by Enoch Daniel
5 minutes
Environmental Control in Pharmaceutical Manufacturing
The importance of maintaining controlled environments for pharmaceutical production.
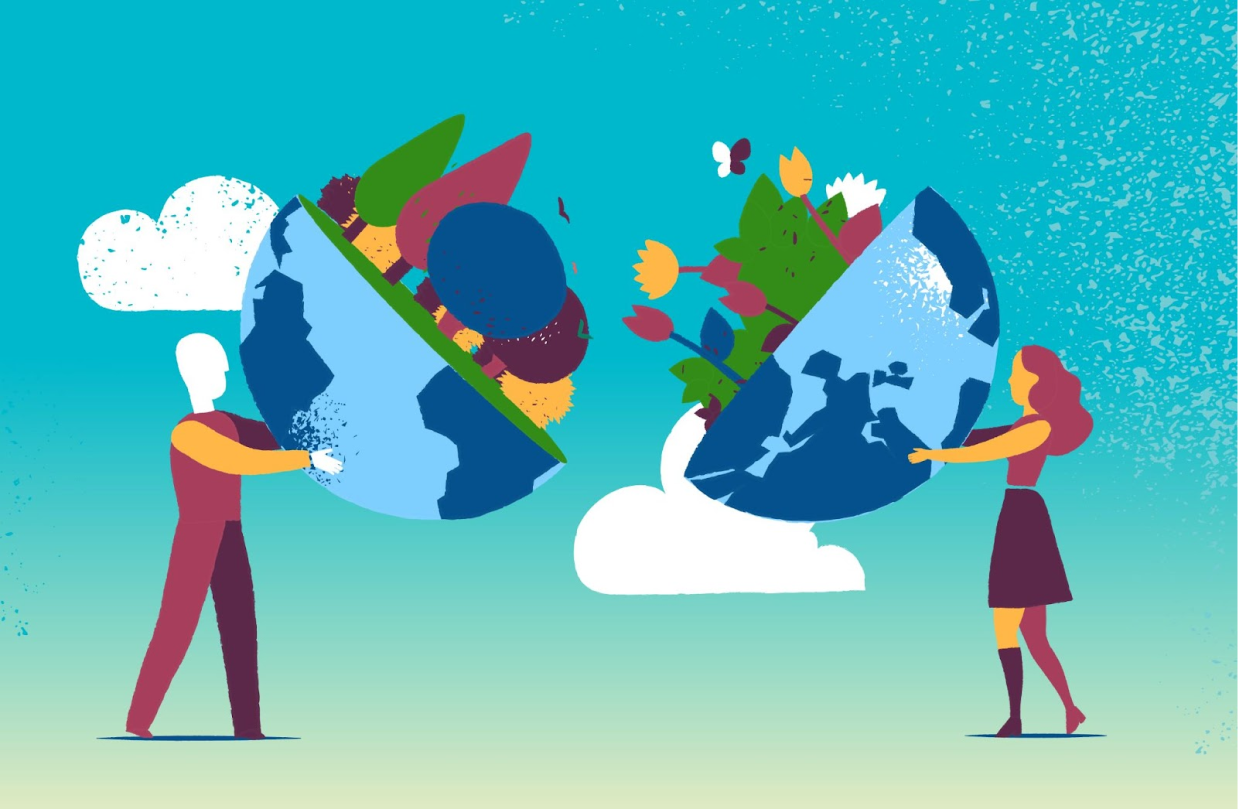
It’s often believed that pharmaceutical manufacturing is sensitive only to raw material quality and process efficiency. However, this is untrue; a more significant contribution to product quality is made by environmental control. Environmental control in pharmaceutical manufacturing refers to selecting environmental factors, such as temperature, humidity, airflow, microorganism exposure/abundance, etc., and maintaining these factors during manufacturing to obtain products with desired characteristics. Even a minor change in these environmental factors can result in a significant deviation in the product quality, quantity, purity, safety and efficacy. Here, we discuss how to ensure product safety and quality by controlling environmental parameters and the potential challenges on this path. Keep reading till the end to read answers to some of your frequently asked questions.
How does environmental control in pharmaceutical manufacturing ensure product quality and safety?
Prevents contamination
Potential contaminants can be identified by regularly sampling air, water, surfaces, equipment, etc., in the manufacturing facility. These contaminants can compromise the product quality and safety. These contaminants can also affect the process efficiency – for example, contaminants may react with the catalysts and enzymes in the facility, denaturing them and eventually affecting production efficiency.
Ensures consistent production quality
Environmental control in pharmaceutical manufacturing allows the development of consistent products. Even when the exact raw material quantities are used, the wrong humidity, temperature, or water quality can affect the product yield and quality. However, when these environmental factors are strictly regulated, a consistent and high-quality product can be replicated, allowing manufacturers to provide better products.
Prevents loss in stability
The stability of pharmaceutical manufacturing is critical because it determines its efficacy in the patient. Let’s consider an example: if a small amount of bacteria is accidentally input into the formulation during the manufacturing of a tablet. Then, this contaminated formulation is packed and sold to retailers and finally to consumers to take it. However, during this lengthy period, the bacteria are still inside the formulation and will react with it, rendering it unstable and ineffective for the consumer.
Consequently, controlled environments are strictly maintained during pharmaceutical manufacturing. Pharmaceutical companies use different techniques for environmental control.
Key environmental control techniques in pharmaceuticals
Here are some of the most common environmental control techniques in pharmaceutical manufacturing:
Develop, use, and maintain clean rooms.
Pharmaceutical companies often design and maintain clean rooms for manufacturing products. Clean rooms are designed according to specific standards, such as the ISO 14644-1 standard for clean rooms and associated controlled environments. To minimise contamination, specific air ventilation systems and growing areas are designed along these clean rooms.
Create unique environmental monitoring programs.
Environmental monitoring programs are designed specifically for individual manufacturing facilities. These programs include air, water, and surface sampling to detect contaminants. The samples are obtained from select locations across the facility and then tested to determine contaminant exposure. Realistically, some contaminants are always present in facilities; therefore, companies usually have ‘maximum allowed limits’.
Develop contamination control strategies.
Specific procedures are developed to prevent contamination of facilities. For example, aseptic techniques are designed to avoid contamination while manufacturing sterile products, and restricted access barrier systems (RABS) are developed to separate sterile products from other environments physically. These contamination control strategies are also expanded to personnel, who are provided specific uniforms or asked to work as per particular guidelines to control contamination.
Invest in personnel training programs.
As part of environmental control techniques, pharmaceutical companies often invest in personnel training programs to help their staff understand the importance of environmental control. These programs also provide detailed information on strategies that personnel can and cannot use for environmental control. Random inspections are also held to ensure staff continue to follow the learnings beyond training.
Create equipment cleaning guidelines.
Cross-contamination due to poor equipment cleaning is a real threat that can jeopardise product quality and safety. Consequently, manufacturers usually develop detailed equipment cleaning protocols that dictate when and how equipment should be cleaned. The protocols often detail the frequency of cleaning, chemicals allowed for cleaning, equipment used for cleaning, etc. Enforcing these protocols ensures there is no cross-contamination between manufacturing batches.
Create guidelines for waste disposal.
The product quality and safety can be seriously jeopardised by improper handling of waste as the waste can continue to react after disposal from the equipment, producing gases, liquids, and vapours – all of which can react with the raw material, product or equipment. Therefore, strict waste disposal protocols are designed and implemented in all facilities.
Setting up of monitoring systems.
Many manufacturers integrate monitoring systems in their facilities so that they do not need to check the environment in every aspect manually. For example, sophisticated HVAC systems, water quality monitoring systems, air quality control systems, and particulate detection systems are integrated to control the corresponding factors.
Regular auditing of all environmental control protocols.
Environmental control in pharmaceutical manufacturing is enforced using standard operating procedures (SOPs). These SOPs follow local and international guidelines, good manufacturing practices, and similar policies. However, to ensure they are updated, compliant and (most importantly!) practical, manufacturers review SOPs regularly (at least once a year). This allows them to develop new protocols or introduce changes where current SOPs fail.
However, environmental control in pharmaceutical manufacturing faces challenges despite enforcing these techniques.
Challenges facing environmental control in pharmaceutical manufacturing
High costs
Setting up and maintaining environmental monitoring systems requires a substantial upfront investment. Consequently, companies must allocate specific budgets before building facilities and every quarter/year to ensure the maintenance is up to the desired standard.
Human error
Human error cannot be easily accounted for. Even if pharmaceutical companies integrate the most advanced and efficient monitoring systems and protocols, they have to account for human mistakes, which will result in contamination. Minimising human errors is challenging, mainly because there is no general formula or solution. Consequently, companies must integrate maximum limits for all parameters to ensure they remain within the desired scope.
High personnel requirement
Companies need well-trained and expert staff to perform environmental control checks. Unfortunately, this often means they must hire permanent staff with the desired skillset or hire consultants – both expensive and require budgets. If permanent staff is employed, they also need regular training.
Conclusion
Environmental control in pharmaceutical manufacturing affects product quality and safety. Poor environmental control can result in product stability loss, product contamination, or the development of inconsistent or ineffective medication, seriously jeopardising the company’s reputation. Consequently, companies adopt various environmental control techniques, such as developing SOPs, clean rooms, and monitoring programs/systems to ensure the factory environment remains stable. However, implementing such environmental control techniques requires high costs and personnel. Unfortunately, companies should develop step-by-step plans because ecological control is a must in pharmaceutical manufacturing. Instead of allocating large budgets and making environmental control a large-scale project, it should be treated as a project with several parts. Flexibly designing monitoring systems and integrating best practices will help achieve the goal.
FAQs
1. How is environmental monitoring in pharmaceutical manufacturing achieved?
Environmental monitoring is achieved by regularly collecting and analysing samples from the facility to determine contamination levels.
2. Which environmental factors are usually monitored?
Environmental monitoring in pharmaceutical manufacturing usually includes the analysis of air and water quality, humidity, temperature, and microbial contamination.
3. Can systems be integrated for environmental monitoring in pharmaceutical manufacturing?
Yes! Most companies integrate air quality management systems, water purification systems, temperature controls, industrial humidifiers, particulate matter systems, HVAC systems, etc., to monitor and control the environment in their facilities.