by Enoch Daniel
6 minutes
Implementing Lean Manufacturing in Pharmaceuticals: Reducing Waste and Enhancing Efficiency
Lean manufacturing in pharma enhances efficiency, reduces waste, improves quality, and ensures compliance through streamlined processes.
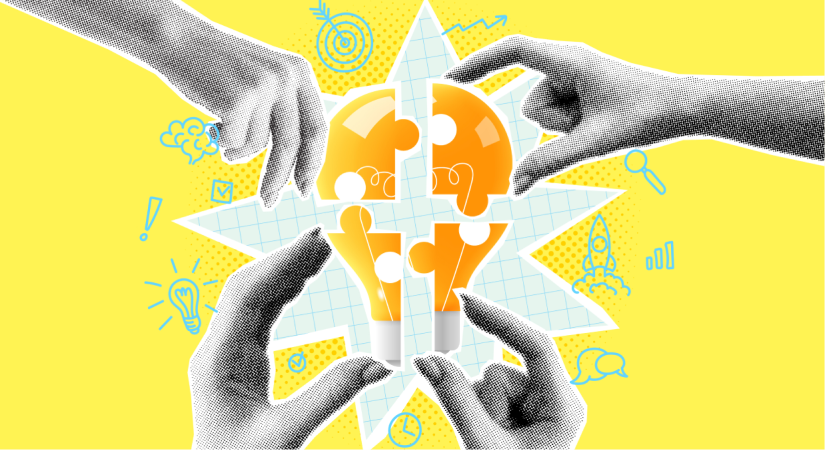
Image Source: freepik.com
In the fast-paced and stringently regulated pharmaceutical space, efficiency, quality, and cost-effectiveness are the key requirements for any pharmaceutical company. Pharma companies need to develop and provide life-saving medicines while adhering to regulatory standards and maintaining high product quality. In this challenging environment, lean manufacturing is emerging as a new approach.
While lean manufacturing principles were first developed for the automotive sector, they are equally applicable to pharmaceuticals. Lean manufacturing in pharmaceuticals can streamline processes, reduce waste, and enhance value—all of which will lead to cost savings. There are several benefits of implementing lean manufacturing practices, but before delving into those, it’s necessary to understand lean manufacturing principles.
The Principles of Lean Manufacturing in Pharmaceuticals
There are five core lean manufacturing principles for pharmaceuticals, which have been adopted from the automotive industry. These core principles are as follows:
Value identification
Value identification involves understanding what end users—patients, healthcare providers (HCPs), and regulators—value the most. Hence, pharmaceutical companies need to identify what their end users value in their products and adjust their manufacturing goals accordingly to build brand trust and improve patient outcomes. For example, HCPs may value accurate dosing and reliable supply, so manufacturing must ensure consistent product quality.
Value stream mapping
Value stream mapping analyzes the flow of materials, processes, and information during manufacturing processes. Using value stream mapping, pharma companies can identify bottlenecks, redundancies, and non-value-adding steps in production cycles. Consequently, these issues should be resolved to improve production efficiency and quality.
Continuous flow
This lean manufacturing principle aims to maintain smooth and uninterrupted production processes while minimizing equipment downtime and aligning production with demand. Unlike batch processing, continuous flow ensures there is little to no wait time, and each production step transitions smoothly. It optimizes equipment use and aligns production with market needs.
Pull system
According to this principle, pharma companies should only produce the products according to the actual demand. By cutting down on bulk manufacturing and only manufacturing units that are actually required in the market right now, companies can avoid overstocking. This principle doesn’t only apply to manufactured goods but also to raw materials. By following this principle, companies can avoid overstocking raw materials, which will also minimize waste.
Perfection
Also known as Kaizen, this principle was developed by Kiichiro Toyoda, the founder of Toyota Motor Corporation. According to this principle, pharma companies must always maintain a culture of improvement. Current processes, systems, and quality must be regularly reviewed and updated. By involving cross-functional teams and training employees to identify improvement opportunities, companies can improve their already robust processes, ensuring their systems prioritize the values most important to end users.
By implementing these five core principles of lean manufacturing, pharma companies can realize multi-fold benefits.
The Benefits of Lean Manufacturing in Pharmaceuticals
High efficiency
Lean manufacturing promotes the streamlining of manufacturing processes by removing, updating, or replacing non-value-adding steps. This reduces the production time and optimizes resource utilization (labor, materials, and equipment), which increases the overall efficiency of the manufacturing plant.
Reduced waste
By manufacturing only what is needed, pharma companies avoid overstocking manufactured goods and raw materials, reducing the risk of wastage. Lean manufacturing principles also encourage efficient resource utilization, which leads to waste minimization, allowing companies to reach their sustainability goals.
Reduced costs
Lean manufacturing principles—especially pull system, continuous flow, and perfection—reduce overproduction, ensure manufacturing is consistent, and make sure processes are optimized, all of which reduce waste and ensure production costs decrease.
Improved product quality
Lean manufacturing ensures the desired product quality is obtained at every stage of manufacturing. Hence, it reduces variability and possible defects in the product, which leads to fewer recalls and compliance violations. By building and maintaining this consistency, pharma companies can meet end users’ expectations.
Increased adaptability
Streamlined processes allow pharma companies to quickly adjust their manufacturing processes to unexpected changes in demand or regulatory requirements. Furthermore, companies can also quickly make changes in production when faced with supply chain disruptions without compromising on product quality.
As shown by these advantages, the implementation of lean manufacturing in pharmaceuticals affords a pharmaceutical company a competitive advantage. They may be able to adapt more quickly to market and regulatory changes than their competitors all the while offering high product quality, reducing waste, and meeting the end users’ criteria. Several major pharma companies practice lean manufacturing techniques in their daily operations.
The implementation of lean manufacturing may seem like a daunting huge task to many, but, in reality, it is not very complex. Lean manufacturing in pharmaceuticals is unique to every company, as there is no set formula for you to follow. So, how exactly does one go about implementing lean manufacturing? Here are some tips to help you!
Lean Manufacturing Tips
Understand principles thoroughly
To successfully implement lean management in pharma production processes, it is necessary to thoroughly understand what each principle means in the context of the manufacturing process. Leaders and teams should thoroughly understand lean management principles and their benefits. Focus should be given to explaining that implementing these processes will improve customer value, reduce waste, and improve efficiency.
Secure leadership support
For successful implementation, leadership should fully support lean initiatives. Hence, it is necessary to clearly communicate how lean initiatives align with the strategic goals of the company, for example, cost reduction, regulatory compliance, and competitiveness. Efforts should be made to ensure lean initiatives do more than just reduce waste—they should bring actual value to the existing system to ensure the adoption is worth the effort.
Start small
Implementing lean initiatives in all areas of production will lead to only one thing: confusion. Instead, target one specific (and preferably, small) area of production like packaging. In this area, test lean initiatives and techniques. Define success indicators before implementing initiatives. Then, after successful implementation, assess whether there were any bottlenecks before implementing the initiative on a large scale. This method will demonstrate commitment to and feasibility of lean initiatives.
Conclusion
Lean management techniques are aimed at reducing waste and enhancing efficiency, both of which are very important in today’s world where pharma companies have to demonstrate the sustainability of their production processes. Many pharma companies have implemented lean manufacturing techniques to increase the overall output of the company as lean principles not only focus on product quality and waste generation but also the standardization and elimination of non-value-adding procedures.
Realistically, lean principles are not a one-time undertaking. They’re a path to creating a culture within a company: a culture that focuses on improvement, standardization, quality, and value. As the pharmaceutical industry and its existing practices come under increased public scrutiny, implementing lean initiatives is another way of gaining trust and creating a reputation.
FAQs
1. What is lean manufacturing in pharmaceuticals?
Lean manufacturing is a systematic approach to reducing waste and enhancing efficiency. By eliminating non-value-adding processes, it aims to deliver high-quality products while reducing costs.
2. What are the advantages of implementing lean manufacturing?
Implementing lean manufacturing in pharmaceuticals has several advantages, including lower costs, better product quality, high regulatory compliance, and faster response to market demands.
3. How can lean manufacturing improve compliance?
Lean manufacturing improves compliance by reducing human errors via standardized processes, improving documentation, and streamlining validation activities.