by Ravindra Warang
7 minutes
Thermoform vs Cold Form Blister Packs: Which One Should You Use?
Compare thermoform vs cold form blister packs in pharma. Understand the pros, cons, use cases, and how to choose the right type for your drug product.
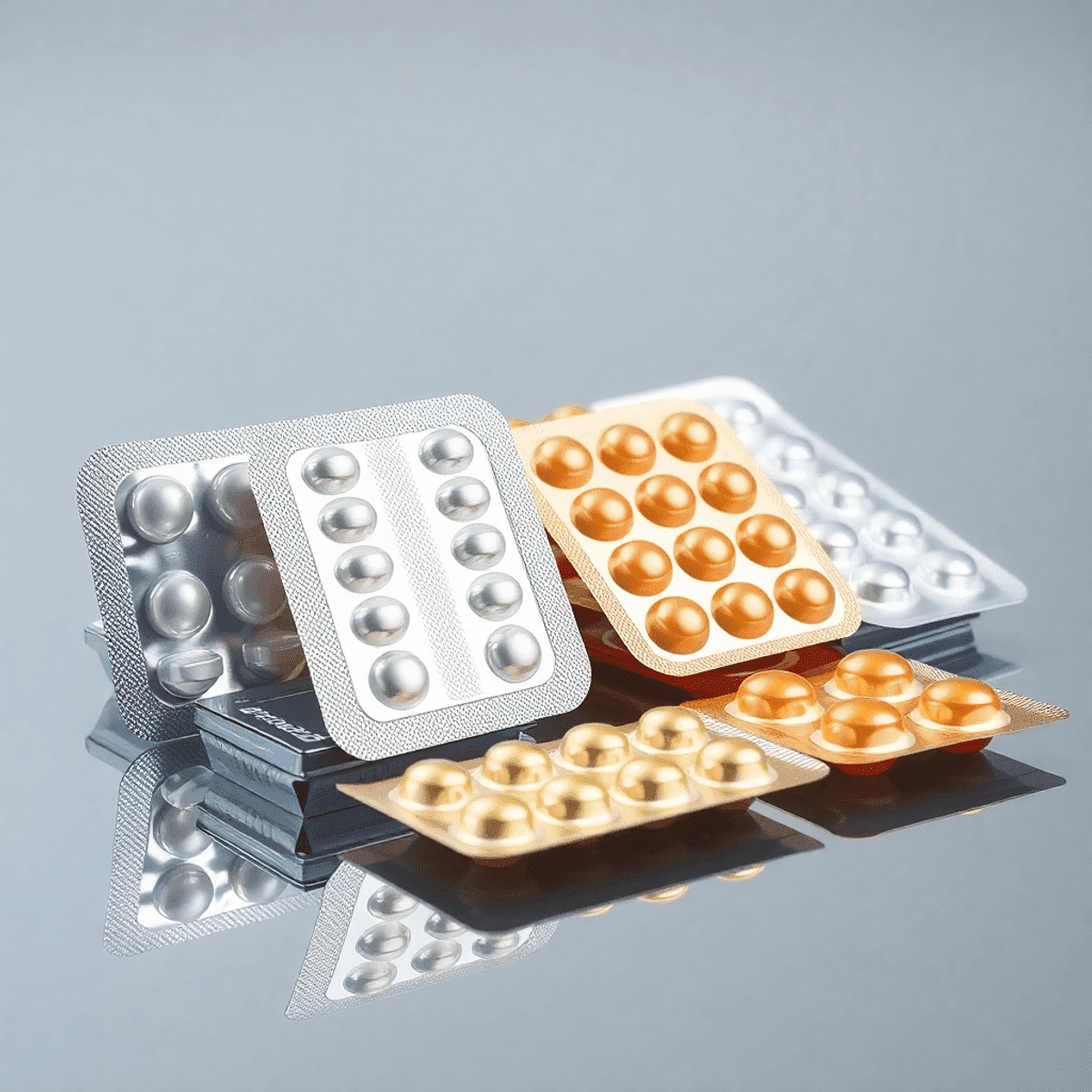
In a quiet R&D lab in Hyderabad, two packaging engineers stood at a crossroads. On the table lay two prototypes: one a sleek, transparent pack showcasing bright pink tablets — the other, a matte, opaque foil casing with no visibility of the medicine inside. “We need to decide today,” said Priya, the packaging head. “Is it going to be thermoform blister packs or cold form (Alu-Alu) blister packs?”
This is a common debate in pharmaceutical companies across the world. The choice between thermoform blister packs and cold form (Alu-Alu) blister packs isn’t just about aesthetics — it’s about shelf life, cost analysis, regulatory fit, and even patient safety.
In this guide, we walk you through this decision like you’re part of the team — understanding each format’s strengths, weaknesses, and ideal use cases in pharmaceutical packaging. Whether you’re considering blister pack comparison or looking for packaging for light-sensitive drugs, this overview will help you make an informed choice. For a deeper understanding of the fundamentals, explore our comprehensive pharma blister packaging guide.
Thermoform Blister Packaging: Speed and Visibility
Imagine molding warm plastic into perfect little cavities, filling each one with precision, and sealing it with foil — all in seconds. That’s the beauty of thermoform blister packaging.
The thermoforming process uses heat to soften plastic films such as PVC, PVDC-coated PVC, or PET, which are then formed into blisters. This method is fast and flexible, allowing for enhanced product visibility that can be a powerful reassurance to both pharmacists and patients.
Thermoform blister packaging is an essential solution in the realm of pharmaceutical packaging solutions, offering not only clarity but also important tamper-evident packaging features that ensure product safety. The use of thermoformed plastic in this process guarantees that each package is tailored to meet the specific needs of the product while maintaining integrity and effectiveness.
Whether you're looking for efficiency or reliability, thermoform blister packaging stands out as a superior choice in modern manufacturing.
When to Use Thermoform Blister Packs:
- OTC painkillers and stable prescription drugs that require protection and stability
- Multivitamins that benefit from visual inspection to ensure quality and integrity
- Products in high-volume production runs where speed and efficiency matter
- Items packaged with materials like PCTFE (polychlorotrifluoroethylene) or COC (cyclic olefin copolymers) to enhance durability, for technical comparisons, explore our PVC and PVDC packaging material comparison.
- Solutions that align with the circular economy in packaging materials by using recyclable options
Pros of Thermoform Blister Packs:
- Fast production: Thermoform blister packs are known for their efficient manufacturing process, allowing for quick turnaround times.
- Transparent packaging: The clear nature of these packs aids in patient identification, ensuring that medications are easily recognizable.
- Cost-efficient: Compared to cold form (Alu-Alu) blister packs, thermoform blister packs offer greater affordability while maintaining quality.
- Versatile materials: Made from polyethylene (PE) or polypropylene (PP), these materials enhance durability and flexibility.
- Ideal for market segmentation by material and application: Thermoform blister packs can be tailored to specific industries based on their unique requirements.
- Compatible with push-through pack (PTP) systems: Their design allows for easy integration with various packaging machinery, including heat sealing machinery.
Learn more about the top blister packaging machine manufacturers powering these systems.
Cons of thermoform blister packs:
- Lower moisture barrier: These packs often have a higher water vapor transmission rate (WVTR), making them less suitable for products sensitive to humidity.
- Light sensitivity: Without a protective coating, thermoform blister packs may not adequately shield light-sensitive drugs.
- Not ideal for sensitive drugs: The materials used, such as polyvinyl chloride (PVC), can interact with certain medications, compromising their efficacy.
- Limited tamper-evident package options: While some designs offer tamper-evidence, many basic thermoform blisters lack this essential feature.
- To enhance safety, manufacturers often adopt blister leak detection methods like vacuum decay and dye ingress.
- Consider conducting a regional market analysis for cold form blister packaging to understand better the alternatives available that address these cons. Also explore PVC-free blister packaging innovations designed to reduce environmental impact without compromising quality.
Cold Form (Alu-Alu) Blister Packaging: Total Protection
Now picture this: a sandwich of aluminum, nylon, and PVC is cold-pressed into a mold, forming a cavity that light and moisture can’t penetrate. That’s cold form (Alu-Alu) blister packaging — your go-to solution for sensitive and high-value drugs like moisture-sensitive drugs.
While slower to produce, Alu-Alu packs are unmatched in barrier protection. For drugs such as oncology tablets or biotech formulations, these aluminum blister packs act like a fortress, ensuring that the integrity of the products is maintained.
The cold forming process used in creating cold form foil (CFF) blisters guarantees superior protection against environmental factors, making them essential in the packaging of delicate pharmaceuticals. As you explore the key players in the cold form blister packaging market, consider how these innovative solutions are revolutionizing the way we safeguard vital medications.
When to Use Cold Form Blister Packs:
- Oxygen- and moisture-sensitive drugs, such as oxygen-sensitive drugs
- Hormones and antibiotics, including those used in tropical market products
- Products requiring a long shelf life of 24+ months, like thermoform blister packs and cold form (Alu-Alu) blister packs
These considerations are essential for ensuring the integrity and efficacy of sensitive pharmaceuticals in light of industry developments and innovations in blister packaging.
Pros of Cold Form Blister Packs:
- Superior barrier protection for pharmaceuticals
- Best for unstable molecules due to their unique composition of oriented-polyamide and polyethylene terephthalate (PET)
- Shelf life up to 36 months or more, making them ideal for the pharmaceutical industry
- Essential during the COVID-19 pandemic for ensuring product integrity
Understanding the difference between thermoform and cold form blister packs is crucial when selecting packaging solutions that offer optimal protection and longevity.
Cons of Cold Form Blister Packs:
- Slower production speed compared to traditional methods
- More expensive material costs due to higher quality resources
- Bulkier packaging that is fully opaque, affecting visibility
When considering options from manufacturers like Constantia Flexibles, Amcor, Bilcare Limited, Honeywell International Inc., and TekniPlex, it's essential to weigh these cons carefully. Additionally, learning about materials used in cold form blister packaging can help you make informed decisions regarding product design and cost-effectiveness.
Thermoform vs Cold Form: A Side-by-Side Battle
In this comprehensive thermoform vs cold form comparison, we will explore the key differences between thermoform blister packs and cold form (Alu-Alu) blister packs across various features.
When assessing the advantages of thermoforming vs cold forming, it's vital to consider these factors carefully. Each type of blister pack serves distinct purposes based on the nature of the product and market demands.
How One Company Balanced Both: A Packaging Strategy Case Study
A leading Indian generics manufacturer, UFlex Limited, faced a packaging dilemma with their antihistamines. These products didn’t require high protection, so they opted for thermoform packs with PVDC coating made from PVDC-coated films, effectively optimizing cost and clarity.
However, when launching a moisture-sensitive oral chemo line in Southeast Asia, they pivoted to cold form Alu-Alu packaging. This shift was driven by long transit times, the region's tropical climate, and the need for product stability. The decision to use thermoform with Alu lidding was part of a strategic blend of science, geography, and patient experience.
This case illustrates the importance of hybrid blister packaging approaches in the pharmaceutical industry, especially for companies like Liveo Research AG and R-Pharm Germany GmbH that are seeking information on pharmaceutical packaging trends and growth drivers.
So… Which One Should You Use?
When choosing between thermoform and cold form blisters, consider the following packaging decision factors:
- Choose Thermoform when cost, speed, and visual inspection matter. This option is often preferred for products where PVC blister films properties are essential for clarity and efficiency.
- Choose Cold Form when product stability and shelf life are non-negotiable. Cold form blisters are ideal for pharmaceuticals that require enhanced protection against moisture and light, making them crucial in maintaining integrity over time.
💡 Pro Tip: You don’t always need to choose. Some companies use hybrid approaches like thermoform with Alu lidding or multi-layer blister films such as PVDC-coated films to get the best of both worlds. Many are also turning to smart blister packaging solutions for patient adherence tracking and digital integration.
Still unsure? Use our Blister Packaging Checklist →
Because in pharma, packaging isn’t just protection — it’s precision, compliance, and care. Consider factors like cost vs stability in pharmaceutical packaging and explore options from key market players like Aphena Pharma Solutions, Wasdell Group, and Pack Time Innovations Pvt. Ltd. when finding key market players and competitive landscape in cold form blister market.
FAQs (Frequently Asked Questions)
What are the key differences between thermoform and cold form blisters?
The key differences between thermoform and cold form blisters lie in their production methods and material composition. Thermoform blister packs are made by molding warm plastic, typically PVC (polyvinyl chloride), into cavities using a flat-plate blister machine. This process offers fast production and transparency for easy product visibility, making it ideal for various applications, including medical blister trays.
In contrast, cold form aluminum blister packs utilize a layered sandwich of aluminum, nylon, and PVC. This method provides superior barrier protection against moisture and oxygen, which is crucial in preserving the integrity of sensitive pharmaceuticals. However, the cold form blister pack manufacturing process is slower and comes with higher costs due to the complexity of the materials involved.
When investigating sustainability practices in the pharmaceutical blister packaging industry, it's essential to consider these key differences between thermoform and cold form blisters. Understanding the advantages and limitations of each type can help manufacturers make informed decisions that balance efficiency with environmental responsibility.
- When should I choose Thermoform blister packaging for my pharmaceutical products?
Consider when to choose thermoform blister packaging for OTC painkillers, multivitamins, and stable prescription drugs where speed, cost-effectiveness, and product visibility are priorities. This type of pharmaceutical blister pack is ideal when you need fast production and easy patient identification through transparent packaging.
Thermoform blisters are particularly suitable for unit dose packaging due to their ability to protect individual doses while ensuring clear visual product display in packaging. If you're looking for alternatives that offer enhanced security, explore options like theft deterrent packaging design or clamshell packaging.
Additionally, if your products require specific safety standards, consider using medical device sterile packaging or cold form foil blister packaging for added protection against moisture and light. Vacuum-formed plastic packaging is also an excellent choice for items that need both visibility and security.
What are the advantages of using Cold Form (Alu-Alu) blister packs?
Cold Form (Alu-Alu) blister packs offer several advantages, particularly their exceptional barrier protection properties. These packs provide superior barrier protection against moisture and oxygen, making them ideal for oxygen- and moisture-sensitive drugs such as hormones and antibiotics. The low oxygen transmission rate (OTR) of cold form foil ensures that the stability of unstable molecules is maintained during storage.
When comparing thermoform blister packs and cold form (Alu-Alu) blister packs, it's essential to consider the cold form foil advantages and disadvantages. While cold form blister packs excel in protecting sensitive medications, thermoformed plastic packs may be more suitable for products that require different sealing properties or cost-effective solutions.
Additionally, when exploring manufacturing processes of blister packs, including form-fill-seal and machine types, understanding the role of multi-layer films and coatings in enhancing moisture and oxygen barrier properties is crucial. These elements play a significant role in ensuring the efficacy of the packaging.
For those looking to identify types of lidding foils and their functions in push-through packs, it's important to note how different materials can affect the overall performance of the blister packaging.
In summary, the advantages of cold form (Alu-Alu) blister packs lie in their superior protection capabilities, making them essential for preserving the integrity of sensitive pharmaceutical products.
What are the disadvantages of Thermoform blister packaging?
One of the main disadvantages of thermoform blister packaging is its moisture and light barrier limitations. These packs often have a lower barrier to moisture and light unless specially coated, making them unsuitable for highly sensitive or unstable drugs. This limitation means that they may not provide sufficient protection for products that require stringent environmental barriers.
When considering pharmaceutical packaging materials, it's essential to find information on barrier properties needed for pharmaceutical packaging materials to ensure that the chosen option meets the necessary safety and stability requirements.
Additionally, while thermoform blisters can be effective for certain applications, it's important to know how blister packs provide tamper evidence and theft deterrence for products. This aspect is crucial in maintaining the integrity of the medication and ensuring patient safety.
For those looking to understand the differences between various types of packaging, it may be helpful to investigate medical blister trays vs pharmaceutical unit dose blisters distinctions. Companies like Perlen Packaging AG, Ecobliss Pharmaceutical Packaging, and Svam Toyal Packaging Industries Pvt. Ltd. offer a range of options that vary in their barrier properties and protective capabilities.
Ultimately, when selecting blister pack materials, consider the specific requirements of the product and the environment it will be exposed to, especially if you're dealing with items that are sensitive to light or moisture. In some cases, alternatives like cold form foil may provide better protection than traditional thermoform options.
Why might Cold Form blister packs be less preferred despite their protective benefits?
Cold Form blister packs offer significant unit-dose packaging benefits due to their superior tamper resistance and protective qualities. They are also well-suited for serialization in blister packaging, ensuring traceability from production to patient. However, there are several reasons for preferring cold form blister packs despite costs. One major factor is that they have slower production speeds and use more expensive materials compared to traditional options. The blister pack materials used in Cold Form packaging often include PVDC coating for blister packs, which enhances barrier properties but also increases overall costs.
Additionally, these packs tend to be bulkier than Thermoform packs, impacting packaging efficiency considerations and logistics. When assessing consumer product packaging with blister packs, it's essential to understand the differences between thermoform and cold form blister packs to make informed decisions based on specific product requirements.
How do companies decide between using Thermoform versus Cold Form blister packaging?
In the decision-making process for blister pack types, companies balance factors like drug sensitivity, cost constraints, production speed, and the need for product visibility. For stable drugs requiring fast production and transparency, Thermoform blister packs are preferred. Conversely, for sensitive drugs that need maximum protection from moisture and oxygen, Cold Form (Alu-Alu) blister packs are chosen despite higher costs.
This balancing act between drug sensitivity and cost in packaging is crucial, especially given the market growth factors for cold form blister packaging influenced by the COVID-19 impact on pharmaceutical packaging market dynamics. Additionally, considerations around sustainability in blister packaging play an essential role, with the advantages of aluminum in blister packs offering both protection and eco-friendly options.