by Ravindra Warang
7 minutes
High-Shear Granulator vs Fluid Bed Dryer
Compare high-shear granulator vs fluid bed dryer. Understand their roles, when to use each, and how they support pharmaceutical granulation.
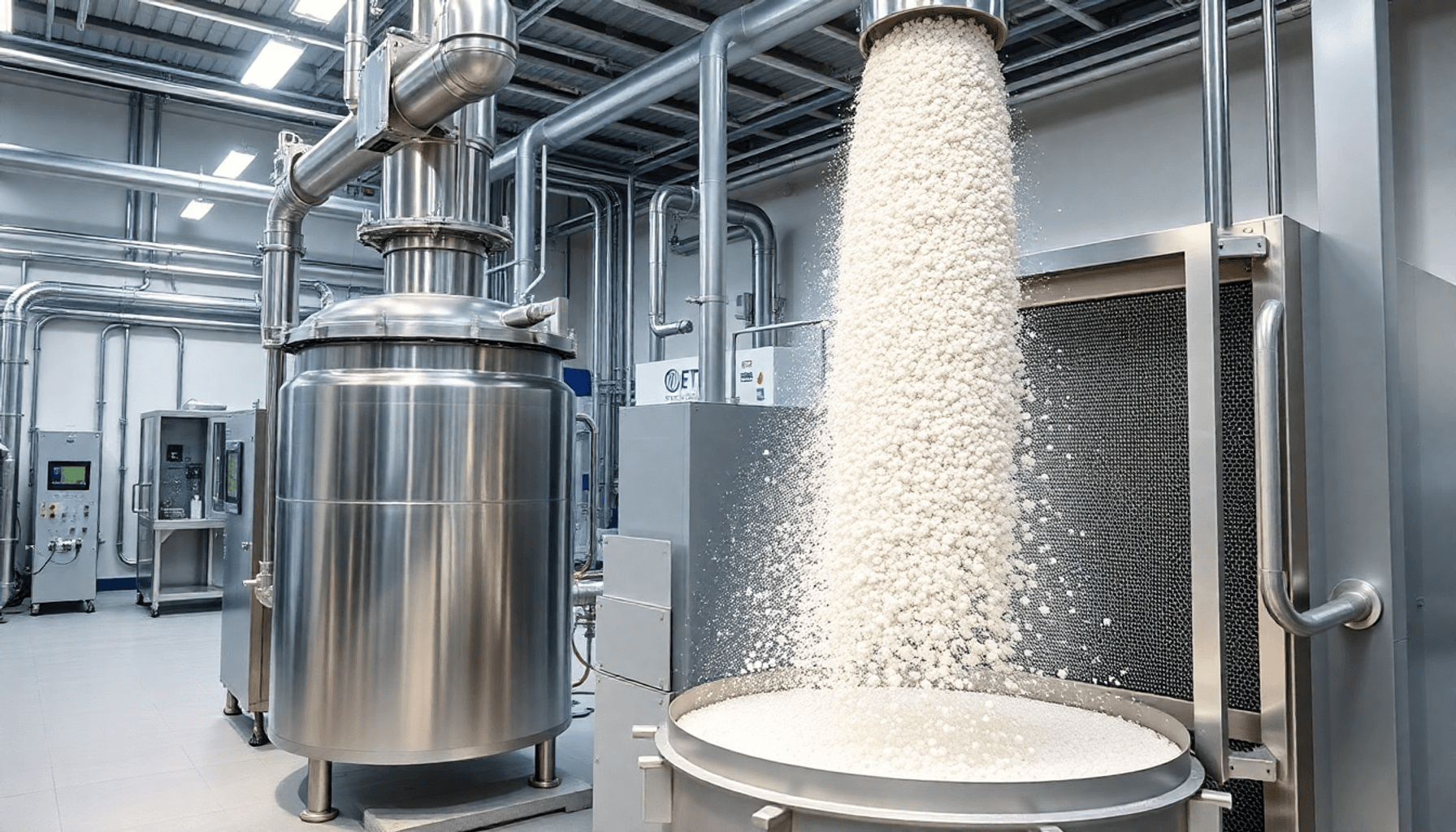
Imagine you're in a modern pharmaceutical manufacturing facility. Two machines are working together—one is mixing powders vigorously to create a wet mass, while the other is gently suspending granules in a stream of heated air. These machines are crucial for the granulation process: the High-Shear Granulator and the Fluid Bed Dryer.
In wet granulation, these machines have different roles, but they are both essential for producing immediate release solid oral dosage forms. The high shear granulator blends and mixes ingredients to form granules, while the fluid bed dryer ensures proper drying and controls particle size.
In this article, we will explore how each machine operates, when and why they are used, and what pharmaceutical professionals should consider when choosing the right technology. We will also compare high shear granulators and fluid bed dryers in pharmaceutical processes, looking at important factors like flowability measurements using the Carr index and key process parameters for fluidized-bed granulation.
What is a High-Shear Granulator (HSG)?
A High-Shear Granulator (HSG) is a specialized mechanical mixer designed to convert powder blends into wet granules using intense mixing forces and binder liquid. This process is essential in the production of modified release solid oral dosage forms.
Source: Noavaran Industries
How It Works: The HSG Working Principle
- Powders (API + excipients) are loaded into a mixing bowl.
- A central impeller rotates rapidly, forcing particles into motion and ensuring effective granule density.
- A chopper blade breaks down agglomerates and guarantees uniform distribution of the liquid binder.
- A liquid binder is added during mixing to create cohesive granules.
- The result: dense, spherical granules ready for drying that maintain optimal granule moisture content.
Key Benefits
- Excellent for formulations needing high density and compact granules, such as low-dose formulations.
- Short cycle time (5–15 minutes per batch) makes it ideal for batch production.
- Uniform binder distribution ensures consistency in controlled-release granules.
- Suitable for batch production and scalable to continuous lines, adapting to various pharmaceutical manufacturing processes.
Best Use Cases
- Low-dose formulations where content uniformity is critical.
- Poorly flowing powders that need rapid agglomeration.
- Controlled-release granules requiring specific binder levels.
Understanding the classifications of pharmaceutical manufacturing equipment related to granulation and drying is crucial for optimizing processes like those involving a High-Shear Granulator (HSG). Techniques such as scanning electron microscope (SEM) analysis can be employed to assess granule quality and ensure effective granule moisture content optimization.
What is a Fluid Bed Dryer (FBD)?
The Fluid Bed Dryer (FBD) is an essential piece of manufacturing equipment used post-granulation to gently dry wet granules using hot air. This process is critical for ensuring product stability and preventing microbial growth in the pharmaceutical industry.
Source: Senieer®
How It Works
- Wet granules are placed in a perforated bowl.
- Hot air flows upward through the bowl, suspending the granules.
- The combination of heat and airflow removes moisture uniformly, making it an effective method for powder agglomeration.
- Sensors monitor drying time, temperature, and humidity, allowing for in-line process monitoring using NIR technology.
Key Benefits
- Uniform drying prevents over-drying or burning, which is vital for maintaining the integrity of formulations.
- Rapid moisture removal due to high heat transfer ensures that granules meet desired specifications for particle size analysis.
- The FBD is compatible with spray granulation and coating nozzles, making it ideal for operations that integrate wet granulation equipment.
- Allows in-line process monitoring using NIR, ensuring consistent quality throughout the drying process.
Best Use Cases
- Heat-stable formulations requiring moisture <2% that demand strict control over the drying process.
- Granules for tablets or capsules that require consistent hardness and uniformity in size.
- Operations with integrated wet granulation and drying suites where the effect of binder spray rate on granule size distribution is a key consideration.
Core Differences at a Glance: High Shear Granulator vs Fluid Bed Dryer
Understanding the core differences between high shear granulators and fluid bed dryers is essential for effective manufacturing processes in pharmaceuticals. While the high shear granulator focuses on wet massing and granule formation through mechanical energy transfer, the fluid bed dryer specializes in drying wet granules using thermal methods. This distinction is crucial when considering granulation vs drying stages in your production line.
Additionally, factors such as batch time comparison reveal that high shear granulation typically requires only 5–15 minutes per batch, whereas fluid bed drying may take 20–40 minutes depending on the moisture content and desired end product characteristics.
When it comes to moisture handling, it's important to note that while high shear granulators may produce wet granules that require downstream drying processes, fluid bed dryers efficiently remove moisture directly from the granules due to their unique drying techniques after granulation.
Furthermore, both equipment types offer high automation capability through advanced systems like PAT integration and PLC integration in high shear granulators, while fluid bed dryers utilize SCADA controls for precise monitoring and control of the drying process.
By grasping these differences—especially regarding particle size reduction mechanisms during granulation and effective moisture management—you can better navigate FDA guidance on scale-up and post-approval manufacturing equipment changes.
Key Considerations in Equipment Selection
1. Batch Size and Throughput
- High Shear Granulators (HSGs) are ideal for high-speed granule formation in both R&D and commercial settings, especially when considering batch size and throughput.
- Fluid Bed Dryers (FBDs) come in varying bowl sizes and can handle large drying volumes, making them suitable for diverse production scales.
2. Product Sensitivity
- If your formulation is heat-sensitive, HSGs allow for short exposure to heat, effectively managing product sensitivity.
- FBDs offer temperature-controlled environments but may require gentle ramps to ensure that sensitive ingredients maintain their integrity.
3. Integration & Scalability
- Both systems can be integrated into closed, contained granulation suites, supporting integration and scalability in pharmaceutical manufacturing.
- Vendors like GEA, Glatt, and Diosna offer modular HSG-FBD units for seamless transitions, allowing manufacturers to adapt to changing requirements while identifying risk assessment requirements when changing pharmaceutical manufacturing equipment.
4. Process Analytical Technology (PAT)
- HSGs integrate torque sensors and binder endpoint detection to monitor the granulation process effectively.
- FBDs use NIR probes for real-time moisture profiling, ensuring consistent quality throughout production.
5. Equipment Operating Principles
- Understanding the equipment operating principles of both HSGs and FBDs is crucial for optimizing processes.
- Consider factors such as the angle of repose measurement and a physical properties comparison of granules from both methods to make informed decisions.
Industry Insight: Why Both Matter
According to data from Pharmaceutical Technology, nearly 75% of wet granulation lines worldwide use both HSGs and FBDs in tandem, especially in high-volume solid dosage plants. This HSG and FBD tandem use is crucial for effective granule formation and drying synergy, as it combines the unique advantages of each process.
The synergy lies in how one forms robust granules—thanks to the high-shear granulator—while the other locks in their quality by controlling residual moisture through precise management of fluidizing air velocity. This approach not only ensures consistent product quality but also aligns with the standards set by the Food and Drug Administration's Center for Drug Evaluation and Research (CDER).
Understanding the differences between high shear and fluid bed granulation is essential for optimizing these processes. While the high-shear granulator efficiently mixes ingredients and promotes granule formation, the fluid bed dryer ensures that excess moisture is carefully removed, preserving the integrity of the final product.
As such, this integrated method is a cornerstone in many solid dosage plants, where maintaining strict quality control and efficiency is paramount.
The Rise of Hybrid Systems in Pharma Facilities
Modern pharma facilities are increasingly adopting integrated granulation suites that combine high shear granulators (HSGs) and fluid bed dryers (FBDs) within a single containment system. This shift towards hybrid systems in pharma facilities offers numerous benefits, including:
- Reduced product transfer losses through efficient material handling
- Faster batch turnovers by streamlining the granulation and drying process
- Enhanced containment for highly potent APIs (HPAPIs), ensuring safety and compliance
- Single-SCADA control for both operations, simplifying process management
Leading examples of these advanced integrated granulation suites include:
- GEA’s PharmaConnect platform
- IMA Active’s Prexima + RotoCube
- Glatt’s MultiLab and TwinLab systems
These innovations not only optimize production efficiency but also allow manufacturers to implement a risk-based approach to equipment changes effectively. By understanding the differences in granule morphology produced by each method—such as the advantages of fluidized-bed granulation over high-shear mixing—pharma companies can better tailor their processes to meet specific quality standards.
Conclusion: A Dynamic Duo, Not a Competition
In the clean, climate-controlled halls of sterile pharma production, granulation harmony in pharma production is essential. Granulation isn’t about choosing one machine over the other; it’s about building a partnership between technologies.
The High-Shear Granulator delivers strength and shape, playing a crucial role in granule formation mechanisms in high shear and fluid bed processes, while the Fluid Bed Dryer ensures safety and consistency. Each plays a vital role in transforming powders into patient-ready tablets.
Whether you're setting up an R&D pilot plant or considering a full-scale facility upgrade, investing in both the high-shear granulator and fluid bed dryer—aligned with your formulation and regulatory goals—is the winning formula. This partnership ensures optimal granule size and porosity, critical factors for quality tablets.
As you navigate your product’s journey from powder to precision, remember the importance of equipment change documentation for FDA submission. Understanding process parameters influencing granulation quality in both techniques will further enhance your success.
Your product’s journey from powder to precision begins with this partnership.
FAQs (Frequently Asked Questions)
Q1: What is the main role of a High-Shear Granulator in pharma?
The main role of a High-Shear Granulator in pharma is to form wet granules from blended powders using a combination of intense mixing and binder addition. This process is essential for ensuring the proper granulation definitions and classifications, as it affects granule shape, bulk density, and the flowability of granules from different granulation methods.
Q2: Which machine is better for heat-sensitive APIs?
The High-Shear Granulator is better for heat-sensitive APIs due to its short processing time, while Fluid Bed Dryers need careful temperature control to prevent degradation of sensitive compounds.
Q3: Do both machines support PAT tools?
Absolutely. High-Shear Granulators monitor torque and endpoint effectively, while Fluid Bed Dryers use NIR and humidity sensors for moisture profiling. This PAT tools support in HSG and FBD ensures real-time monitoring and quality control throughout the manufacturing process.
Q4: High Shear Granulator vs Fluid Bed Dryer: A Comparison
Explore the high shear granulator vs fluid bed dryer comparison. Understand their pharmaceutical granulation roles and equipment selection criteria.
Q5: What is a High-Shear Granulator and what are its main benefits?
A High-Shear Granulator (HSG) converts powder blends into wet granules using intense mixing forces and binder liquid. Its benefits include producing high-density granules, short cycle times, uniform binder distribution, and suitability for low-dose formulations, poorly flowing powders, and controlled-release granules.
Q6: How does a Fluid Bed Dryer work and what advantages does it offer?
A Fluid Bed Dryer (FBD) gently dries wet granules using hot air circulation. It ensures product stability, prevents microbial growth, provides uniform drying, rapid moisture removal, and compatibility with spray granulation/coating nozzles. It's best for heat-stable formulations and granules requiring consistent hardness for tablets or capsules.
Q7: What are the key differences between High-Shear Granulators and Fluid Bed Dryers?
High-Shear Granulators perform wet massing and granule formation in the primary granulation stage using mechanical energy (impeller/chopper), taking 5-15 minutes per batch to output wet granules needing downstream drying. Fluid Bed Dryers perform drying of wet granules in the post-granulation stage using thermal energy (hot air), taking 20-40 minutes per batch to produce dried free-flowing granules by removing moisture directly. Both offer high automation capabilities but differ in energy transfer methods and process stages.