by Dr. Udaykumar K. Rakibe, M.Pharm, PhD, MBA
7 minutes
Blister Packaging in Pharmaceuticals: Science, Compliance & Regulatory Risk
Explore the science, validation, and compliance of blister packaging and its critical role in pharmaceutical product integrity and patient safety.
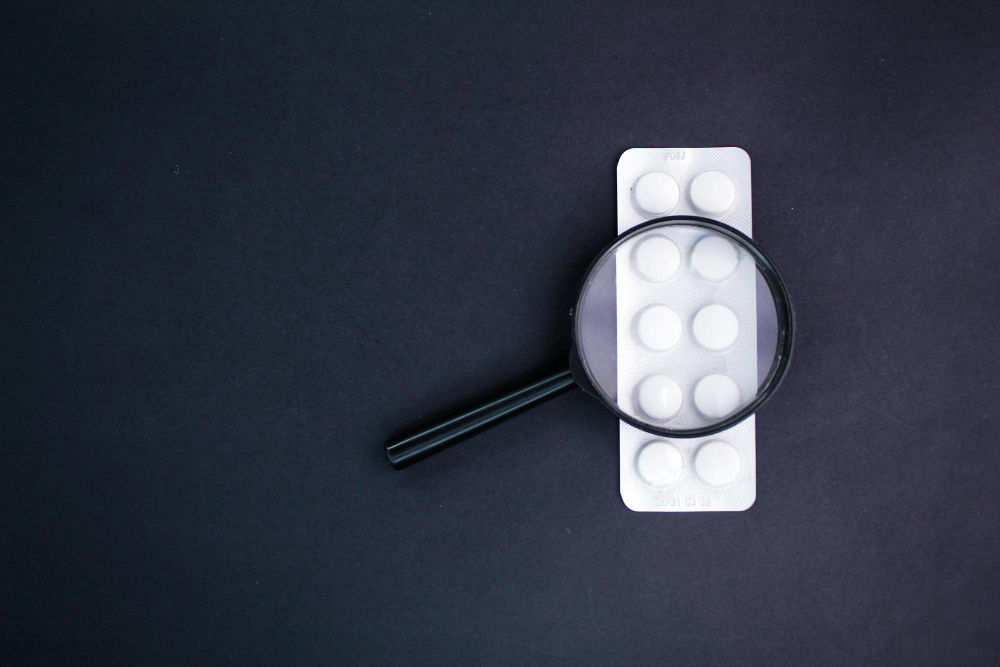
Abstract
Blister packaging plays a vital role in preserving the quality, safety, and integrity of pharmaceutical products—particularly solid oral dosage forms. With growing regulatory scrutiny on packaging operations, manufacturers must understand both the scientific foundations and compliance expectations governing blister systems. This article explores the functional purpose, material science, and technological advancements in blister packaging. It also examines how common inspectional observations often stem from overlooked or poorly validated packaging processes. A comparison with strip packaging highlights why blister formats have become the gold standard globally. To ensure inspection readiness, quality leaders must integrate robust design, validation, and control strategies across the packaging lifecycle.
1. Purpose of Blister Packaging
Blister packaging is far more than a physical enclosure. It serves as a critical control point to ensure product quality, integrity, and patient safety. Key objectives include:
- Protection: Shields drug products from moisture, oxygen, light, and external contamination.
- Dosage Accuracy: Facilitates unit-dose dispensing, minimizing medication errors.
- Tamper Evidence: Provides visible proof of tampering and unauthorized access.
- Anti-Counterfeiting & Traceability: Supports serialization and supply chain integrity.
- Convenience: Enhances usability and adherence, especially for pediatric and geriatric populations.
2. Evolution and Comparison with Strip Packaging
The Shift Toward Unit-Dose Packaging
The pharmaceutical industry has progressively moved from bulk and strip packaging toward blister formats, driven by the need for stability, compliance, and patient-centric design. While both strip and blister packs are used for tablets and capsules, blister formats dominate regulated markets due to superior protection, automation, and traceability.
Blister vs. Strip Packaging: Key Differences
3. Science Behind Blister Packaging
Blister packaging involves multidisciplinary expertise in material science, engineering, and process validation. Key scientific elements include:
1. Barrier Protection
Films such as PVDC, Aclar, and cold-form aluminum are selected based on:
- Moisture vapor transmission rate (MVTR)
- Oxygen barrier capabilities
- Light resistance (UV/IR blocking)
2. Forming Technologies
- Thermoforming: Heat and pressure shape cavities in plastic films. Offers visibility.
- Cold-forming: Mechanically forms cavities without heat. Ideal for moisture-sensitive drugs.
3. Seal Integrity
Strong seals are essential to prevent contamination and preserve drug stability. Key controls include:
- Seal strength testing
- Vacuum/dye ingress leak detection
4. Vision & Inspection Systems
Advanced cameras inspect:
- Tablet/capsule placement
- Seal defects
- Printing accuracy
These systems enable 100% online inspection, reducing manual errors.
5. Packaging and Stability Integration
Final packaging formats are aligned with ICH Q1A(R2) stability data to ensure long-term drug integrity under various environmental conditions.
4. GMP Compliance and Regulatory Expectations
Regulatory bodies (FDA, EMA, WHO) require blister packaging processes to be validated, documented, and controlled as part of the pharmaceutical quality system. Key requirements include:
- Material Qualification: Compliant with USP <661>, ICH Q3D, and other local standards.
- Seal Process Validation: Sealing temperatures, pressure, and dwell time must be optimized.
- In-Process Controls: Include line clearance, vision inspection, and reconciliation of printed components.
- Documentation & Data Integrity: Ensure traceable batch records, deviation logs, and CAPA documentation.
5. Common Blister Packaging Defects and Root Causes
1. Forming Issues
- Pinholes or Cracks: Microscopic breaches in the cavity.
- Poor Cavity Formation: Due to incorrect forming temperatures or mechanical failure.
- Distorted Blisters: From uneven heating or pressure distribution.
2. Sealing Problems
- Weak Seals: Resulting in contamination or moisture ingress.
- Seal Gaps: Incomplete sealing due to uneven heat or worn tooling.
- Overheating: Causes foil degradation or sticking.
3. Printing Errors
- Misaligned Batch Info: Poor print registration.
- Fading or Smudging: Improper drying or ink issues.
4. Product Placement Issues
- Empty Cavities: Missing tablets or capsules.
- Misaligned Products: Incorrect filling or feeding.
- Damaged Units: Broken or chipped products inside cavities.
5. Aesthetic and Visual Defects
- Scratches or Fogging: From mechanical wear or film incompatibility.
- Foreign Matter: Indicative of poor line hygiene or static control failure.
Root Causes
- Material Issues: Substandard or incompatible foils and films
- Machine Failures: Misaligned dies, improper calibration
- Environment: Temperature/humidity deviations during operation
- Human Error: Incorrect settings, failure to detect anomalies
- Product Nature: Fragile or irregularly shaped dosage forms
6. Regulatory Inspection Findings & Observations
Blister packaging-related deficiencies are frequently cited in inspections:
7. Case Studies: Recalls Due to Blister Packaging Errors
MHRA Class 2 Recall – March 2025
Product: Boots Paracetamol 500 mg Tablets
Issue: Blister foil incorrectly labeled as ‘Aspirin 300 mg’.
Impact: Medication error risk, patient confusion.
Action: Nationwide Class 2 recall within 48 hours.
Pfizer Recall – March 2023
Product: Nurtec® ODT 8-unit blister pack
Issue: Packaging failed child-resistant requirements under the PPPA.
Impact: Potential poisoning risk to children.
Action: Class-level recall of ~4.2 million units.
Risk Table: Defect Type vs. Potential Impact
8. Risk Mitigation and Best Practices
To ensure compliance and prevent costly recalls:
- Automate 100% online vision inspection for fill, seal, and print accuracy.
- Conduct regular leak testing (vacuum or dye ingress) and trend results statistically.
- Integrate complaints and deviations into CAPA systems, focusing on packaging trends.
- Revalidate sealing and inspection equipment after any material/tooling changes.
- Involve cross-functional teams (QA, Engineering, Regulatory) in packaging line control and investigations.
Conclusion
Blister packaging sits at the intersection of product protection, regulatory compliance, and manufacturing science. In an era of global supply chains and zero-tolerance for packaging failures, companies must treat blister packaging as a strategic quality function, not a routine end-stage activity.
To remain inspection-ready and globally compliant:
- Design with scientifically justified barrier materials.
- Rigorously validate sealing and inspection systems.
- Embed packaging controls into the quality management system.
By doing so, manufacturers can avoid regulatory citations, safeguard patients, and uphold product integrity from packaging line to patient use.