by Ravindra Warang
4 minutes
Blister Packaging Explained: A Beginner’s Guide for Pharma Professionals
Blister packaging ensures safe, effective, and user-friendly drug delivery in pharma. Learn its types, materials, and benefits.
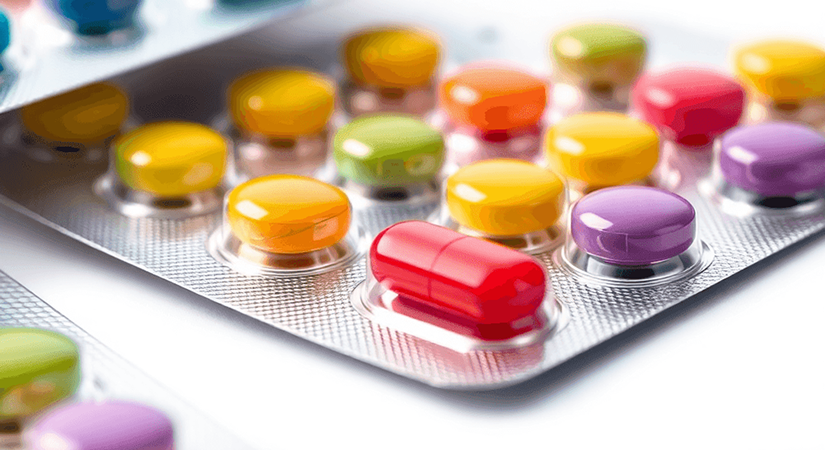
Blister packaging is an essential part of modern pharmaceutical packaging, transforming the way medications are delivered to patients securely and efficiently. This pre-formed plastic packaging system creates individual pockets for tablets, capsules, and other pharmaceutical products, ensuring each dose remains protected until it's time to use it.
The pharmaceutical industry relies heavily on unit-dose packaging to address two critical challenges:
- Patient Safety: Individual compartments prevent cross-contamination and make tampering attempts immediately visible.
- Medication Adherence: Clear organization of doses helps patients follow prescribed treatment schedules.
Blister packs offer several advantages for both pharmaceutical companies and patients:
- Protection against environmental factors (moisture, light, oxygen)
- Improved product stability and longer shelf life
- Built-in tamper evidence features
- Visual confirmation of remaining doses
- Convenient portability for patients
This packaging solution has become essential in pharmaceutical manufacturing, combining strong protection with user-friendly design to support successful medical treatments and positive patient outcomes.
Understanding Blister Packaging
Blister packaging consists of two essential components: a formable material that creates cavities or pockets, and a backing material that seals the package. These components work together to create individual compartments that protect and preserve pharmaceutical products.
Two primary types of blister packaging dominate the pharmaceutical industry: Thermoform vs Cold Form Blister Packaging
1. Thermoform Blister Packaging
- Uses heat and pressure to form plastic cavities
- Creates transparent, rigid pockets
- Common base materials include:
- PVC (Polyvinyl Chloride) film
- PVDC (Polyvinylidene Chloride) film
- PET (Polyethylene Terephthalate)
2. Cold Form Blister Packaging (Alu-Alu)
- Forms cavities through mechanical pressure
- Uses aluminum foil as the forming material
- Provides superior moisture and oxygen barrier
- Ideal for moisture-sensitive medications
The choice of materials significantly impacts product protection: Comparing blister packaging materials
- PVC Blister Film: Basic moisture barrier, cost-effective solution, suitable for stable products
- PVDC Blister Film: Enhanced moisture protection, higher oxygen barrier, used for sensitive medications
- Aluminum-Based Laminate Film: Maximum protection against moisture, complete light barrier, perfect for highly sensitive drugs
The backing material typically consists of aluminum foil, which can be coated with heat-seal lacquer to ensure proper sealing with the formed cavity material.
Why Blister Packaging Matters in Pharma
Blister packaging serves as a critical defense system in pharmaceutical product protection. The multi-layered barrier shields medications from:
- Moisture penetration
- UV light exposure
- Oxygen degradation
- Physical damage during transport
- Environmental contaminants
The individual cavity design ensures precise dose control, eliminating the risk of accidental overdose or underdose common with bulk packaging. Each blister compartment contains the exact prescribed amount, making it impossible for patients to mix up dosages.
Patient compliance reaches new levels with blister packaging's built-in features:
- Calendar markings track medication schedules
- Clear visibility of remaining doses
- Easy-to-follow progression of doses
- Portable design for on-the-go medication management
The tamper-evident nature of blister packs provides an additional layer of safety. Any attempt to breach the packaging becomes immediately visible, protecting patients from potentially compromised medications.
Pharmaceutical companies benefit from enhanced traceability through:
- Batch number printing on each blister
- Expiration date visibility
- Product authentication features
- Individual dose tracking capabilities
These security measures create an unbroken chain of accountability from manufacturer to patient, ensuring medication safety and authenticity throughout the distribution process. Serialization in blister packaging helps ensure supply chain integrity and global compliance.
Exploring Different Applications of Blister Packaging in Pharma
Blister packaging adapts seamlessly to various pharmaceutical dosage forms:
1. Tablets and Capsules
- Custom-sized cavities protect different shapes and sizes
- Push-through design enables easy dispensing
- Calendar formats track daily medication intake
2. Transdermal Patches
- Larger cavity designs accommodate patch dimensions
- Special coatings preserve adhesive properties
- Light-protective materials maintain patch efficacy
3. Clinical Settings
- Unit-dose packaging for hospital dispensaries
- Color-coded blisters for medication identification
- Tamper-evident designs for controlled substances
4. Retail Applications
- Clear visibility for product inspection
- Brand-specific designs and printing
- Child-resistant features for safety compliance
The versatility of blister packaging extends to specialized pharmaceutical products:
- Effervescent tablets with moisture-proof barriers
- Temperature-sensitive medications with enhanced protection
- Combination therapy packs with multiple drug types
These applications demonstrate blister packaging's adaptability across pharmaceutical formats, meeting specific storage and dispensing requirements while maintaining product integrity.
Smart blister packaging is also gaining popularity to support digital adherence.
Considerations for Choosing the Right Blister Packaging Solution
Selecting the best blister packaging solution requires careful evaluation of multiple factors to ensure product integrity and patient safety. Here are the key considerations:
1. Product Characteristics
- Chemical stability and sensitivity to environmental factors
- Required moisture barrier properties
- Light sensitivity levels
- Physical properties (size, shape, weight)
2. Regulatory Compliance
- Child-resistant requirements
- Material safety standards
- Market-specific regulations
- Stability testing requirements
3. Patient and Market Needs
- Target patient demographics (elderly, pediatric)
- Storage conditions in different markets
- Climate zone requirements
- Cost considerations
The selection process should balance product protection needs with practical aspects. High-barrier materials like Alu-Alu might be essential for moisture-sensitive drugs, while standard PVC could suffice for less sensitive products. For more sustainable options, manufacturers are exploring PVC-free blister packaging. The chosen solution must align with stability data, regulatory requirements, and patient usability needs while remaining cost-effective for large-scale production.
Understanding Blister Packaging Materials and Designs
Choosing the right materials is crucial for the performance of pharmaceutical blister packaging. Here's a detailed breakdown of the key components:
Forming Films
- PVC (Polyvinyl Chloride): Basic moisture barrier properties, cost-effective
- PVC/PVDC: Enhanced moisture protection, ideal for humidity-sensitive drugs
- PCTFE/PVC: Superior moisture barrier, used for highly sensitive medications
- COC (Cyclic Olefin Copolymer): High clarity, excellent moisture resistance
Lidding Materials
- Hard-tempered aluminum foil (20-25 μm)
- Paper-backed foil for enhanced durability
- Heat-sealable lacquer coatings
Barrier Properties by Material Type
Child-Resistant Features
- Push-through resistance
- Peel-push opening mechanisms
- Special scoring patterns
- Double-layer materials
The combination of these materials creates a complete barrier system. Each layer serves specific functions - from product protection to tamper evidence. To ensure integrity of these barriers, quality teams employ blister leak detection methods like vacuum decay and dye ingress.
Conclusion
Blister packaging is an essential part of modern pharmaceutical packaging design, offering significant benefits to both healthcare providers and patients. This packaging solution excels in:
- Protection: Safeguarding drug integrity through moisture barriers and tamper-evident features
- Compliance: Supporting patient adherence with clear dosage organization
- Safety: Maintaining drug stability and preventing contamination
- Versatility: Accommodating various drug delivery system designs
The pharmaceutical industry continues to improve blister packaging technology, pushing boundaries in material science and design innovation. These advancements create packaging solutions that meet strict regulatory requirements while addressing changing patient needs. As pharmaceutical companies strive for excellence in drug delivery and patient care, blister packaging remains a vital tool in their arsenal.
For deeper insights, explore the top blister packaging machine manufacturers driving innovation across the globe