by Ravindra Warang
7 minutes
Pharmaceutical Granulation Equipment Buyers Guide
A pharma expert’s guide to choosing the right granulation equipment—features, vendors, pricing, and GMP insights.
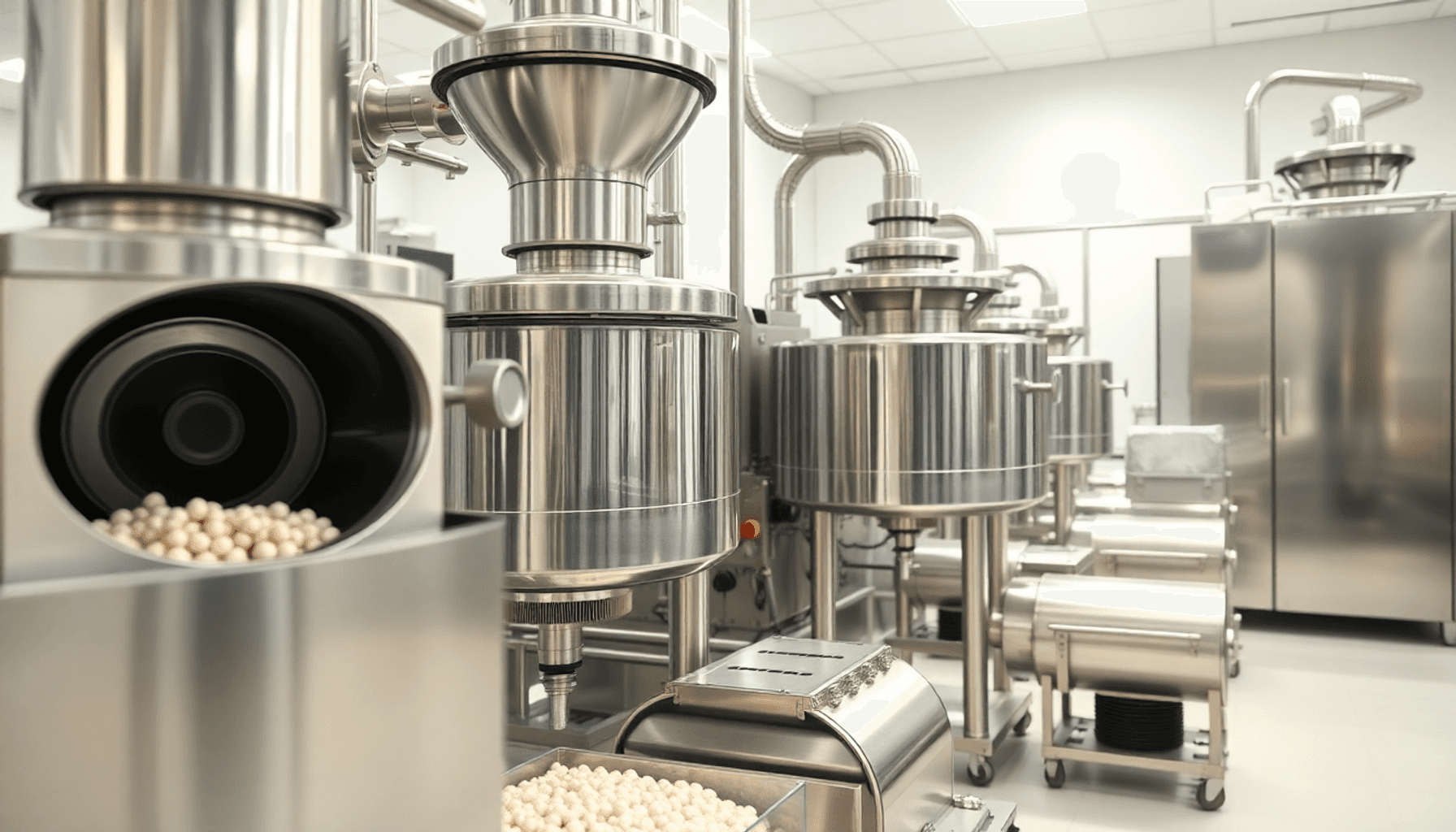
When setting up a new solid dosage manufacturing line, there are many factors to consider. You have your formulation, facility, and team in place, but there's one decision that will have a significant impact on everything else: choosing the right pharmaceutical granulation equipment. This decision is similar to selecting the engine for a race car. If you make the wrong choice, you'll encounter flow issues in tablet manufacturing and face challenges in preventing tablet defects—leading to compliance problems down the line.
This comprehensive buyer’s guide is designed to assist pharma professionals, procurement teams, and startup CDMOs in confidently navigating the process of selecting granulation equipment. We cover various types of equipment such as high-shear mixers, fluid bed dryers, and roller compactors that are essential for achieving precision in granulation, consistency in product quality, and adherence to regulatory standards in the pharmaceutical industry.
Whether you're interested in understanding the differences between wet and dry granulation methods or seeking information about automation and control systems used in pharmaceutical granulation lines, this guide has all the information you need.
In this guide, you will:
- Gain insights into the complex processes involved in forming and drying granules
- Learn how advanced technologies like pharmaceutical manufacturing automation with PLC control systems can improve efficiency
- Understand the significance of selecting the appropriate equipment for success, whether it's through dry granulation or freeze granulation techniques
1. Understanding the Granulation Equipment Ecosystem
The granulation equipment ecosystem in pharmaceutical manufacturing typically employs a sequence of machines that transform powder blends into compressible granules. This process is essential for solid oral dosage manufacturing lines and involves various techniques such as wet granulation and dry granulation. The major categories of equipment include:
- High-Shear Granulators (HSG) – Essential for wet granulation, these devices mix powders with liquids to form cohesive granules.
- Fluid Bed Dryers (FBD) – Used for drying wet granules, FBDs ensure that moisture is effectively removed while maintaining the integrity of the active pharmaceutical ingredients (API).
- Roller Compactors – These are vital for dry granulation processes, allowing the formation of granules without heat or moisture through mechanisms like thermal adhesion granulation (TAG).
- Oscillating Granulators / Cone Mills – Important for size reduction in granulation, these machines ensure uniform granule sizing and consistency in the final product.
- Blenders (Bin/V-Blenders) – Critical for final lubricant blending before compression, bin blenders ensure even distribution of excipients.
Each unit in this granulation equipment ecosystem has a specific role—choosing the right model, size, and automation level is key to ensuring output quality. Additionally, integrating advanced technologies such as cleaning-in-place (CIP) systems in pharmaceutical equipment and vacuum conveying devices can enhance efficiency and maintain hygiene standards across the production line.
When considering different approaches, it's important to weigh the benefits of comparing wet vs dry granulation techniques for pharmaceutical powder processing based on factors like product characteristics and desired end quality.
2. Key Considerations Before Buying Granulation Equipment
When exploring key considerations for buying granulation equipment, it's essential to assess various factors that influence your decision-making process:
Key Factors in Granulation Equipment Selection and Why They Matter
1. API Sensitivity
Understanding the sensitivity of the active pharmaceutical ingredient (API) is critical when selecting between wet and dry granulation methods. Characteristics such as moisture or heat sensitivity influence which approach ensures product stability and efficacy.
2. Batch Size
Batch size directly impacts equipment selection. Equipment must be capable of accommodating varying batch volumes while maintaining production efficiency. Scalability and flexibility are crucial for meeting changing production demands.
3. Automation Needs
Automation level influences the granulation process's efficiency and consistency. Choosing between minimal automation and systems integrated with SCADA (Supervisory Control and Data Acquisition) technology helps ensure tight process control and operational excellence.
4. Cleaning Validation
Proper cleaning validation is essential for regulatory compliance. Equipment should support easy and effective cleaning to minimize cross-contamination risks, especially during product changeovers.
5. Facility Layout
A well-designed facility layout supports smooth material flow, modularity, and minimal contamination risks. The placement of granulation lines should facilitate efficient operations and align with cleanroom zoning and GMP design principles.
6. GMP Compliance
Granulation equipment must meet GMP (Good Manufacturing Practice) standards to secure regulatory approvals. This ensures the system is built to deliver consistent quality, traceability, and reproducibility.
By carefully evaluating these factors, you can make informed decisions that align with your production goals and ensure the effectiveness of your solid dosage granulation line.
3. Wet Granulation Equipment: What to Look For
A. High-Shear Granulators
- Best For: Binders with aqueous/organic solvents, fast wet massing techniques
- Top Vendors: GEA (UltimaGral), IMA (ROTO MIX), Gansons (SuperGran)
- Features to Look For:
- Variable-speed impeller and chopper
- Jacketed bowl for temperature control in granulation
- CIP/SIP-ready design for cleanroom compliance
High-shear granulators are essential in pharmaceutical granulation equipment due to their efficiency in mixing and ensuring uniformity in the wet granulation process.
B. Fluid Bed Dryers
- Best For: Uniform drying of granules with minimal degradation
- Top Vendors: Glatt, ACG, Diosna, IMA Active
- Features to Look For:
- Integrated spray system (for granulation/coating)
- Explosion-proof design for solvent handling
- HEPA filters and energy-efficient airflow
Fluid bed dryers are crucial for the drying phase in the pharmaceutical production line, ensuring that granules maintain their integrity while preventing cross-contamination during processing.
Understanding the workflow of continuous versus batch processes in pharmaceutical manufacturing equipment is vital when selecting the appropriate wet granulation equipment features.
4. Dry Granulation Equipment: Roller Compactors
- Best For: Moisture/heat-sensitive APIs
- Top Vendors: Fitzpatrick (CCS), Alexanderwerk (WP series), Freund-Vector
- Key Features:
- Roller gap control with servo feedback
- Granule size adjustment techniques via oscillating granulators
- Containment options for high-potency products
Over 40% of dry granulation lines globally now use roller compactors for handling thermolabile APIs (PharmaTech 2024). This shift is part of the broader global trends in dry granulation lines, as manufacturers seek efficient solutions in the granulation process in the pharma industry.
5. Advanced Equipment Features That Add Value in Granulation
- PAT Integration – NIR sensors for real-time monitoring in granulation processes, ensuring quality control through PAT integration in pharma processing.
- SCADA Automation – Advanced SCADA automation systems for full control over parameters like torque, binder volume, and temperature during the wet granulation process.
- CIP/SIP Capability – Essential CIP/SIP capability in equipment for clean-in-place and sanitize-in-place operations, allowing faster turnaround and maintaining hygiene standards.
- Explosion-Proof Design (ATEX) – Critical explosion-proof design (ATEX) for safely handling volatile solvents in wet granulation activities.
- Batch vs Continuous Options – Exploring batch vs continuous granulation options to enhance scalability and operational flexibility within the granulation equipment sector.
6. Buying Checklist: What to Ask Your Vendor
- Is the equipment GMP compliant and does it meet 21 CFR Part 11 standards?
- Does it come with comprehensive FAT/SAT documentation and validation protocols?
- Are PAT ports pre-installed or can they be added later?
- What’s the cleaning cycle time and method for maintaining hygiene in pharmaceutical granulation equipment?
- What support is offered for installation, including training services and ongoing maintenance?
- Does it include essential safety features like safety interlocks and user-access controls?
- Is the total cost of ownership (TCO) clearly defined, including spares and AMC costs as well as energy use in granulation equipment?
7. Vendor Comparison Snapshot for Pharmaceutical Granulation Equipment
This vendor comparison for pharmaceutical granulation equipment highlights various granulation types and the unique features each vendor offers. Consider factors such as support availability in India and the specific advantages of continuous granulation technology when selecting a granulation machine. Understanding components of pharmaceutical granulation equipment for solid dosage forms is crucial for making informed decisions.
8. Budgeting Tips: What Influences Price in Pharmaceutical Granulation Equipment
- Automation Level – SCADA-integrated models cost 20–30% more due to the increased automation level impact on price.
- Material of Construction – Consider material of construction options like SS316L and Hastelloy for corrosive APIs.
- Batch Size Flexibility – Multi-size bowls for versatility add cost but increase batch size flexibility in the granulation process.
- Compliance Add-ons – Incorporating compliance add-ons in granulation equipment such as PAT, ATEX, and CIP systems increase base cost but reduce downtime effectively.
When budgeting for pharmaceutical granulation equipment, it's essential to understand how these factors interact with the fluid bed granulator/dryer/coater's efficiency and the overall wet granulation process.
Conclusion:
In pharmaceutical manufacturing, granulation isn’t just a step—it’s the foundation of product performance. Understanding the importance of granulation in pharmaceutical manufacturing is crucial for ensuring that every tablet or capsule you produce is uniform, compliant, and scalable. Selecting the right pharmaceutical granulation equipment guarantees uniformity in tablets and capsules while adhering to strict compliance in granulation processes.
This guide is your launchpad. Whether you're setting up a high-volume generics plant or considering an R&D pilot suite, understanding your granulation needs—such as conducting a thorough granulation needs assessment—and how equipment mapping for granulation processes aligns with them gives you the upper hand. Be sure to explore features and specifications of high shear granulators and fluid bed dryers to ensure they meet your specific requirements.
Buy smart. Validate thoroughly. And build a process where every granule counts, keeping in mind the scalability of granulation equipment and the essential flow properties improvement in powders that effective granulation can provide.
FAQs
Q1: What is the most important equipment in pharmaceutical granulation?
In the pharmaceutical granulation equipment overview, the high-shear granulator plays a crucial role due to its functions in mixing and forming granules. Additionally, the fluid bed dryer is essential for controlling moisture levels and ensuring uniformity in wet granulation processes. For dry granulation, roller compactors are key as they effectively compress powders and enhance compressibility through granulation.
Q2: How do I choose between wet and dry granulation equipment?
When choosing between wet and dry granulation equipment, consider factors such as API sensitivity considerations, formulation characteristics analysis, and target batch size evaluation. Moisture/heat-sensitive drugs typically favor dry granulation methods to preserve their integrity.
Q3: What vendors offer granulation equipment in India?
Top vendors of granulation equipment in India include ACG, Gansons, and Prism for local manufacturing. For global solutions, GEA, IMA, and Fitzpatrick are prominent names that supply advanced pharmaceutical granulation equipment.
Q4: What factors should be considered when selecting granulation equipment for pharmaceutical production?
Important factors include API sensitivity, batch size, automation requirements, cleaning validation protocols, facility layout constraints, and compliance with Good Manufacturing Practices (GMP).