The growing emphasis on self-administration has turned injectables into consumer-centric products. In 2025, smart autoinjectors are leading this shift, particularly with advancements in Bluetooth connectivity and NFC technology.
Key Features:
- Connectivity via Bluetooth or NFC
- Real-time adherence tracking
- Digital dose reminders
- Dose authentication to reduce counterfeiting
Companies are co-developing drug-device combinations under the FDA Combination Product Rule (21 CFR 3.2(e)). Human factors studies are now essential for approval, particularly for chronic therapies like insulin, GLP-1 agonists, and anti-migraine injectables. This is especially relevant given the increasing demand for emerging therapies for rare diseases and oncology.
As the aging population impacts pharma market growth, the need for innovative solutions like large-volume systems and plastic syringes becomes crucial. Additionally, addressing supply chain issues in the injectable pharma industry is vital for ensuring the availability of lyophilised drugs.
For those looking to stay ahead, it's important to learn about innovations in syringe and injectable drug packaging, including the use of digital twins in manufacturing.
5. mRNA Technology Injectables and Cell Therapy Injectables: From Research to Reality
In the post-pandemic era, mRNA technology and autologous cell therapies are making their way into injectable pipelines. However, their manufacturing demands differ significantly from traditional biologics. As the growth of GLP-1 therapies beyond diabetes continues, the demand for innovative solutions in the injectable pharma sector is rising.
Emerging Needs:
- Cryogenic fill-finish for mRNA technology injectables and cell therapy injectables
- Cold chain storage (-70°C) to ensure product integrity
- Sterility under low-exposure isolators during the production of CAR-T therapies and mRNA vaccines
- Closed system manufacturing to enhance safety and efficiency
Facilities are integrating biosafety level design, RNA lyophilization systems, and real-time analytics to support next-gen injectable modalities. Additionally, as chronic disease prevalence increases, understanding market drivers and restraints for injectable drugs becomes crucial.
The Parenteral Drug Association (PDA) emphasizes the importance of programme management and addressing cybersecurity risks in pharma manufacturing as these technologies advance. Companies like Viatris and Corning Incorporated are at the forefront of implementing liquid-liquid technologies and lyophilization technology trends that redefine standards in the industry.
Explore emerging therapeutic areas such as GLP-1 agonists while considering the impact of radio-frequency identification (RFID) systems on supply chain efficiency in this evolving landscape.
6. Integration of Digital Twins in Injectable Manufacturing
Digital twins in injectable manufacturing—virtual replicas of physical systems—are changing the game for process design simulation, troubleshooting, and scale-up in injectables.
Applications:
- Simulating fill-finish parameters and line throughput prediction
- Predictive maintenance for isolators and filling needles
- Virtual training modules for operators
Fact: According to the McKinsey report on digital twins, companies using digital twins in pharma report 20–30% faster tech transfers and significant reductions in OOS investigations.
As the injectable pharma trends 2025 evolve, the integration of digital twins will be crucial in addressing master services agreement negotiation challenges in pharma collaborations and ensuring compliance with regulatory impacts on pharmaceutical packaging.
7. Advanced Lyophilization: Smarter, Smaller, Faster
The freeze-drying of injectables, especially biologics, has seen significant technological upgrades with advanced lyophilization techniques.
Innovations in 2025:
- Controlled nucleation for uniform cake structure
- AI-based endpoint determination
- Continuous lyophilization (vs. traditional batch mode)
Smaller, multi-product lyophilizers enable high-mix, low-volume runs with better agility and energy consumption reduction—aligning with sustainability goals in lyophilization. These advancements are crucial for meeting the needs of diverse markets, including oncology and rare disease indications, while also addressing the impact of US FDA changes on drug approvals and inspections.
As the demand for home healthcare solutions rises in the Asia-Pacific region, understanding these trends is essential.
8. Sustainability in Injectable Packaging and Processes
Environmental responsibility is now a key metric discussed in boardrooms. Injectable manufacturing in 2025 will focus on eco-friendly processes in the pharmaceutical industry and packaging solutions with minimal environmental impact. As the industry changes, sustainability in injectable packaging becomes crucial, especially with the increasing use of cell and gene therapies and treatments for cancer.
Sustainability Initiatives:
- Using recyclable polymer cartridges (COP, COC)
- Reducing overfill and waste from glass containers
- Implementing energy-efficient operations in cleanrooms
- Recovering solvents and optimizing Water for Injection (WFI) loops
Manufacturers are using Life Cycle Assessments (LCA) to measure and reduce carbon dioxide emissions for each injectable unit. This method not only helps in understanding the impact on the environment but also tackles funding issues faced by biotech startups and pharmaceutical companies in 2025.
As the healthcare sector shifts towards home-based care and self-administration trends in 2025, it becomes important for industry professionals to know the differences between PDA Miniverse and Universe conferences. Moreover, understanding how supply chain dynamics in North America influence these developments will be crucial.
Robotics in aseptic processing is also becoming more popular as companies aim for higher efficiency while upholding sustainability standards.
9. Collaborative Robotics (Cobots) in Aseptic Suites
To reduce human intervention and GMP (Good Manufacturing Practice) deviations, companies are deploying collaborative robotics (cobots) in aseptic suites within Grade A/B environments. This integration is essential for maintaining high standards of quality and safety, especially in light of emerging injectable drug delivery trends 2025.
Use Cases:
- Vial loading automation: Loading vials into nests
- Capping and stoppering tasks: Ensuring proper sealing and integrity
- In-process sample collection: Streamlining testing procedures
These mobile cobots are lightweight, programmable for high-mix lines—improving consistency and reducing fatigue-related errors. As the pharmaceutical industry navigates market uncertainties and layoffs in pharmaceutical industry 2025, the adoption of such technologies not only enhances efficiency but also supports risk mitigation strategies when working with third-party pharma partners.
With the rise of chronic diseases and the need for innovative solutions like NARCAN nasal spray and pre-filled syringe packaging innovations, collaborative robots are becoming indispensable in large-volume systems dedicated to on-demand injectable manufacturing.
10. Personalized Injectables & On-Demand Manufacturing
With the rise of precision medicine, there’s a growing demand for personalized injectables—especially for cancer therapies, rare disease treatments, and gene therapies.
Trends in 2025:
- 3D-printed autoinjector components for patient-specific regimens
- Closed-loop formulation systems in hospital pharmacies
- Use of patient-derived data to calibrate dose, route, and formulation
Regulators like EMA and FDA are exploring adaptive regulatory pathways for these fast-evolving modalities. As advancements in autoinjectors and emergency drug delivery devices continue, it's crucial to discover regulatory challenges affecting injectable pharma product approvals. Additionally, understanding how program management can affect injectable pharma projects is essential, especially with the increasing use of self-administration devices for injections among patients with diabetes.
Furthermore, discussions at conferences like the PDA Universe conference vs Miniverse conference will likely address trends such as plastic vs glass syringes advantages and trends, as well as assessing materials used for syringes and their benefits.
Conclusion: Manufacturing at the Speed of Innovation
Imagine a world where a rare disease treatment, such as cancer therapy, is manufactured on-demand in a modular cleanroom using single-use line technology. This process is enhanced by AI inspection systems and ensures that the final product is shipped overnight in a smart injector to a patient's home.
That world is here—and it’s only accelerating.
The trends transforming injectable manufacturing innovation in 2025 aren’t just upgrades; they are paradigm shifts in pharma manufacturing—toward speed and flexibility in production, sustainability in injectable pharma, and patient-centric injectable solutions. Companies that embrace these changes aren’t just staying competitive—they’re defining the future of pharmaceutical care.
As the Biden administration implements stringent regulatory mandates and sterility standards, the hospital demand for injectable drug packaging continues to rise, as evidenced by 2023 data. Additionally, understanding the impact of chronic diseases on injectable drug demand is crucial for CDMOs as they adapt their roles and evolving capabilities in drug delivery device development.
Moreover, the connected health impact on clinical trials and compliance monitoring cannot be overlooked. Innovations in injectable drug delivery devices are reshaping how treatments are administered and monitored, ensuring that patient safety and efficacy remain at the forefront.
In this dynamic landscape, staying ahead of injectable pharma trends 2025 will require a keen awareness of emerging technologies and market shifts.
FAQs (Frequently Asked Questions)
How are modular cleanrooms revolutionizing injectable drug manufacturing?
Modular cleanrooms offer scalable and reconfigurable facilities on demand, significantly reducing time-to-launch for niche biologics and advanced therapies. Their flexibility supports faster production cycles and adaptability to evolving manufacturing needs.
What role does AI play in enhancing quality control in injectable manufacturing?
AI-powered quality control integrates AI-driven visual inspection systems that replace human inspectors, detecting particles as small as 50 microns and improving particle detection rates by up to 90%, thereby enhancing product safety and consistency.
Why is single-use technology becoming prevalent in injectable drug manufacturing?
Single-use technology minimizes cleaning, validation, and changeover times while reducing the risk of cross-contamination. Currently, over 65% of biomanufacturers utilize single-use systems to streamline aseptic processes and improve operational efficiency.
What advancements are shaping smart autoinjectors in 2025?
Smart autoinjectors now enable connectivity features such as adherence tracking, dose reminders, and dose authentication. Developed under FDA's Combination Product Rule (21 CFR 3.2(e)), these devices enhance patient-centricity and treatment compliance.
How are digital twins transforming fill-finish operations in injectable manufacturing?
Digital twins create virtual replicas of physical systems to simulate fill-finish parameters, optimize line throughput, enable predictive maintenance, and provide virtual training modules. This integration results in 20-30% faster technology transfers and improved operational efficiency.
What sustainability initiatives are being adopted in injectable drug manufacturing by 2025?
Injectable manufacturing prioritizes green processes and low-impact packaging by adopting Life Cycle Assessments (LCA) to reduce CO₂ emissions per unit. These efforts support environmental responsibility while maintaining high-quality production standards.