by Ravindra Warang
7 minutes
Blister Packaging & Compliance: Navigating FDA, EU GMP, and CDSCO Guidelines
A complete guide to blister packaging compliance in pharmaceuticals, covering global regulations, labeling, testing, and serialization.
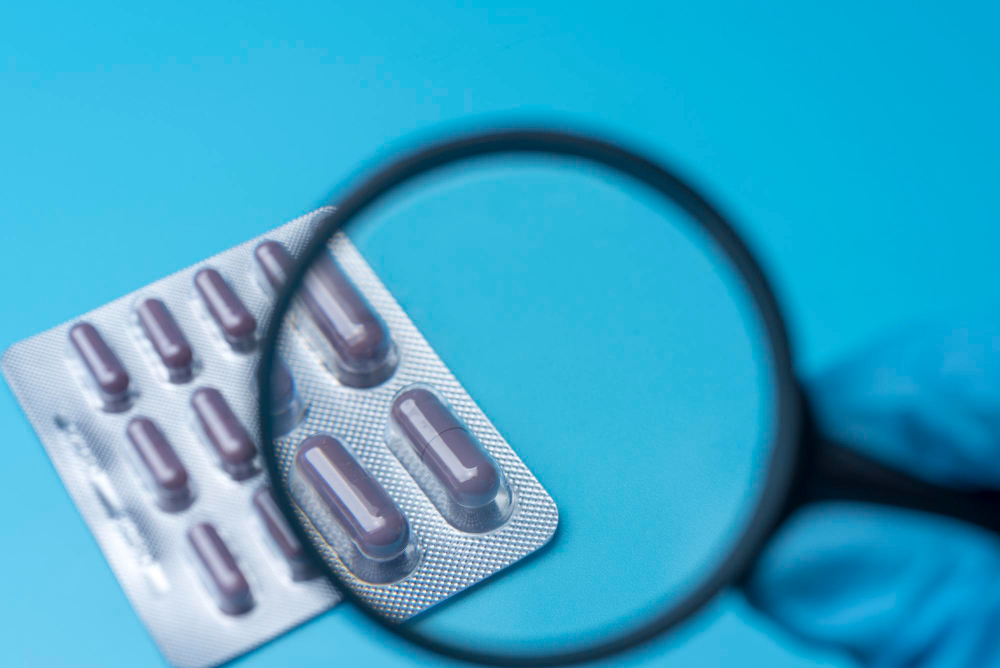
When Priya, QA lead at an Indian Pharma CRO, reviewed a batch release for a migraine medication, she noticed that the blister packaging lacked serial codes and dosage instructions. Despite the product itself meeting purity specs, this packaging discrepancy triggered a regulatory violation in packaging compliance. As a result, the Canadian import site rejected the entire carton. She spent the next week fixing labels and arranging re-shipment, delaying patient access and increasing costs due to the cost implications of packaging non-compliance.
This story illustrates a key truth: blister packaging is more than mere presentation—it is a critical compliance interface that ensures patient safety in pharmaceutical packaging. Across global markets, blister packs must align with FDA guidelines, EU GMP standards, and CDSCO regulations, or face delays, recalls, or worse.
This comprehensive guide explores how to navigate these regulations, covering technical design, testing, labeling, and inspection requirements essential for compliant pharmaceuticals. By understanding the intricacies of blister packaging in regulatory compliance, you can avoid regulatory violations in packaging and ensure adherence to global pharmaceutical packaging standards.
1. Regulatory Framework Overview
The regulatory framework for blister packaging in the pharmaceutical industry is essential to ensure compliance with stringent pharmaceutical packaging regulations. These regulations are designed to uphold pharmaceutical product safety packaging standards and guarantee the integrity of containers and closures used in various applications.
Key organizations such as the World Health Organization (WHO) provide guidelines through documents like the WHO Technical Report Series, which outlines best practices and compliance standards in pharma packaging. Additionally, the International Organization for Standardization (ISO) establishes international standards that govern the quality and safety of packaging materials.
Pharmacopoeias also play a crucial role in defining the requirements for packaging systems, ensuring that they meet specific criteria related to efficacy and safety. As such, understanding the interplay between these regulatory elements is vital for manufacturers aiming to achieve compliance and ensure the safe distribution of pharmaceutical products.
1.1 FDA (United States)
FDA primary packaging definition: Primary Packaging is defined in 21 CFR Part 201 and includes blisters in direct contact with drug substances.
Container-closure systems: The FDA’s “Container Closure Systems” guidance requires blister systems to maintain safety, functionality, and barrier performance.
Blister pack labeling rules: Labeling rules for blister packs must comply with 21 CFR 201.10—name, strength, expiration, lot number.
Tamper-evident features: Tamper-evident features are mandated under 21 CFR Part 211 and child safety packaging requirements outlined in 16 CFR 1700 (POPA.
When considering packaging for sensitive pharmaceutical products, it is essential to adhere to these regulations to ensure safety and compliance.
1.2 EU GMP
EU GMP Annex 13 (Investigational): Allows minimal artwork on primary packaging materials; supplement with secondary labels and flag labels. This ensures clarity in labeling while adhering to regulations for blister packaging in regulatory compliance.
ISO 11607: Ensure blister integrity under sterilization and storage of blister packs and during storage. This standard is crucial for maintaining product quality and safety.
GMP packaging validation: In line with ICH Q10, this process includes packaging design and closure integrity, ensuring that all aspects of labeling are compliant with industry standards. Effective GMP packaging validation is essential for production efficiency in pharma packaging.
1.3 CDSCO (India)
CDSCO Schedule M: Defines Good Manufacturing Practices in India, including packaging, material handling, and documentation. This includes specific guidelines for the use of glass containers and plastic containers in the manufacturing process.
Indian labeling requirements for pharmaceuticals: Indian label laws specify mandatory mention of generic name, form, manufacturer details, and Batch/Lot.
Import Norms: Blister packs exported must comply with WHO standards for blister packs, as well as WHO, PIC/S compliance, or EMA-equivalent standards. Additionally, it is crucial to understand the role of automated packaging in pharmaceutical regulatory compliance.
2. Material Compliance & Compatibility in Blister Packaging
FDA and WHO emphasize safety and lack of interaction between pack material and API. Ensuring material compliance in blister packaging is crucial for maintaining API compatibility with packaging materials.
Testing standards (e.g., extractables and leachables testing, WVTR/OTR, stability testing in packaging) are specified in FDA – Container-Closure Guidance and WHO Annex 9. Learn about compliance standards like GMP to ensure the integrity of your packaging materials.
3. Process Controls & Validation in Blister Packaging
In the pharmaceutical industry, effective process controls in blister packaging are essential to ensure product integrity and compliance with packaging validation processes. Adhering to GMP principles in production records is crucial for maintaining quality and ensuring that all steps meet regulatory standards.
Blister packaging plays a vital role in regulatory compliance, particularly when it comes to marketing authorization. It is important to consider the specific requirements outlined by the Drug Supply Chain Security Act (DSCSA), which includes serialization practices to enhance traceability and security within the drug supply chain.
Additionally, when using rubber closures in packaging, ensure that they meet the necessary specifications to prevent contamination and maintain product stability. Effective process controls and thorough validation processes are key components in safeguarding the quality of pharmaceutical products throughout their lifecycle.
3.1 Formation–Sealing
FDA guidelines recommend validation of seal parameters and inspection of blister edge seals to ensure seal integrity. Effective seal validation techniques are essential for maintaining quality in blister packaging..
EU Annex 13 expects traceable production records linked to Good Manufacturing Practices (GMP) and Quality Risk Management (QRM) principles. These traceable production records are crucial for regulatory compliance and ensuring adherence to pharmaceutical packaging guidelines.
Additionally, find labeling and documentation guidelines related to pharmaceutical packaging compliance to ensure that all aspects of DSCSA in pharma packaging are thoroughly addressed.
3.2 Line Monitoring & Testing
- Routine Tests for Blister Packs:
- Leak testing methods: (bubble emission, vacuum decay)
- Seal integrity inspection techniques: (visual/automated inspection)
- Periodic Tests:
- Material compatibility testing: (USP <661>/EP) - ensuring compatibility of packaging with drug substances
- Extractables and leachables analysis: (ICH Q3E)
Incorporating these testing procedures is essential for maintaining the quality and safety of pharmaceuticals, especially when using automated packaging systems like bottle filling and capping machines or cartoning and case packing machines.
3.3 Equipment Qualification
Equipment qualification for blister lines is essential and must include IQ–OQ–PQ processes as outlined in EU GMP Annex 1 requirements and FDA cGMP expectations. Stability chambers for testing are standard for accelerated stability testing (40 °C/75% RH) to ensure regulatory compliance in device packaging. These chambers play a crucial role in stability testing, allowing manufacturers to assess the integrity of blister packaging in regulatory compliance effectively. Additionally, understanding packaging functions in pharmaceuticals is vital—discover how serialization ensures traceability and combats counterfeit drugs while maintaining adherence to established guidelines.
4. Labeling Compliance & Risk Mitigation
Ensuring labeling compliance in blister packaging is crucial for meeting regulatory requirements for pharmaceutical labels. Effective risk mitigation strategies in pharma packaging not only enhance pharmaceutical labeling accuracy but also ensure traceability throughout the supply chain.
One key aspect of compliance is the implementation of serialization in pharma packaging, which helps track products and prevent counterfeit drugs from entering the market. Additionally, incorporating desiccant insertion technology can protect sensitive medications from moisture while maintaining label integrity.
As companies like Aesus lead the way in pharmaceutical packaging automation, it's essential to find solutions to reduce human error in pharmaceutical packaging processes. By adopting advanced technologies and adhering to strict labeling standards, manufacturers can effectively manage risks and ensure that their products meet all necessary regulations.
4.1 FDA Requirements
Blister packaging labels must include:
- Proprietary/generic name, strength, lot, expiration
- Adequate text size & contrast (21 CFR 201.15
- Barcode readability—foil packaging issues can cause problems.
- Compliance with pharmaceutical regulations regarding adequate labeling is crucial for the protection of pharmaceutical products.
- Ensure that labels clearly identify features of automated labeling and tamper-evident technologies for pharma products.
- Adhering to FDA labeling requirements helps maintain overall pharmaceutical labeling compliance.
4.2 EU Labeling & Annex 13
Under EU labeling requirements, primary packs may omit full labeling; however, secondary packaging labels such as “flag labels” or cartons must include essential sponsor/site information and batch codes. This is crucial for compliance with Annex 13 guidelines.
The use of pictograms in pharmaceutical packaging (e.g., sun/moon symbols for dosage forms) is encouraged to enhance clarity and understanding. Incorporating such visual elements can improve labeling requirements for pharmaceuticals and assist in guiding patients effectively.
Additionally, when considering blister packaging in regulatory compliance, it's important to ensure that all labels adhere to strict labeling and serialization systems established by the EU.
4.3 Indian Standards
CDSCO labeling rules require label data that adheres to bilingual labeling requirements, with sections in both English and Hindi.
When considering GMP compliance in packaging, blister packs may need secondary tags for exports in blister packs to ensure traceability in the pharmaceutical supply chain.
Additionally, it is essential to incorporate tamper-evident seals in pharma products to maintain data integrity and comply with FDA blister packaging guidelines.
Automated blister packaging processes can also assist in reducing human error in packaging while ensuring that all regulatory requirements are met.
5. Tamper-Evidence & Child Safety in Pharmaceutical Packaging
Blisters inherently provide tamper-evident packaging; regulatory artwork requires visible tamper statements. Understand regulatory requirements for blister packaging in pharmaceuticals is essential to ensure compliance with tampering prevention measures.
Child-resistant designs are crucial when required by regulation (especially for OTC and controlled drugs); these must meet ISO 8317 standards and CPSC. Adhering to these pharmaceutical packaging standards and regulations ensures the safety of children while maintaining product integrity.
FDA guidance recommends calendar blister packs or limited-supply packs for risk mitigation in pharmaceutical packaging. These packaging materials for medicines are designed to reduce the likelihood of accidental ingestion and ensure that dosages are taken as intended.
Incorporating tamper-evident features and child-resistant designs is essential for compliance with EU GMP blister packaging requirements.
6. Serialization, Data-Matrix Compliance & Track-and-Trace in Pharmaceutical Packaging
Source: Marchesini Group
FDA DSCSA compliance (2023): product identifier (lot + expiration) at unit-dose packaging or case level. This is crucial for ensuring effective track-and-trace systems in pharma.
EU Falsified Medicines Directive: 2D GS1 data matrix codes on unit-dose or secondary packs. These requirements are essential for maintaining pharmaceutical product stability and packaging interaction.
CDSCO packaging rules: CDSCO is working on similar serialization regulations to enhance safety and traceability in the pharmaceutical industry.
Blister packaging in regulatory compliance must have in-line camera verification and apply GS1 data matrix codes. This ensures that all products are accurately tracked and traced throughout the supply chain.
Discover best practices for selecting and testing primary and secondary packaging materials for medicines to ensure compliance with these stringent regulations.
7. Quality Risk Management (ICH Q9/Q10)
In the context of Quality Risk Management in packaging, it is essential to conduct a thorough defect risk assessment for issues such as misformed cavities, poor seals, print errors, or incorrect labels. Major risk management activities (MGAs) include:
- Batch-level defect thresholds
- OOS/OOT alert protocols
- Trends in excursion rates by line/day
Additionally, CAPA systems in pharma packaging must effectively capture pack redesigns or regulatory updates to ensure ISO 11607 compliance and adherence to FDA QSR standards. This process is crucial for maintaining quality assurance and quality control in pharmaceutical packaging.
For those looking to Explore quality assurance and control processes relevant to pharmaceutical blister packaging, understanding these standards is vital. Adhering to pharmaceutical blister packaging standards not only ensures product integrity but also safeguards patient safety.
8. Inspection Readiness & Documentation for Blister Packaging
Inspection expectations:
- EU GMP: Annex 13 compliance, QRM documentation, packaging specs
- FDA: Facility must meet FDA facility requirements by showing CCPs, control charts, deviation records
- CDSCO: Adherence to Schedule M, process reports, validation dossiers
Comprehensive site master file and batch release documentation must reference blister line protocols and include packaging documentation requirements.
Ensure that all records reflect the packaging process steps and demonstrate compliance for blister packs. Additionally, consider the containment function of packaging during inspections to guarantee inspection readiness for blister packaging.
9. Compliance Comparison: FDA vs EU GMP vs CDSCO
This compliance comparison of FDA vs EU GMP vs CDSCO highlights key differences in labeling, material testing, validation protocols, child safety regulations, and serialization requirements across regions. Understanding these nuances is essential for ensuring regulatory compliance in the pharmaceutical industry, especially when considering factors like blister packaging in regulatory compliance and the interplay between packaging and patient safety.
10. Future Trends in Compliance
- Industry 4.0 in blister packaging: Connected blister lines with real-time SPC, reducing deviations and enhancing overall efficiency.
- Smart packaging technologies: NFC/blister sensors for temperature and integrity monitoring, ensuring product safety and compliance.
- Sustainable packaging solutions: PET mono-material blisters that remain compliant while addressing environmental concerns.
- Global harmonization of standards: Evolution toward PIC/S acceptance of FDA/EU standards, aiding exports and simplifying regulatory processes.
- Learn about the functions of pharmaceutical packaging including containment and protection as these trends evolve.
- Identify types of materials used in pharmaceutical blister packaging and their compliance standards to ensure adherence to regulations.
- Understand how blister packaging contributes to patient safety and product stability in the context of these future trends in pharmaceutical compliance.
Conclusion
Blister packaging is more than a convenience—it is a compliance-critical element that bridges manufacturing, regulation, and market access. Its importance in compliance cannot be overstated, as it ensures adherence to regulatory expectations for blister packs across various industries. From material safety and barrier testing to labeling requirements, serialization, tamper-evidence, and child safety, each regulatory body sets expectations that converge on patient safety and product integrity. This is especially vital in the pharmaceutical sector, where the integrity of active pharmaceutical ingredients must be safeguarded.
For global pharmaceutical companies, mastering FDA, EU GMP, and CDSCO compliance for blister packs isn't optional—it’s foundational to effective global pharmaceutical compliance strategies. Robust systems that integrate packaging line controls and documentation are non-negotiable to avoid recalls, regulatory delays, and reputational harm. Blister packaging plays a crucial role in regulatory compliance by ensuring that pharmaceutical products meet stringent safety and quality standards while protecting them from contamination and degradation.
FAQs
1. What are the key regulatory standards that blister packaging must comply with?
Blister packaging must comply with critical regulatory standards including FDA 21 CFR Part 201, EU GMP Annex 13 and ISO 11607, and CDSCO Schedule M. These standards ensure safety, labeling accuracy, material integrity, and manufacturing compliance essential for pharmaceutical products.
2. How does FDA regulate labeling and material compliance for blister packaging?
FDA mandates that blister packaging labels include proprietary/generic names, strength, lot number, expiration date with adequate text size and contrast as per 21 CFR 201.10 and 201.15. Material compliance prioritizes safety by ensuring no interaction between pack materials and APIs, controlling plasticizers in PVC/PVDC films, barrier performance of cold-form foils, and minimizing migration risks from adhesives and inks.
3. What process controls and testing are required to ensure blister packaging quality?
FDA recommends seal parameter validation and inspection of blister edge seals for integrity. Routine tests include leak testing methods like bubble emission and vacuum decay, visual or automated seal inspections. Periodic testing involves material compatibility per USP <661>/EP standards and extractables & leachables assessments following ICH Q3E guidelines to ensure product safety and packaging performance.