by Ravindra Warang
10 minutes
Roller Compaction: Dry Granulation Methods
Discover roller compaction in pharma: moisture-free, efficient dry granulation for stable and scalable tablet manufacturing.
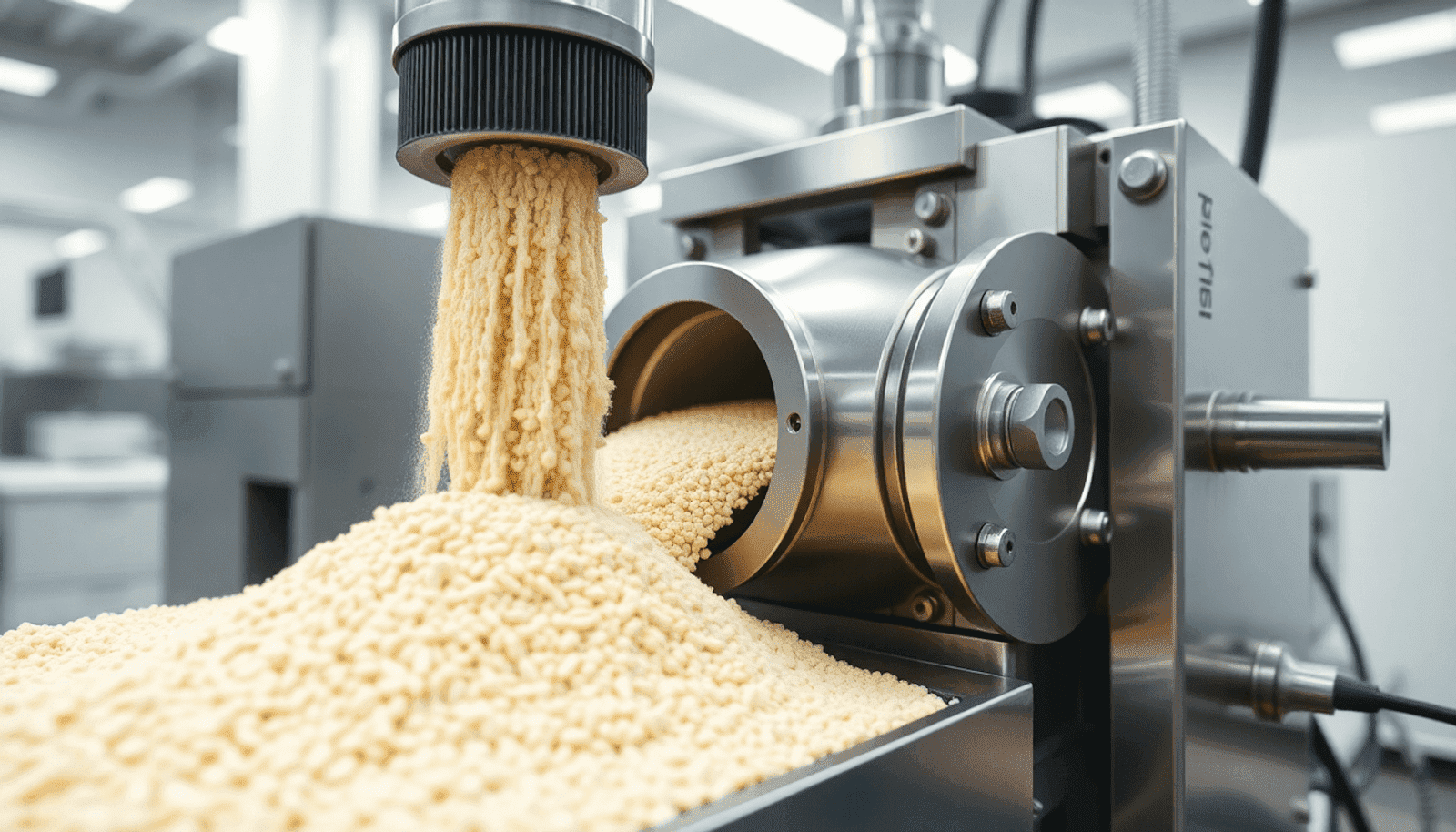
In a high-containment pharmaceutical suite, technicians prepare a formulation for a moisture-sensitive API. Water is out of the question, and heat isn’t safe either. The solution? Pressure—delivered precisely by roller compaction.
Dry granulation, led by roller compaction in pharmaceuticals, has become the go-to technology for pharmaceutical formulations where heat, solvents, or liquid binders could destabilize the active pharmaceutical ingredient (API). This method is especially critical when working with sensitive compounds that require careful handling to maintain their integrity.
In this guide, we’ll explore how roller compaction works, its advantages—such as improved uniformity and reduced processing time—when to use it in the context of oral solid dosage manufacturing, and how it’s reshaping the future of pharmaceutical manufacturing.
We’ll also discuss key considerations like the impact of roller compaction on moisture-sensitive compounds and the importance of stability and dissolution testing of roller compacted formulations. Additionally, we’ll compare slugging vs roller compaction as techniques in dry granulation and examine the role of process analytical technology (PAT) in optimizing these processes.
Whether you’re considering using spray-dried lactose monohydrate as a filler-binder or assessing the efficacy of high performance liquid chromatography (HPLC) in quality control, understanding these dynamics is essential for successful formulation development.
Join us as we delve into the intricacies of roller compaction and its pivotal role in modern pharmaceutical manufacturing.
What is Roller Compaction in Pharma?
Roller compaction is an important dry granulation method used in making pharmaceuticals. It works by using two rollers that turn in opposite directions to compress powder mixtures into solid strips. These strips are then crushed into evenly sized granules, guaranteeing consistent quality and performance.
Why Choose Roller Compaction?
Roller compaction offers distinct advantages over wet granulation, particularly when dealing with sensitive drugs:
- No moisture exposure: Unlike wet granulation, which uses liquid binders, roller compaction eliminates the risk of moisture damage to heat-sensitive ingredients.
- Gentle processing: The absence of heat during the process ensures that delicate compounds retain their stability and efficacy.
This makes roller compaction an ideal choice for formulating moisture- and heat-sensitive medications.
Key Principles:
Here's a breakdown of the key principles behind roller compaction:
- Powder is compacted between two rollers under high pressure
- Ribbons are formed as a result of the compaction process
- Ribbons are milled into granules
- Granules are blended and sent for compression or encapsulation using a tablet press
These principles play a crucial role in achieving optimal results during pharmaceutical manufacturing.
Advantages of Dry Granulation Process:
The dry granulation process, including roller compaction, offers several benefits:
- Reduced moisture exposure
- Improved flow properties of granules
- Enhanced bioavailability of active ingredients
- Greater flexibility in formulation design
By leveraging these advantages, pharmaceutical companies can enhance their manufacturing efficiency while ensuring product integrity.
Understanding the roller compaction process is essential for achieving pharmaceutical manufacturing efficiency improvements with dry granulation. By utilizing this technique, companies like PCI Pharma Services can streamline continuous processing while maintaining product integrity.
Advantages of Roller Compaction and Why It Matters
1. No Water or Heat Needed
→ Ideal for processing moisture- or heat-sensitive Active Pharmaceutical Ingredients (APIs). Eliminates the need for drying steps.
2. Simplified Process
→ The absence of drying steps significantly reduces production time, streamlining the overall granulation workflow.
3. Consistent Granule Density
→ Delivers robust tablet hardness and uniformity. This consistency is critical for ensuring proper tensile strength in tablets.
4. Cost-Efficient
→ Requires lower energy consumption and has a smaller equipment footprint, which supports operational cost savings and contributes to sustainability in pharmaceutical manufacturing.
5. Scalability
→ Roller compaction is easily scalable—from pilot to commercial production—accommodating a wide range of batch sizes.
By considering the influence of excipient composition on roller compaction, manufacturers can effectively tailor formulations that meet specific quality standards. Additionally, learning about the impact of formulation variables on roller compacted product quality is essential for success in this dynamic field.
Using fixed rolls roller compactors allows for precise control over the granulation process, making it an excellent alternative to traditional wet granulation methods.
Core Components of a Roller Compaction System
- Feeder Hopper: The feeder hopper delivers powder into the compactor, playing a crucial role in the roller compaction process steps.
- Compaction Rollers: These compaction rollers apply mechanical force to compress powder, ensuring the formation of consistent ribbons essential for oral solid dosage forms.
- Flake Crusher/Granulator: The flake crusher/granulator mills ribbons into granules, allowing for effective size reduction and ensuring the desired properties of the final product.
- Control System (SCADA/PLC): This control system monitors roller pressure, feed rate, and compaction force, integrating PAT tools like force sensors and NIR to optimize consistency and provide real-time feedback.
Leading manufacturers often utilize these core components of roller compaction systems while considering the effect of filler type on ribbon and granule properties. Additionally, when comparing excipients used in dry granulation processes, lactose frequently emerges as a primary choice due to its favorable characteristics.
Learn the benefits of using roller compaction compared to wet granulation methods to understand how this technique can enhance efficiency and product quality in pharmaceuticals.
Step-by-Step Roller Compaction Process
1. Powder Feeding
In the step-by-step roller compaction process, powders are delivered through feeders with constant flow regulation to ensure uniformity. This is crucial for maintaining the compressibility and flowability of the materials involved.
2. Compaction into Ribbons
During the compaction into ribbons stage, rollers compress powders like mannitol and other excipients into ribbons. Roller pressure, gap, and speed are finely controlled to optimize the quality of the ribbons and to assess the impact of starch content on ribbon tensile strength and solid fraction.
3. Ribbon Milling
After compaction, ribbons are passed through a flake crusher or oscillating granulator in the ribbon milling phase to produce uniform-sized granules. This step is essential in tablet manufacturing as it ensures consistency in granule size distribution.
4. Final Blending
In the final blending stage, lubricants like magnesium stearate are added before the granules are compressed into tablets. This step enhances the lubrication properties and ensures smooth tablet formation.
By utilizing GERTEIS® technology throughout these stages, manufacturers can experience significant advantages of roller compaction over wet granulation. Additionally, it’s important to explore the technical parameters critical to the roller compaction process to achieve optimal results.
Fact Check: Growing Industry Use of Roller Compaction
According to a 2023 study by Pharmaceutical Manufacturing Journal, over 40% of solid oral dosage forms for moisture-sensitive APIs now utilize dry granulation techniques in pharma, specifically through the industry use of roller compaction. This method is essential for producing stable powder blends that maintain the desired dissolution rate while effectively managing the properties of moisture-sensitive ingredients.
The study highlights key dry granulation statistics, noting that the incorporation of excipients like microcrystalline cellulose (MCC) and starch is crucial in forming solid fractions during the granulation process. Additionally, it emphasizes the important role of talc as a glidant in dry granulation, ensuring smooth processing and uniformity in the final product.
As manufacturers continue to adopt these advanced techniques, understanding the different types of roller compactors and their advantages becomes vital for optimizing production efficiency and product quality.
Key Applications of Roller Compaction in Pharma
- High-dose APIs (Active Pharmaceutical Ingredients) using directly compressible excipients due to simplified excipient ratio
- Heat/moisture-sensitive actives (e.g., aspirin, probiotics) that require careful pellicle formation
- Modified-release tablets (with compressible coatings) utilizing specific filler comparisons, such as lactose and mannitol fillers in roller compaction
- Simplified scale-up formulations (common in generics) that leverage optimal roller compactor parameters like pressure, speed, and gap size
Comparison: Roller Compaction vs Slugging
In this roller compaction vs slugging comparison, it's essential to understand the different dry granulation methods available. Roller compaction offers advantages such as ribbon formation in dry granulation and improved tablet manufacturing efficiency due to its continuous nature. In contrast, the slugging process typically involves batch processing, which can result in irregular slugs and lower consistency in tablet quality.
When considering the scalability of these methods, roller compaction is easier to scale up while slugging may present challenges due to its reliance on larger presses. Additionally, the equipment footprint plays a crucial role; roller compactors are generally more compact and automated compared to the bulkier setups required for slugging.
Finally, effective physical properties measurement of ribbons and granules is vital in ensuring that the desired quality standards are met across both processes. Techniques such as extra-granular blending can further enhance the quality of tablets produced through these granulation methods.
Common Equipment Brands in Roller Compaction
1. Alexanderwerk – WP Series
Alexanderwerk's WP Series offers precise pressure control in roller compactors. Their modular systems support flexibility and customization for varying production needs.
2. Fitzpatrick – CCS Roller Compactors
Fitzpatrick provides a wide range of capacities in their CCS Roller Compactors, catering to both pilot and commercial-scale production.
3. Freund-Vector – TFCL Roller Compactors
Freund-Vector’s TFCL Roller Compactors are compact systems integrated with granulators, making them ideal for streamlined processing.
4. Gerteis – MACRO-PACTOR
Gerteis’ MACRO-PACTOR systems are particularly suited for high-containment roller compaction setups, often required for handling potent APIs.
These common roller compaction equipment brands are essential for various processes in the pharmaceutical industry. When selecting a roller compactor, consider key features such as precise pressure control and the ability to handle high-containment requirements, especially when processing potent pharmaceutical compounds.
Challenges and Solutions in Roller Compaction
1. Ribbon Hardness Variability
- Challenge: One of the key challenges in roller compaction is ribbon hardness variability, which can affect the consistency of the final product.
- Solution: Implement solutions for ribbon hardness variability by using servo-controlled rollers equipped with pressure feedback loops. This approach ensures precise control over manufacturing process parameters for roller compaction, such as compression force.
2. Poor Flowability Post-Granulation
- Challenge: Flowability post-granulation issues are common and can hinder efficient processing.
- Solution: To address this, consider adding flow enhancers in granulation or adjusting milling speed to reduce fines. Incorporating disintegrants may also improve flow characteristics.
3. Overheating of Rollers
- Challenge: Overheating of rollers is a frequent problem that can impact the quality of the granulate.
- Solution: Explore overheating of rollers fixes by integrating cooling jackets or establishing water circulation systems around the rollers.
4. Particle Size Variation
- Challenge: Particle size variation is another critical issue that affects uniformity in roller compaction.
- Solution: Use controlled granulators with sieve sets to narrow the distribution of particle sizes effectively. This method ensures consistent quality and helps in comparing slugging vs roller compaction techniques.
By addressing these challenges in roller compaction with targeted solutions, manufacturers can enhance efficiency and product quality. Additionally, find out how continuous processing integrates with roller compaction for efficiency while discovering methods to measure physical properties such as tensile strength.
Best Practices for Roller Compaction
- Conduct pre-blend studies to optimize excipient ratios and ensure effective excipient ratio optimization.
- Monitor compaction force closely using compaction force monitoring techniques and process analytical technology (PAT) in compaction.
- Maintain uniform particle size to avoid downstream issues; this is crucial for uniform particle size maintenance.
- Validate every stage—especially compaction force and ribbon thickness control—to ensure the integrity of the process during validation of compaction stages.
- Consider the impact of gap width on solid fraction and bulk density during roller compaction.
- When selecting types of roller compaction systems, evaluate the differences between fixed vs floating rolls.
- Explore the use of lubricants to enhance product flow and reduce friction in the compaction process.
- Learn about sustainability benefits associated with dry granulation via roller compaction.
Regulatory and GMP Guidance for Roller Compaction
Roller compaction must adhere to regulatory expectations including:
- US FDA Process Validation Guidelines for effective process validation
- EU Annex 15 qualification and validation standards to ensure compliance
- ICH Q8/Q9/Q10 quality by design principles and risk management in roller compaction
Documented controls on roller gap, force, and granule particle size distribution (PSD) are critical for validation. Ensuring proper granule PSD controls is essential for maintaining particle size uniformity and achieving GMP compliance in dry granulation processes.
Additionally, when working with potent compounds in roller compaction, it is vital to implement effective containment strategies and use personal protective equipment (PPE) to ensure safety.
Consider conducting factorial design experiments to systematically evaluate the effects of various parameters such as roll speed on the quality of the granules produced.
Finally, it may be beneficial to identify leading companies and experts involved in advanced roller compaction technologies to stay updated on best practices and innovations in the field.
Conclusion: Granulation Without Compromise
In the pharmaceutical industry, where speed, stability, and simplicity are crucial, roller compaction offers the ideal solution—dry granulation without compromise. The advantages of roller compaction in pharmaceuticals are evident: it enables the production of strong granules while keeping complete control over the process.
Whether it's a rapidly growing generic drug or a heat-sensitive groundbreaking medication, roller compaction makes processing heat-sensitive drugs more efficient. This method allows you to create sturdy granules with minimal processing, making it a vital technique in smarter pharmaceutical manufacturing.
For professionals in the pharmaceutical field, it's no longer just about avoiding water or heat—it's about embracing cleaner granulation methods and leaner manufacturing processes that guarantee quality and efficiency. In this dry granulation arena, pressure—quite literally—drives performance.
As you navigate the complexities of granulation, remember the significance of stability testing (40 °C/75% RH) to ensure that your products retain their integrity over time. Additionally, techniques such as granule particle size analysis using laser diffraction can offer valuable insights into the flowability of granules and ribbons produced during the process.
When working with highly potent drug molecules, incorporating contained engineering solutions is essential for safe processing, ensuring that both safety and effectiveness are prioritized. As you explore the potential of roller compaction in pharmaceuticals, keep in mind that this method not only streamlines production but also improves the overall quality of your pharmaceutical formulations.
In this ever-changing landscape, high shear granulation may still have its place, but we cannot ignore the advantages of roller compaction. Embrace these innovations and confidently redefine your approach to granulation.
FAQs (Frequently Asked Questions)
Q1: What is roller compaction in pharmaceuticals?
Roller compaction is a dry granulation technique in pharmaceuticals where powders are compressed between rollers to form ribbons, later milled into granules. This process is essential for moisture-sensitive API processing, as it effectively combines ingredients while minimizing exposure to heat and humidity.
Q2: When is roller compaction preferred over wet granulation?
It’s ideal when APIs are sensitive to moisture or heat, or when process simplicity and faster throughput are required. Roller compaction is a key alternative to wet granulation, especially in cases where the stability of the active ingredients might be compromised by liquid solvents.
Q3: What equipment is used in roller compaction?
Typical equipment includes roller compactors, flake crushers, feeders, and integrated control systems. This roller compaction equipment overview highlights the essential tools needed for efficient ribbon and granule formation processes in dry granulation.
Q4: Can roller compaction be used for modified-release formulations?
Yes. With proper excipient selection, roller compaction can support modified-release formulations with roller compaction that achieve sustained or delayed release profiles. This technique allows for precise control over the release characteristics of the final product.
Q5: Is roller compaction accepted by regulators?
Yes, regulatory acceptance of roller compaction is well-established in the pharmaceutical industry. Many guidelines recognize its efficacy and safety when conducted under strict quality control measures.
Q6: What is roller compaction and why is it suitable for moisture or heat-sensitive APIs?
Roller compaction is a dry granulation method that compresses powder blends between two counter-rotating rollers to form ribbons, which are then milled into uniform granules. It is ideal for moisture or heat-sensitive APIs because it does not require water or heat during the process, preserving the stability of sensitive active pharmaceutical ingredients.
Q7: What are the main advantages of using roller compaction in pharmaceutical manufacturing?
The advantages of roller compaction include eliminating the need for water and heat, simplifying the manufacturing process, achieving consistent granule density, being cost-efficient, and offering scalability. This makes it highly suitable for producing solid oral dosage forms with moisture-sensitive APIs.
Q8: How does roller compaction compare to slugging in terms of process and equipment?
Roller compaction operates in a continuous or semi-continuous mode producing uniform ribbons, whereas slugging is a batch process producing irregular slugs. Roller compaction offers easier scalability, a smaller equipment footprint, and higher tablet quality control compared to slugging's larger equipment and lower consistency.
Q9: What are common challenges encountered in roller compaction and how can they be addressed?
Challenges include ribbon hardness variability (addressed by servo-controlled rollers), poor flowability after granulation (managed through flow enhancers or milling speed adjustments), overheating of rollers (mitigated with cooling jackets or water circulation), and particle size variation (controlled using precise granulators and sieve sets).
Q10: Which equipment brands are recognized leaders in roller compaction technology?
Notable brands providing roller compaction equipment include Alexanderwerk with their WP Series, Fitzpatrick's CCS Roller Compactors, Freund-Vector's TFC Roller Compactors, and Gerteis' MACRO-PACTOR systems.
Q11: What best practices ensure optimal results in roller compaction processes?
Best practices involve conducting pre-blend studies to optimize excipient ratios, closely monitoring compaction force using Process Analytical Technology (PAT), maintaining uniform particle size to avoid downstream processing issues, and adhering strictly to regulatory and Good Manufacturing Practice (GMP) guidelines.