by Ravindra Warang
7 minutes
Wet Vs Dry Granulation: Process Comparison
Compare wet vs dry granulation in pharma. Explore pros, process steps, equipment, and when to use each method effectively.
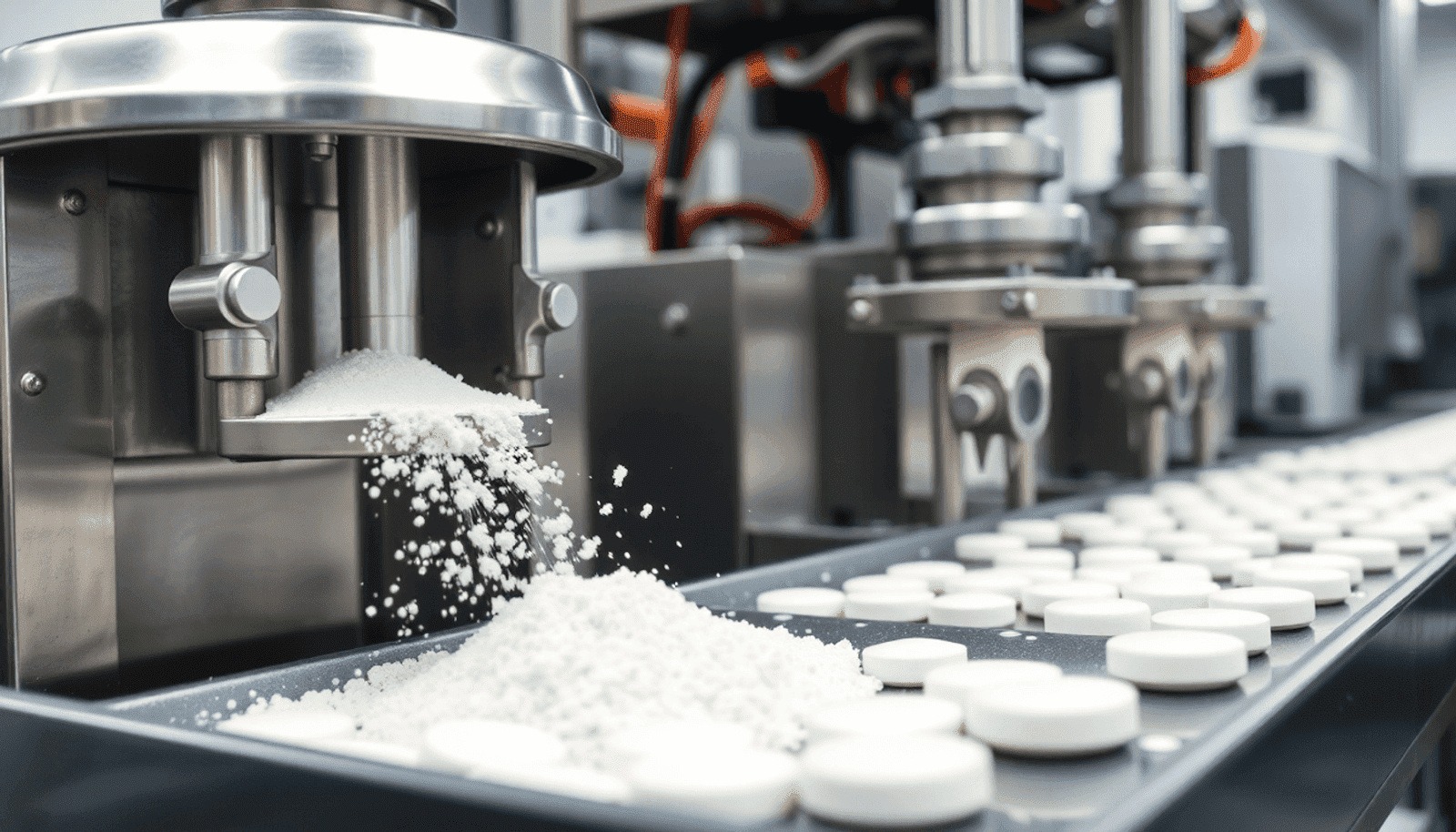
Granulation is a critical process in the manufacturing of solid dosage forms like tablets. It involves agglomerating fine powders into larger granules, which improves the flowability and compressibility of the material, ultimately leading to better tablet quality.
In the world of pharmaceuticals, there are two main methods of granulation: wet granulation and dry granulation. Each method has its own set of advantages and disadvantages, making it essential for professionals in the industry to understand their differences.
This guide aims to provide a comprehensive comparison between wet and dry granulation techniques from a pharmaceutical perspective. We will delve into key factors such as:
- Particle size distribution
- Equipment used for each method
- Formulation variables that influence outcomes
By gaining insights into these aspects, you will be better equipped to make informed decisions when it comes to tablet formulation and production.
Furthermore, we will explore how recent technological advancements have impacted best practices in pharmaceutical granulation. From fluidized bed granulators employed in batch wet granulation to pneumatic dry granulation methods, each technique brings its own set of benefits and limitations that directly affect the quality of the final tablet.
Understanding these intricacies is crucial not only for ensuring consistency in solid dosage forms but also for maintaining efficacy in drug delivery systems. Whether you are involved in product development or quality control, having a solid grasp of wet versus dry granulation will greatly contribute to your success in the field.
What is Granulation in Pharmaceuticals?
Granulation is a crucial process in the production of oral solid dosage forms such as tablets and capsules. It transforms loose powders—active pharmaceutical ingredients (APIs) and excipients—into structured, free-flowing granules. These granules are essential for ensuring dose accuracy, maintaining tablet integrity, and enhancing processing efficiency.
The two principal methods of granule formation are:
- Wet Granulation: This method uses moisture or a granulation liquid to bind particles into granules, making it ideal for moisture-sensitive APIs.
- Dry Granulation: In this technique, powders are compacted without any liquid using force, often through a roller compaction process.
Each approach offers unique benefits depending on your product’s sensitivity, production goals, and regulatory expectations. For instance, wet granulation is particularly effective in improving flowability and ensuring uniformity in the granulation process steps.
Fun Fact: According to a report by Visiongain, over 60% of oral solid dosage forms rely on granulation to meet flow and compressibility requirements. As the industry evolves, recent innovations in wet granulation technology are shaping how manufacturers approach these processes, especially when considering continuous vs batch granulation processes.
When selecting a granulation technique, it's essential to compare the pros and cons of different pharmaceutical granulation techniques while considering factors like bulk density and tensile strength of the final product.
Wet Granulation: The Industry Standard
How It Works
Wet granulation blends powder particles and introduces a liquid binder to agglomerate them. This process typically involves a high shear granulator to mix the powders thoroughly with the binder. The resulting damp mass is dried using a fluid bed dryer and then milled with an oscillating granulator before being blended into uniform granules. This method is especially effective for modified-release formulations due to its ability to enhance content uniformity and control the porosity of the final product.
Typical Equipment Used:
- High Shear Granulator
- Fluid Bed Dryer
- Oscillating Granulator
- V-Blender or Bin Blender
Advantages:
- Superior flowability and compressibility
- Enhanced content uniformity
- Ideal for modified-release formulations
- Reduces dust and improves operator safety
Limitations:
- Requires drying—adds time and energy use
- Incompatible with moisture-sensitive APIs
- May involve solvent recovery systems
When to Use:
- Low-dose or potent APIs
- Poorly flowing powders
- Controlled-release product development
Additional Considerations in Wet Granulation
When selecting binding agents for wet granulation, it's crucial to consider the properties of pharmaceutical binders and their impact on drug loading efficiency. Moreover, understanding the advantages of wet granulation compared to other methods like spray drying or steam granulation can help in making informed decisions during the formulation process.
Additionally, be aware of how granule size and shape effects on tablet making can influence the overall quality of the final product. Factors such as the impact of particle size on flowability and compressibility should also be taken into account when designing your granulation process.
Finally, if you're exploring different techniques, research pneumatic dry granulation technology benefits and limitations to determine if it aligns with your specific production needs.
Dry Granulation: Lean, Clean, and Effective
How It Works
Dry granulation uses compaction—no binder, no drying. Powders are compressed into ribbons or slugs using a roller compactor and then milled into granules with an oscillating granulator or cone mill. This process is ideal for moisture- or heat-sensitive APIs, ensuring that thermolabile drugs retain their integrity.
Typical Equipment Used:
- Roller Compactor
- Oscillating Granulator or Cone Mill
- Blenders (Pre and Post Compression)
Advantages:
- Perfect for moisture- or heat-sensitive APIs
- Shorter processing time and lower energy footprint
- Supports continuous manufacturing platforms
- Improves granule morphology compared to wet vs dry granulation methods
Limitations:
- Granules may lack uniform strength
- Less suitable for low-dose APIs without binder support
When to Use:
- Hygroscopic or thermolabile APIs
- Continuous, lean production setups
- Projects demanding rapid scale-up
Interesting Insight: Roller compaction technology, a core method for dry granulation, has grown by over 7% annually in adoption among CDMOs worldwide due to its lean footprint and scalability. This growth is partly driven by the advantages of dry granulation in maintaining tablet quality and flowability in granulated powders.
Additionally, as the industry explores new technologies like steam and dissolution processes, the comparison of wet massing vs mechanical compression methods becomes increasingly relevant. Understanding the role of binding agents such as PVP in wet granulation versus moisture-activated dry granulation is essential for optimizing formulations.
Side-by-Side Comparison Table of Granulation Methods
This comparison table highlights key features of wet granulation methods in pharmaceuticals versus dry granulation techniques. Wet granulation, often utilizing steam as a granulating liquid in steam granulation techniques, is essential for ensuring drug-excipient uniformity in tablet formulation. Conversely, dry granulation is ideal for APIs sensitive to moisture, allowing for effective segregation and maintaining integrity under varying moisture content conditions.
When choosing between these methods, it's crucial to identify challenges and limitations associated with each type of pharmaceutical granulations. Wet granulation may require extensive drying processes due to its reliance on liquid binders, while dry granulation can offer efficiency through shorter process durations—especially in settings focused on continuous versus batch processing in pharmaceutical granulation technology.
Choosing the Right Method: An Expert’s Framework
1. API Profile Analysis
Is your active pharmaceutical ingredient (API) sensitive to heat or humidity? Dry granulation, particularly through methods like roller compaction, is your ally.
2. Tablet Performance Goals
Are you aiming for strong granules or specific release characteristics? Consider wet granulation to achieve optimal tablet compression characteristics with different granulations.
3. Manufacturing Setup Considerations
If you lack a dryer or operate in a compact facility, dry granulation offers efficiency and addresses flow properties of pharmaceutical powders and granules effectively.
4. Regulatory Experience in Granulation
Some filings may benefit from the historical robustness of wet granulation due to the advantages of wet granulation in ensuring consistent particle size distribution.
In practice, hybrid granulation strategies are also emerging—blending wet and dry techniques or integrating PAT tools in granulation monitoring for real-time assessment of granule quality. Consider moisture activated dry granulation process overview and merits when exploring these options.
Conclusion: Your Granulation Journey Begins with a Choice
As the machines power up and the batch ticket prints, the formulation scientist makes the call—dry granulation wins for this moisture-sensitive drug with a tight deadline. The advantages of dry granulation are clear: improved powder flow properties and efficiency in producing solid dosage forms. But in a different scenario—a low-dose, controlled-release medication—she’d choose wet granulation without hesitation, considering the unique demands of controlled-release formulations.
Granulation isn’t just a process—it’s a precision-guided balance of science, compliance, and manufacturing strategy. Understanding the differences between wet and dry granulation techniques in pharmaceutical manufacturing is crucial. In the pharma world, your granulation process selection here doesn’t just shape a tablet—it protects a patient by ensuring tablet quality assurance and adhering to strict pharmaceutical compliance strategies.
Choose wisely, and the granulation process becomes not just a production step—but a guardian of trust, quality, and safety. Whether you're exploring high shear mixing methods or fluid bed granulation techniques, each decision shapes the efficacy and safety of the final product. Consider how novel granulation methods can enhance dissolution rate improvement and ensure that every batch meets the highest standards of quality.
FAQs
Q1: What is the main difference between wet and dry granulation?
The main differences between wet vs dry granulation lie in their processes and applications. Wet granulation uses a binder solution (often a solvent) to form granules, while dry granulation compacts powders without moisture. Each method has its own application based on formulation-specific granulation methods and the unique needs of the formulation. Understanding the differences between wet and dry granulation methods in pharmaceuticals is crucial for selecting the appropriate technique based on drug properties.
Q2: Which granulation process is faster?
Dry granulation is generally faster than wet granulation since it skips the drying phase, making it ideal for rapid turnaround in commercial settings. The speed advantages of dry granulation are particularly beneficial when working with formulations that require quick processing times.
Q3: Can PAT tools be used in granulation?
Yes, PAT tools in granulation are essential for monitoring critical parameters throughout the process. Tools such as NIR spectroscopy can effectively monitor moisture content and particle size in real time, improving consistency and ensuring that desired granule characteristics and properties are achieved.
Q4: What are the main advantages of wet granulation in pharmaceutical manufacturing?
Wet granulation binds particles with liquid, offering superior flowability, compressibility, and content uniformity. It is ideal for modified-release formulations due to its high granule strength and batch size flexibility.
Q5: What equipment is commonly used in wet granulation processes?
Wet granulation typically utilizes high shear granulators, fluid bed dryers, oscillating granulators, V-blenders, or bin blenders to achieve effective particle binding and granule formation.